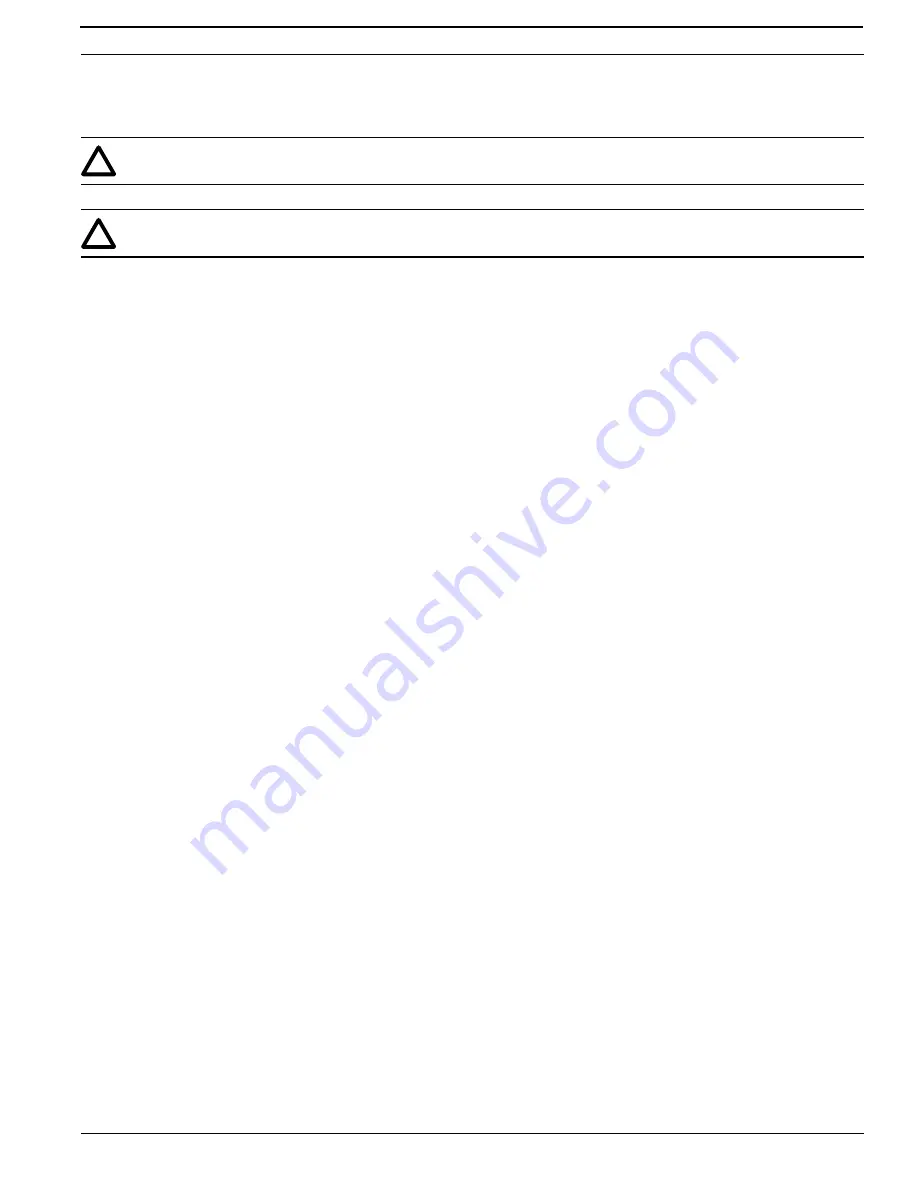
Glacia Second Stage Service & Repair Manual
15
© 2000 Aqua Lung America, Inc.
4.
Attach an
¹¹⁄₁₆
" crows-foot to a torque wrench. Thread the female end of the hose onto the inlet fitting.
While holding the inlet fitting with a 19mm (
³⁄₄
") wrench, tighten the hose to 40±2 inch-pounds.
NOTE: Before performing the following procedure, refer to Table 5, titled
"Test Bench Specifications -
Glacia 2nd Stage."
NOTE: If an accurately calibrated airflow test bench is not available, proceed to the Subjective Tuning
Procedures provided on the following page.
SECOND STAGE OPENING EFFORT TEST
1.
Connect the first stage regulator to a calibrated test bench and pressurize the system to 3000 (±100)
psi. Slowly open the flowmeter control knob (start vacuum) while watching both the magnahelic gauge
and the intermediate pressure gauge.
2.
When the intermediate pressure begins to drop, indicating the second-stage valve is open, the
magnahelic gauge should indicate an opening effort of +1.0" to +1.6" of H
2
O. If the opening effort
meets this specification, you may skip step 3 below.
3.
If the opening effort does not meet the specifications in step 2, you must readjust the crown (32). In
general, turning the crown counterclockwise (outward) will decrease opening effort and raise the lever
height; turning the crown clockwise (inward) will increase opening effort and lower the lever height.
Therefore, each time the crown is turned in either direction, the lever height must be readjusted so it
remains flush with the rim of the box bottom. The lever height is adjusted by tightening or loosening
the locknut (20). To readjust the regulator, you will need to remove the hose (35), front cover (3),
diaphragm (5) and ribbed plug (16). Refer to Disassembly Procedures, steps 1, 4, 6, 11, respectively.
a. To decrease opening effort: Turn the crown
¹⁄₄
turn counterclockwise. Attach the hose to the sec-
ond-stage and pressurize the system. Turn the locknut counterclockwise until the lever is flush with the
rim of the box bottom. Reassemble the second-stage an retest the opening effort. Repeat this step until
the opening effort meets specification.
b. To increase opening effort: Turn the crown
¹⁄₄
turn clockwise. Attach the hose to the second-stage
and pressurize the system. Turn the locknut clockwise until the lever is flush with the rim of the box
bottom. Reassemble the second-stage an retest the opening effort. Repeat this step until the opening
effort meets specification.
SECOND STAGE AIR FLOW TEST
1.
Slowly turn the flowmeter control knob until the flow reaches a minimum of 15 SCFM (425 liters per
minute). The reading on the Magnahelic gauge (inhalation / exhalation effort gauge) should indicate
no more than +6.O” H
2
O. If the reading e6.0" H
2
O, refer to refer to "Table 1 - Troubleshoot-
ing" for corrective actions.
SECOND STAGE PURGE FLOW TEST
1.
Turn off the flowmeter control knob. Next, while the second stage is still mounted on the mouthpiece
adapter, watch the flowmeter gauge and depress the purge button until the second stage valve is com-
pletely open. The flowmeter gauge must indicate a minimum of +5.0 SCFM (142 Liters per minute.). If
the purge flow is less than +5.0 SCFM, refer to "Table 1 - Troubleshooting."
2.
When purge flow is correct, remove the second-stage from the mouthpiece adapter on the flow test
bench. Shut the valve of the test bench, and purge the second stage to depressurize the system. Remove
the regulator.
Summary of Contents for GLACIA
Page 25: ...TECHNICIAN S NOTES...
Page 26: ......