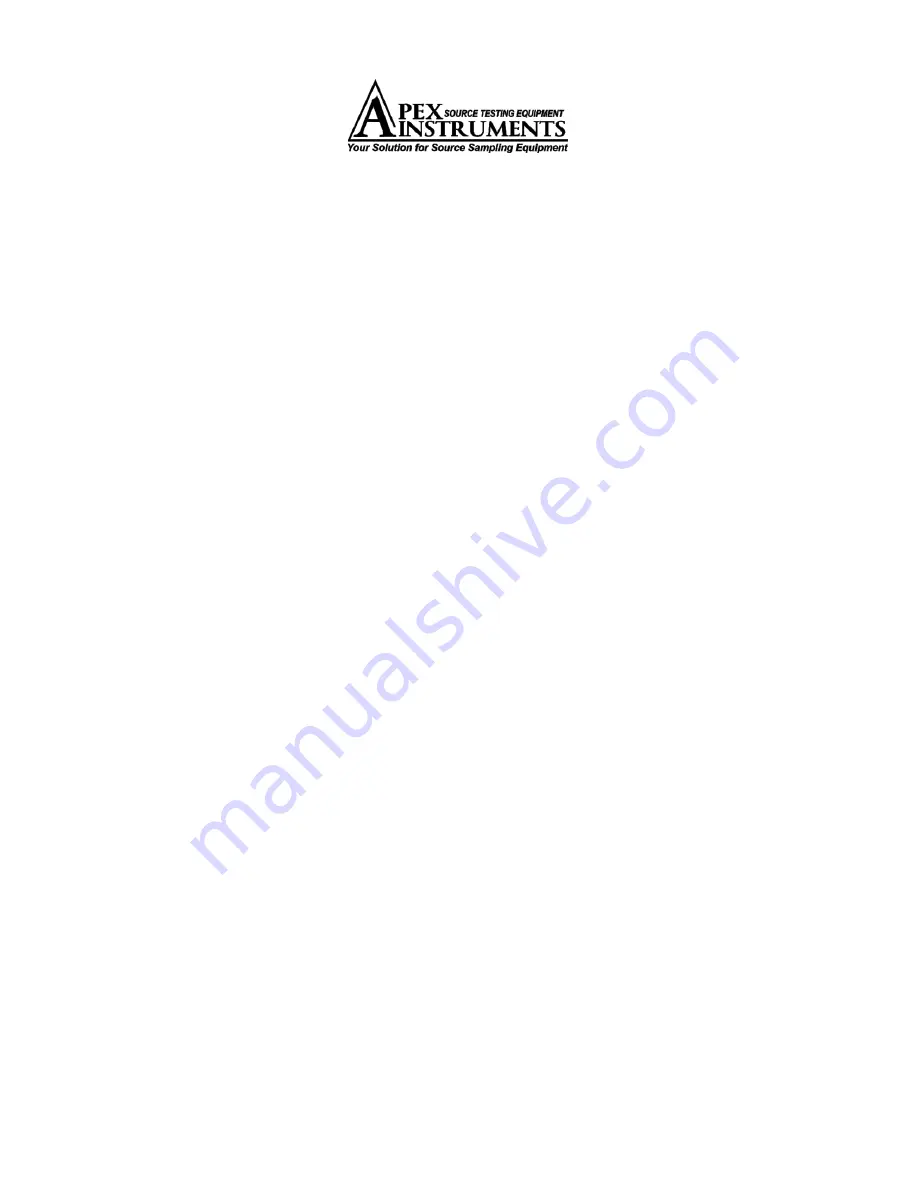
Copyright © 2017 Apex Instruments, Inc. All Rights Reserved
This manual may not be, in part or in whole, reproduced, transmitted, transcribed, stored in a retrieval
system, or translated into any other language or computer language, in any form or by any means,
whether it be electronic, magnetic, manual, mechanical, optical or otherwise, without the prior written
consent of Apex Instruments, Inc. 204 Technology Park Lane, Fuquay-Varina, NC 27526.
Warranty
This equipment is sold subject to the mutual agreement that it is warranted by Apex Instruments, Inc.
free from defects of material and of construction, and that Apex Instruments, Inc. liability shall be
limited to replacing or repairing at our facility (without charge, except for transportation), or at
customer plant at our option, any material or construction in which defects become apparent within
one year from the date of shipment, except in cases where quotations or acknowledgments provide
for a shorter period. Components manufactured by others bear the warranty of their manufacturer.
This warranty does not cover defects caused by wear, accident, misuse, neglect or repairs other than
those performed by Apex Instruments, Inc. at our service center. We assume no liability for direct or
indirect damages of any kind and the purchaser by the acceptance of the equipment will assume all
liability for any damage which may result from its use or misuse.
We reserve the right to employ any suitable material in the manufacture of our apparatus, and to
make any alterations in the dimensions, shape or weight of any parts, in so far as such alterations do
not adversely affect our warranty.
Important Notice
This instrument provides measurement readings to its user, and serves as a tool by which valuable
data can be gathered. The information provided by the instrument may assist the user in eliminating
potential hazards caused by the utilized process; however, it is essential that all personnel involved in
the use of the instrument or its interface, with the process being measured, be properly trained in the
process itself, as well as all instrumentation related to it.
The safety of personnel is ultimately the responsibility of those who control process conditions. While
this instrument may be able to provide early warning of imminent danger, it has no control over
process conditions, and it can be misused. In particular, any alarm or control systems installed must
be tested and understood, both as to how they operate and as to how they can be defeated. Any
safeguards required such as locks, labels, or redundancy, must be provided by the user or specifically
requested of Apex Instruments, Inc. at the time the order is placed.
Therefore, the purchaser must be aware of the hazardous process conditions. The purchaser is
responsible for the training of personnel, for providing hazard warning methods and instrumentation
per the appropriate standards, and for ensuring that hazard warning devices and instrumentation are
maintained and operated properly.
Apex Instruments, Inc. cannot accept responsibility for conditions beyond its knowledge and control.
No statement expressed or implied by this document or any information disseminated by the
manufacturer or its agents, is to be construed as a warranty of adequate safety control under the
user‘s process conditions.
XC-51 SAMPLING CONSOLE
Revision:01 Page 1 of 23 9/26/2017