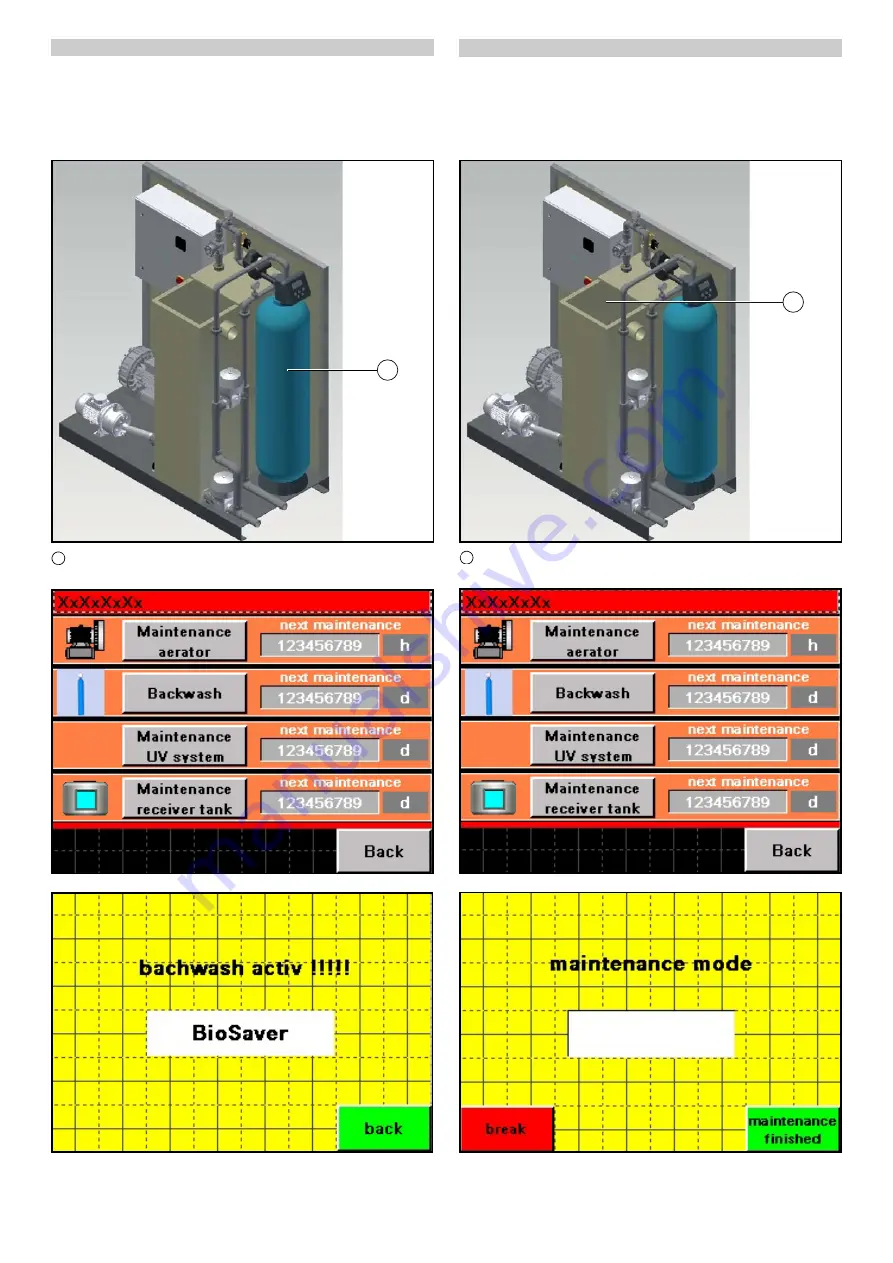
English
17
Post-treatment servicing
Note
No processed water for the washing process is provided during
the flushing period. Cleaning may only be performed when no
washing operations are being performed.
The display shows an information message when the post-treat-
ment stage needs to be flushed.
1
Backwashing
1. Touch the "Backwashing" button in the "Service" screen.
The "Backwashing" screen opens and flushing is active.
2. Acknowledge completion of flushing (after approx 15 minutes)
using the "Back" button.
Reservoir tank servicing
Note
The inlet is blocked during cleaning. Cleaning may only be per-
formed when no washing operations are being performed.
Deposits form in the processed water tank during operation. The
display shows an information message when the reservoir tank
needs to be cleaned.
1
Reservoir tank
1. Touch the "Reservoir tank" button in the "Service" screen.
The "Service Mode" screen opens.
The processed water tank is automatically drained, the immer-
sion pump in the biological stage is locked.
1
1