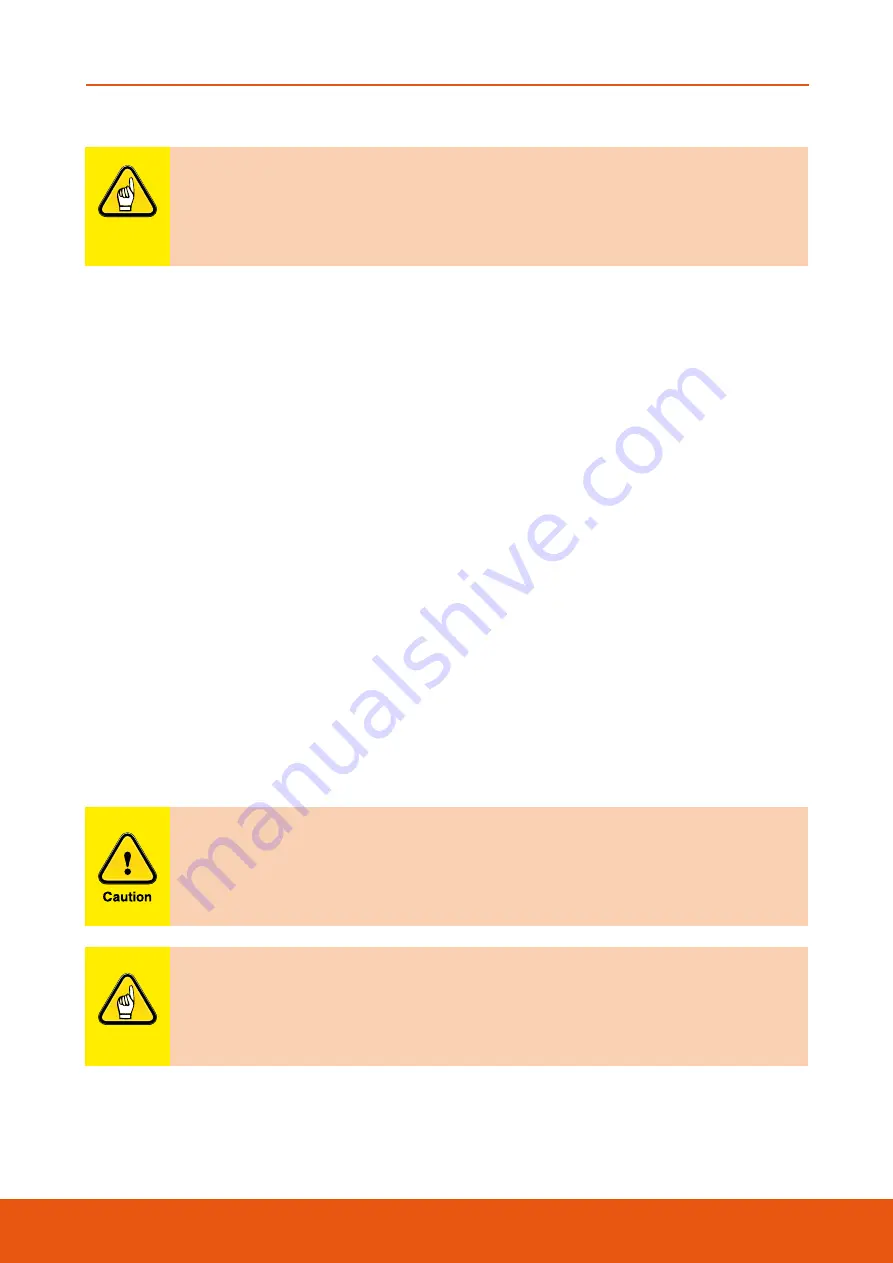
GLOBE VALVES OS & Y - FORGED - ISO 15761/API 602/B16.34
Australian Pipeline Valve - Installation, Operation and Maintenance Manual
20
Note
The stem packing style will vary according to valve size, type and class as well as
the stem packing material specified. Examples include combination sets, wire
reinforced braided packing, PTFE Chevron moulded sets, live loaded sets.
4.3 BONNET DISASSEMBLY & STEM REPLACEMENT/REPAIR
Before disassembly:
1. Check that the line is in a complete shut down phase then remove the valve from the line.
2. Pre-order all necessary spare gland packings and jointing gaskets.
3. Open the valve slightly by turning the handwheel anti-clockwise and loosen the gland.
4. Put identification marking on valve body, bonnet, disc, yoke and actuator. This helps to avoid
mismatching of parts at the time of re-assembly.
5. If the bolts and nuts are too tight, apply deep penetrating oil then unscrew.
Refer Sections 4.3.1 & 4.3.2 for removing and replacing the bonnet & gasket.
To replace or repair the stem when the valve is completely disassembled for general maintenance first
see Section 4.3.1 then follow this procedure:
• Open valve half way then remove bonnet bolts and nuts.
• Lift up the bonnet to remove disc. The disc has to be reassembled in the same position as originally
assembled.
• Remove hand wheel then turn stem to release it from the yoke nut and remove from stuffing box.
• Check condition of back seat bushing for seizure marks. If apparent, order replacement parts.
• Remove stem packing.
• Remove stem. Remove disc from stem which may be threaded or keyed and may have a retaining
clip or tack weld which can be removed.
Always be sure that the valve is de-pressurised and isolated prior to performing
any maintenance work. Do not attempt to repair valve in-line if volatile, dangerous,
hazardous or flammable service.
Note
Welded bonnet valves can be replaced but otherwise are not repairable.