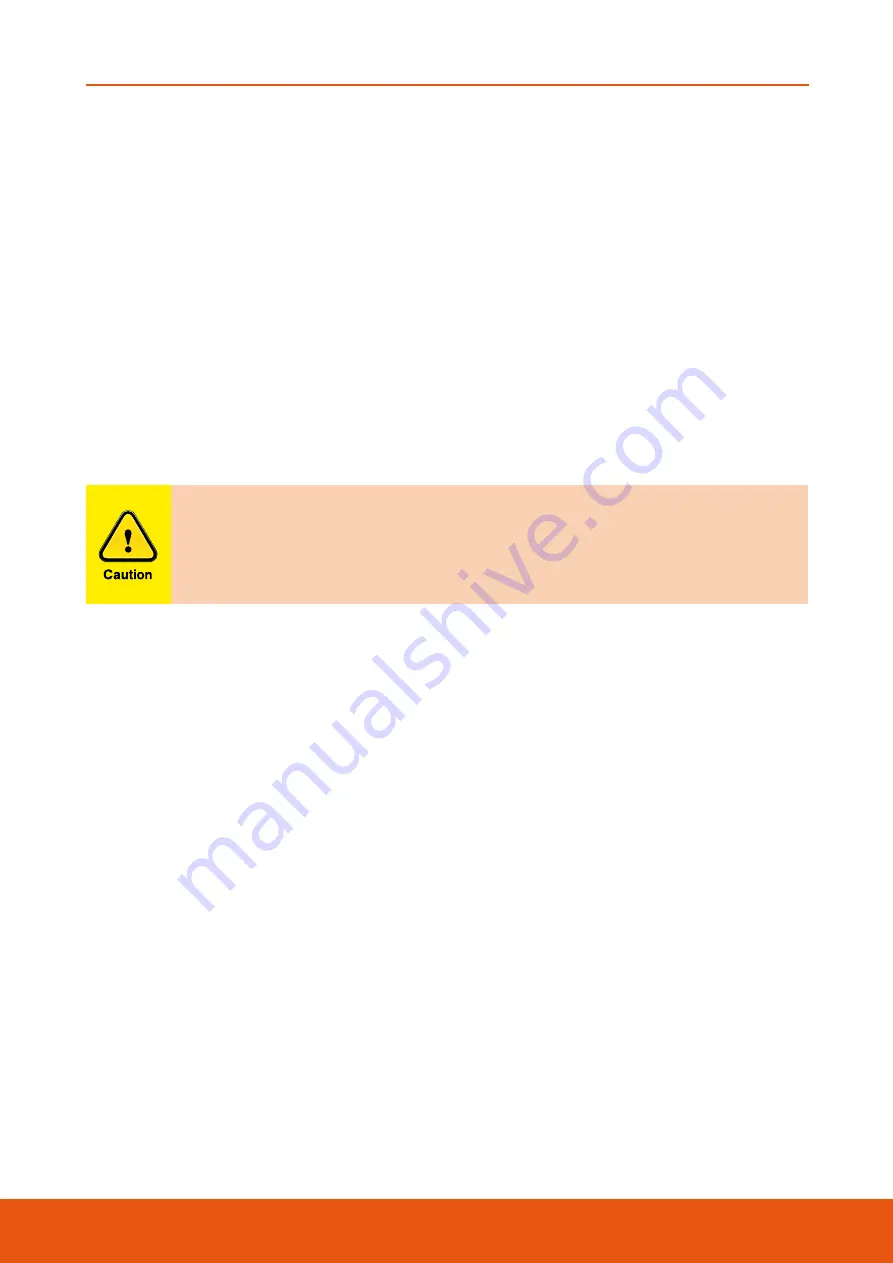
CHECK VALVES - SWING, TILTING DISC & PISTON - API594/API6D/BS1868/B16.34
Australian Pipeline Valve - Installation, Operation and Maintenance Manual
6
1.2 PREPARATION FOR INSTALLATION
• Remove protective end caps or plugs and inspect valve ends for damage to threads, socket weld bores
or flange faces.
• Thoroughly clean adjacent piping system to remove any foreign material that could cause damage to
seating surfaces during valve operation.
• Verify that the space available for installation is adequate to allow the valve to be installed.
1.3 END CONNECTIONS
1.3.1 Flanged Ends
Check to see that mating flanges are dimensionally compatible with the flanges on the valve body and
ensure sealing surfaces are free of debris.
Install the correct studs and nuts for the application and place the gasket between the flange facings.
Stud nuts should be tightened in an opposing criss-cross pattern in equal increments
to ensure even gasket compression. See Appendix A, Table A.
1.3.2 Buttweld Ends
Clean the weld ends as necessary and weld into the line using an approved weld procedure. Make sure
the pipe and valve body material given on the nameplate or valve body is compatible with the welding
procedure. (Refer compatibility cross reference chart at the APV website for equivalent pipe, valve &
fitting grades).
1.3.3 Valve Installation by Welding
Leave valves assembled during installation, welding and post-weld heat treatment. This will prevent the
valve seat from floating or distorting during the process. After welding completion, open the valve and
flush line to clean out any foreign matter.
Remove the bonnet and bonnet gasket and match mark each component during disassembly for proper
reassembly.
Theresponsibilityforweldingofthevalvesintopipingsystemsisthatofthoseperformingthewelding.
RefertoASMEB31.1,B31.3etc.Writtenweldingprocedurescoveringallattributesoftheprocessand
materialstobeweldedshallbeinaccordancewithSectionIXoftheASMEBoilerandPressureVesselCode
andanyadditionalrequirementsfromtheapplicablepipingcodeincludinganypossiblenecessary
localisedpostweldheattreatmentdependingonmaterialspecifications.