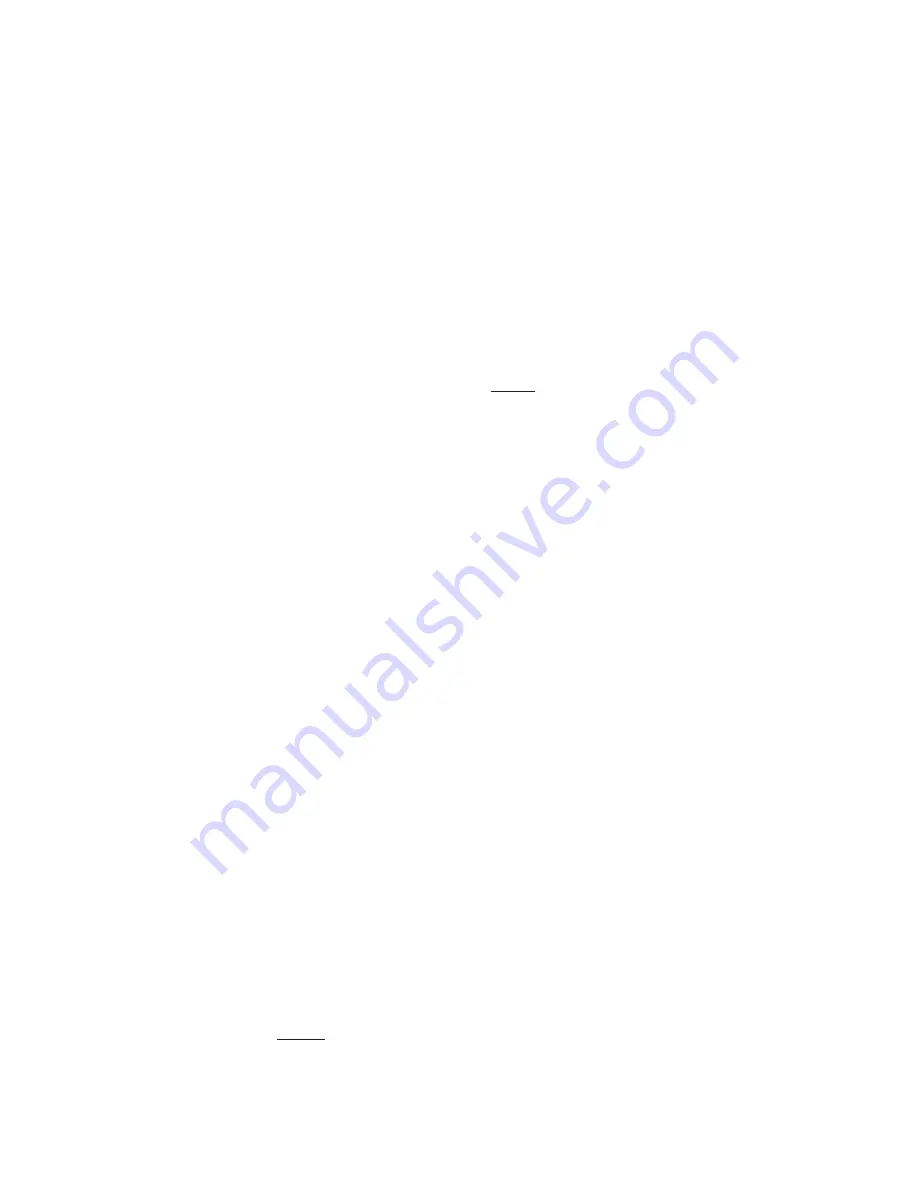
– 22 –
NOTE: Pilot regulator adjustment may be needed if
the adjustment of the needle valve does not yield
the required reading. Typical adjustment of the
needle valve is 1-1/2 to 2 turns open.
NOTE: Frequently the cause of pilot problems
relates to gas pressures that are too high and/or air
dampers that are closed too far. This causes a fuel
rich mixture.
NOTE: 3 or 4 trials may be needed to purge air from
pilot line.
Watch D.C. voltmeter carefully. The reading should
be steady and between 2.0 and 5.0 Volts D.C. If the
reading is too low, slowly turn the needle valve in or out
until satisfactory fl ame signal is obtained (See separate
literature for testing of fl ame safeguard).
Make sure that the combustion air and pilot gas
pressure is suffi cient to provide instant ignition, a stable
fl ame, and fl ame signal. Cycle pilot several times to
insure reliability.
With pilot adjusted, you can now shut down the burner
by turning the Heat "on-off" switch to the "off" position.
Setting the Main Flame
IMPORTANT: When the Flame Safeguard relay
module is switched to the TEST mode, it stops
and holds at the next Run/Test Switch point in the
operating sequence. Make sure that the Run/Test
Switch is in the Run position before starting the
burner.
CAUTION: Do not attempt to start the burner when
furnace is full of vapor or combustion chamber is
very hot.
CAUTION: At no time should you stand in front of
the relief door.
Connect the test instruments, meters, and thermometers
on the heater and controls to measure and record the
appropriate data.
Install one manometer at test port on the last tee of the
burner manifold and one at the relief door.
Set all thermostats to call for heat. Set inlet ductstat (if
applicable) above outside air temperature.
Restart unit. After the pilot proves the main automatic
fuel valves will be energized.
Slowly
open the last gas
shut-off valve and the burner should light immediately.
CAUTION: If main fl ame does not light within a few
seconds after pilot fl ame is established, shut the
burner down and repeat steps. You may have to
eliminate air from the main gas line. The main gas
pressure and / or burner air setting may also need
to be readjusted.
If fl ame signal drops signifi cantly when main gas valves
open, slightly increase or decrease pilot gas pressure to
attain a steady fl ame signal.
After the burner lights; adjust gas pressure regulator,
using a manometer, and combustion air damper
to match normal manifold pressure shown on unit
nameplate. Make sure the thermostat and gas valves
are in high fi re.
These units have an induced draft fan, a minimum
of –0.20" W.C. must be maintained at the relief door,
simultaneously while setting the fuel to air pressure
on the burner at full input. This is done by changing
the damper setting at the induced draft fan outlet
with a warm stack. Be sure to lock down the locking
quadrant when you are done.
Check all gas piping again for leaks using a soap bubble
solution.
On-Off Operation
Check to make sure operating thermostat cycles burner
and induced draft fan.
See fi nal checks and adjustments.
High-Low-Off Operation
Turn the two stage thermostat down slowly until main
gas valve begins to drive closed (low fi re) or the power
on the second stage may be disconnected.
NOTE: Low fi re rate should be set at approximately
50% of high fi re.
CAUTION: Too low of an input setting will cause
condensation of the fl ue gases.
To reset low fi re, remove the cover from the Two Stage
gas valve actuator and using the wrench provided
readjust the internal cam setting.
Check to make sure Two Stage thermostat cycles
burner and induced draft fan.
See fi nal checks and adjustments.
Summary of Contents for GAS-FIRED HEATERS
Page 6: ... 6 ...
Page 7: ... 7 ...
Page 8: ... 8 ...
Page 9: ... 9 ...
Page 13: ... 13 ...
Page 24: ... 24 TYPICAL SEQUENCE FOR MODULATING THERMOSTAT WITH 135 OHM CONTROLS ...
Page 25: ... 25 TYPICAL SEQUENCE FOR MODULATING THERMOSTAT WITH 4 20 mA CONTROLS ...
Page 64: ...4830 Transport Drive Dallas TX 75247 Phone 214 638 6010 Fax 214 905 0806 www appliedair com ...