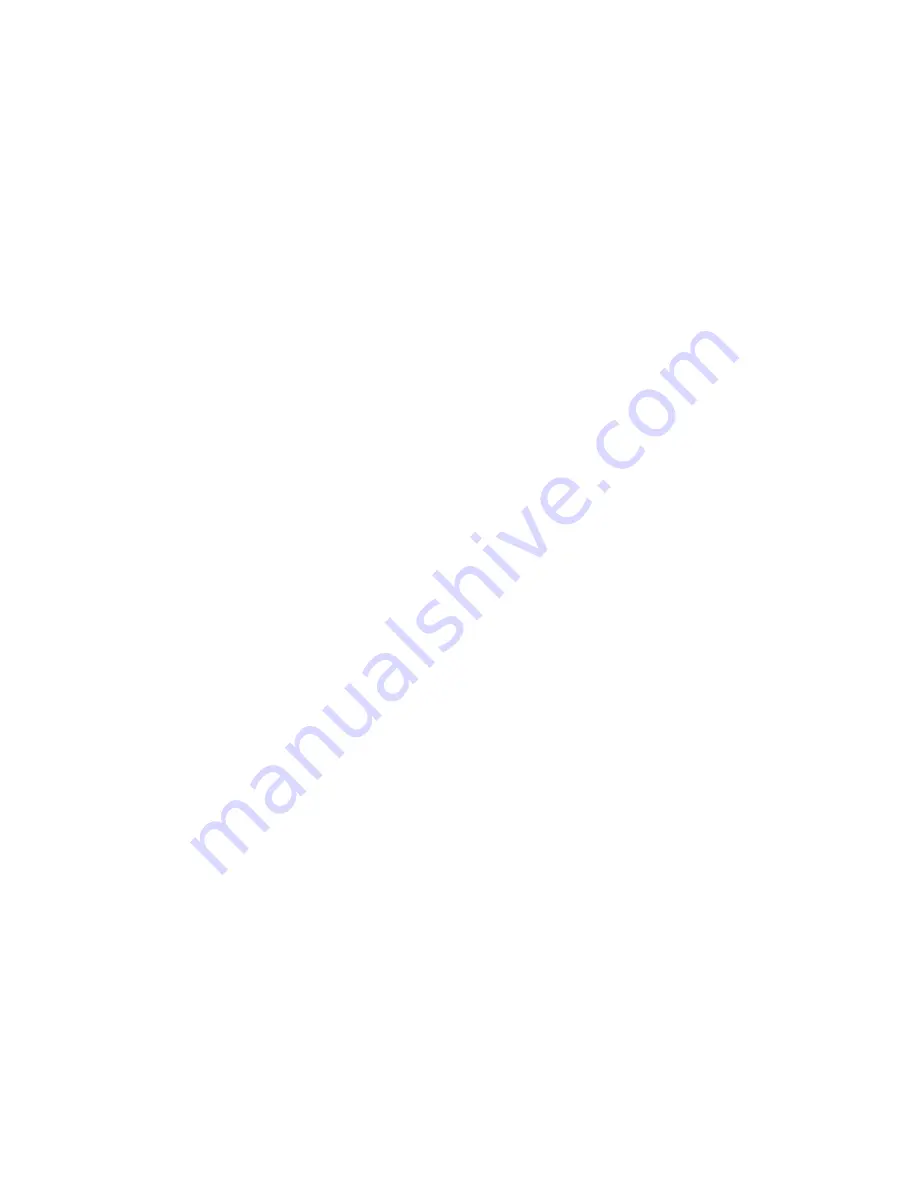
3
1.0 INTRODUCTION
The following Owner's Manual for the Applied Air equipment outlines installation,
operation and service requirements for IFD series of indirect gas fired duct furnace.
The IFD series is ETL certified. Certification includes indoor models, high altitude
applications, and a wide range of operational conditions. For more information on
certification, please contact the Customer Service department at Applied Air Systems.
These manuals have been prepared to assist in the installation, operation and
maintenance of your duct furnace. It is good practice to know as much as possible
about your duct furnace before trying to install or operate it. Read the contents carefully
before proceeding. Due to the custom nature of Applied Air equipment, not all
possibilities are addressed in this manual. In cases where a special application is not
covered, the customer or installer can obtain information from Applied Air's sales
representative or the Applied Air factory. Additional component specific manuals may
be included with this manual, i.e. burner manuals, to assist in the maintenance or
repairs of the furnace.
1.1 Notes
1. Please disregard any information and/or data covering optional components not
supplied with the duct furnace.
2. Do not destroy or remove information from this instruction manual. Leave this
instruction in the electrical enclosure of the duct furnace.
3. Field installed fuel conversion kits are not available. If your fuel requirements change
contact the factory about converting your furnace to/from natural or LP gas.
1.2 Caution
1. Regulations require that service mechanics that work on combustion equipment must
be qualified.
2. Contact with moving parts can cause injury or property damage. Automatic control
devices may start the duct furnace without warning. To prevent accidental start-up, the
maintenance personnel should always lockout all power supplies before working on
Applied Air equipment. A duct furnace will often have more than one power connection
point; disconnect all sources of power before servicing. Even when locked out
electrically, fans located in a parallel or series fan system may be subject to wind
milling.
3. Refer to the rating plate for fuel input and supply pressures.
4. DO NOT attempt to start the burner if the duct furnace is full of vapor or gas, or if
the combustion chamber is very hot.
5. DO NOT use gasoline, crankcase oil or any oil containing gasoline for fuel.
6. DO NOT burn garbage or paper in this heating system. Never leave paper or
combustible material near the duct furnace.
7. SHUT OFF the manual fuel supply valve if the burner is shut down for an extended
period of time.
8. Ensure all access and clean-out doors are secure before starting the blower and burner.