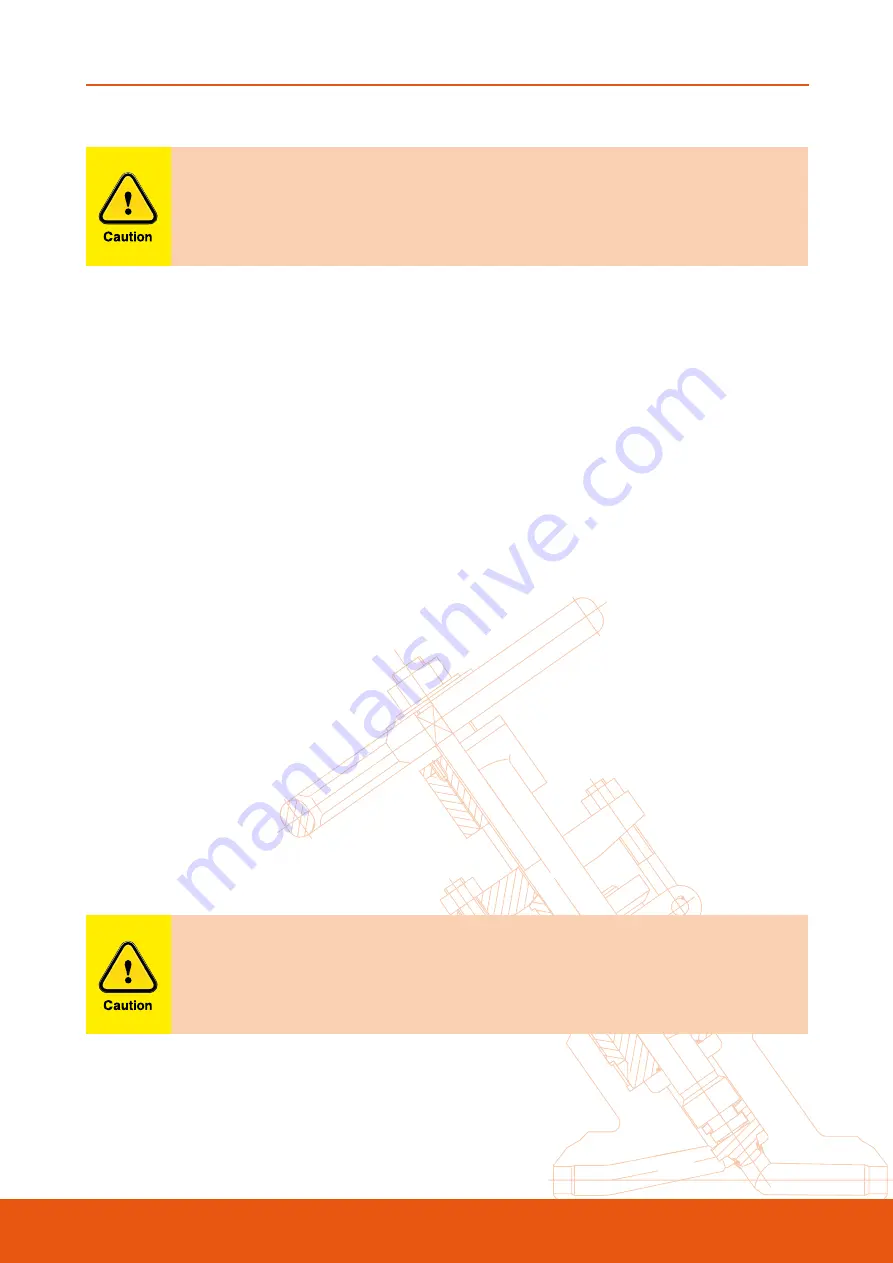
GLOBE VALVES OS & Y - FORGED - ISO 15761/API 602/B16.34
Australian Pipeline Valve - Installation, Operation and Maintenance Manual
9
Globe valves should be lightly closed during welding to prevent damage to the
seating surfaces and stem caused by thermal expansion during the weld process.
1.3.4 Buttweld Ends
In accordance with ASME B16.25 clean the weld ends as necessary and weld into the line using an
approved weld procedure. Make sure the pipe and valve body material given on the nameplate or valve
body is compatible with the welding procedure. (Refer our compatibility cross reference chart for
equivalent pipe, valve & fitting grades).
1.3.5 Valve Installation by Welding
In accordance with ASME B16.11 unless the valve contains PTFE packing and/or gasket, leave valves
assembled and in the lightly closed position during installation, welding and post-weld heat treatment.
This will prevent the valve seat from floating or distorting during the process. After welding completion,
open the valve and flush line to clean out any foreign matter.
Valves under 40mm (1 1/2”) containing PTFE packing and/or gasket must be dis-assembled for installation
as the welding temperature can adversely affect the PTFE components. Remove the bonnet and bonnet
gasket and match mark each component during disassembly for proper reassembly.
If you do not disassemble valves it will be the responsibility of the operator to ensure valves are kept cool
during welding and then post-weld testing of the valve should be performed. Larger size valves over
65mm NB are less likely to transmit heat to bonnet and stem packing during welding but still care should
be taken.
The responsibility for welding of the valves into piping systems is that of those performing the welding.
Refer to ASME B31.1, B31.3 etc. Written welding procedures covering all attributes of the process and
materials to be welded shall be in accordance with Section IX of the ASME Boiler and Pressure Vessel Code
and any additional requirements from the applicable piping code including any possible necessary
localized PWHT depending on material specifications.
APV forged globe valves do not run the risk of seat loosening during welding due to
the fact that they are supplied with integral Stellite body seats.
Subsequent to welding, clean and inspect the finished weld(s) and, if necessary, repair any defects using
a qualified weld repair procedure. In addition, cycle the valve open-closed to check for proper operation,
making sure no binding has occurred due to the weld heat.