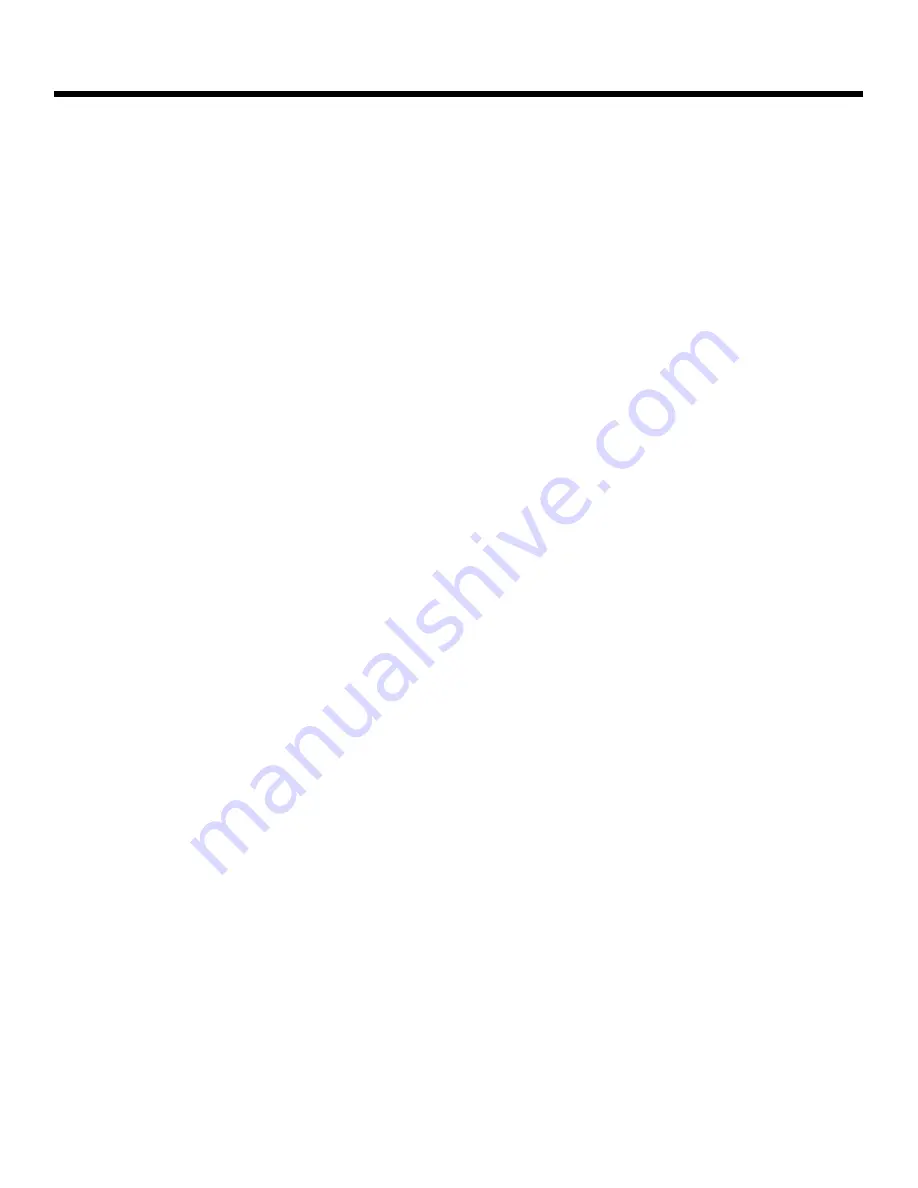
13
G5TWIN OPERATION MANUAL
© 2016 APPION INC. - ALL RIGHTS RESERVED
Additional Machine Usage
PURGING NON-CONDENSABLES FROM RECOVERY CYLINDERS
In the event that the Recovery Cylinder pressure is higher than expected, or if the recovery process seems slower
than usual, use an external gauge (not the gauge on the G5Twin) and a Refrigerant Pressure/Temperature
chart to check for the presence of non-condensable gases in the cylinder.
You can bleed/purge non-condensables into another cylinder following this procedure:
1. The Recovery Cylinder must remain undisturbed for at least 24 hours for the non-condensables to rise to
the top of the cylinder.
2. Through a Manifold Gauge Set, connect the Recovery Cylinder Vapor Port to the Vapor Port of a second
recovery cylinder.
3. Consult a Refrigerant Pressure/Temperature chart, and check the temperature of the Recovery Cylinder to
determine what the pressure should be.
4. While the pressure is higher than the pressure on the chart, slowly open the Vapor Port to bleed off excess
pressure until it is about 5 psi (0.35 Kg/cm
2
) above the pressure listed on the chart.
5. Close the valves and let the cylinder stand still for 10 minutes. Repeat if necessary.
CHANGING BETWEEN REFRIGERANT TYPES
Appion refrigerant recovery machines are unique in that there is no refrigerant directly introduced into the
compressor crankcase. This allows the G5Twin to easily and efficiently clear out refrigerant at the end of the
recovery process. However,
as with all recovery machines
, trace refrigerant vapors may remain and should be
cleared out when switching between different types of refrigerant.
When you are changing between refrigerant types, any refrigerant remaining in the recovery machine
should be drawn into a deeply evacuated recovery cylinder before switching. Then, to prevent any cross-
contamination, it is recommended that a vacuum pump be connected to the output port of the G5Twin
(keep
the Input Valve closed and the Output Valve open),
and run the vacuum pump to completely evacuate the
machine of any trace refrigerant vapors.
STORING THE MACHINE BETWEEN USES
When storing the machine between recovery jobs, trace refrigerant vapors can continue to wear on the
internal components of the machine. If the machine is fully sealed (closed valves or port covers), storing the
machine in a hot truck can cause the trace vapors to expand and wear on the components further.
To minimize wear during storage, leave both valves on the G5Twin open.
You can use port caps/covers to
protect the machine from dirt, but make sure they do not have an airtight seal.