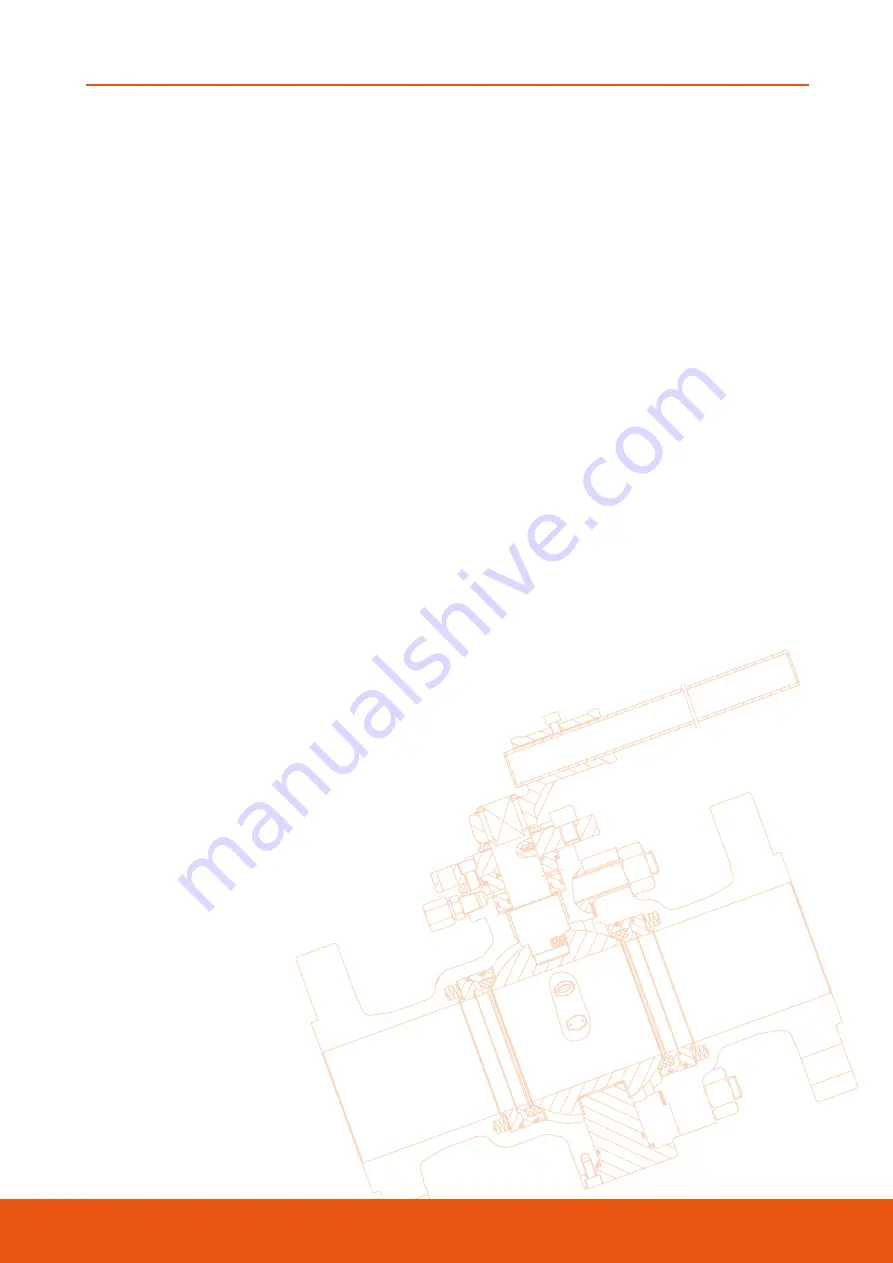
SIDE ENTRY 2P TRUNNION BALL VALVES API6D STANDARD - FS9000 SERIES
Australian Pipeline Valve - Installation, Operation and Maintenance Manual
7
• We recommend you tropicalise bore and ends of valves if stored in humid or salt air environment.
Grease bore with valve full open so no grease is applied to soft seat inserts.
1.3 ENVIRONMENTAL CONSIDERATIONS
According to ISO 14000 regulations and the environmental policy of APV the recyclability of the
components that form part of APV valves is as follows:
Recyclable components:
Metal parts, PTFE (hard), plastic plug (low-density polyethylene).
Non-recyclable components:
PTFE mixed with other compounds (glass-fiber, graphite, etc.), nylon, graphite and graphite mixed with
metal.
2 . 0 I N S T A L L A T I O N
2.1 VALVE PREPARATION
a- Remove the ends protectors and check accurately the status of the valve as indicated in point 1.2.
b- Prior to shipment, a preservative/corrosion inhibitor may have been applied to the inner body of the
valve. This preservative/corrosion inhibitor can be removed with a solvent, provided the solvent used
does not affect the seats/seals used in the valve.
c- Do not operate the valve until the following procedures have been fully applied:
• Clean internal conduits.
• After cleaning the ball must be operated (one complete stroke).
• During installation the ball must be kept in the fully open position.
2.2 VALVE INSTALLATION
a- To handle the valve use body lugs if applicable or suitable eyebolts. Never handle the valve by yoke or
using the lever or actuator or gear box eye bolts. Never lift from bore of valve.
Do not lift the valve
using only one lifting lug.
b- The end protectors must be removed only immediately before installation. If one of end is not
connected to the line for a period of longer than half a day the opened end shall be securely sealed
with plastic or wooden cover.
c- For butt weld type valves take care for the following: If brushing or grinding, seal valve conduit (bore)
to prevent damage. At the end of such operation clean accurately the conduit. The welding procedure
and post-weld treatment shall be performed taking into account the allowable maximum temperature
for seats and seals. The welding sequence shall be pre-planned in order to give an acceptable piping
load to the valve. Leave valve in full open position to reduce temperature transmission to soft seats for
valves up to 80 NB (3”) use temperature measuring strips. Ensure temperature of body does not go
above 180
°
C.