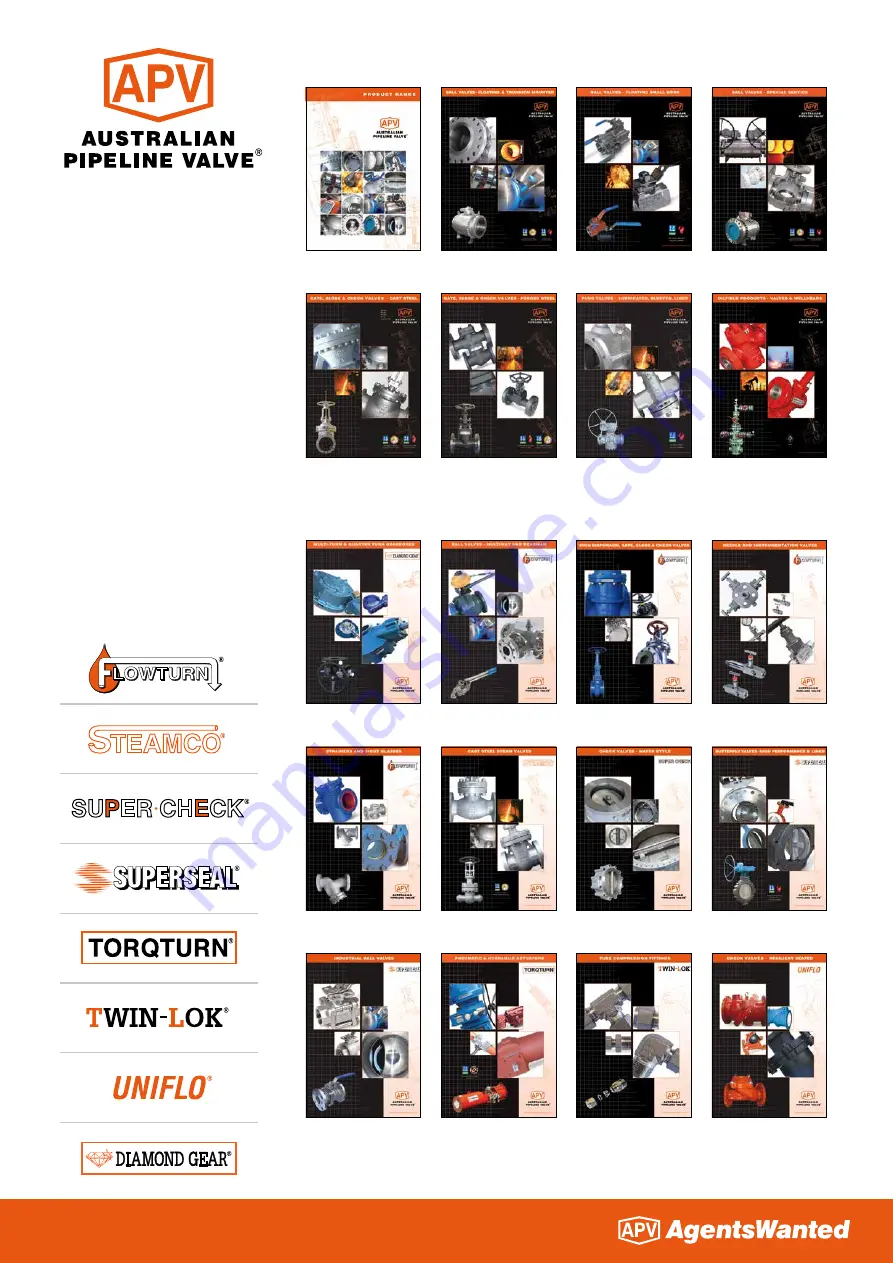
View our catalogues at www.australianpipelinevalve.com.au
AUSTRALIAN PIPELINE VALVE BRAND RANGE - CATALOGUES
APV FAMILY OF BRANDS RANGE - CATALOGUES
COMPLETE
PRODUCT LINE
“Australian Pipeline Valve
produces isolation,
control and flow reversal
protection products for
severe and critical service
media in utility, steam,
pipelines, oil & gas
and process industries.
APV valves and pipeline
products form the most
competitive portfolio
in the market.”
Oilfield Products
Valves & Wellheads
Gate, Globe & Check
Valves - Forged Steel
Plug Valves Lubricated,
Sleeved & Lined
Gate, Globe & Check
Valves - Cast Steel
Diamond Gear
Gearboxes
Flowturn Gate, Globe
& Check Valves
Flowturn
Instrument Valves
Flowturn Ball Valves
Multiway & Deadman
Flowturn Strainers
& Sight Glasses
Supercheck
Wafer Check Valves
Superseal
Butterfly Valves
Steamco
Steam Valves
Superseal
Industrial Ball Valves
TwinLok Tube Fittings
Uniflo Check Valves
Torqturn Actuators
Ball Valves Floating
& Trunnion Mounted
Ball Valves
Floating Small Bore
Ball Valves
Special Service
Product Brochure
Contact us for your local stockist/distributor