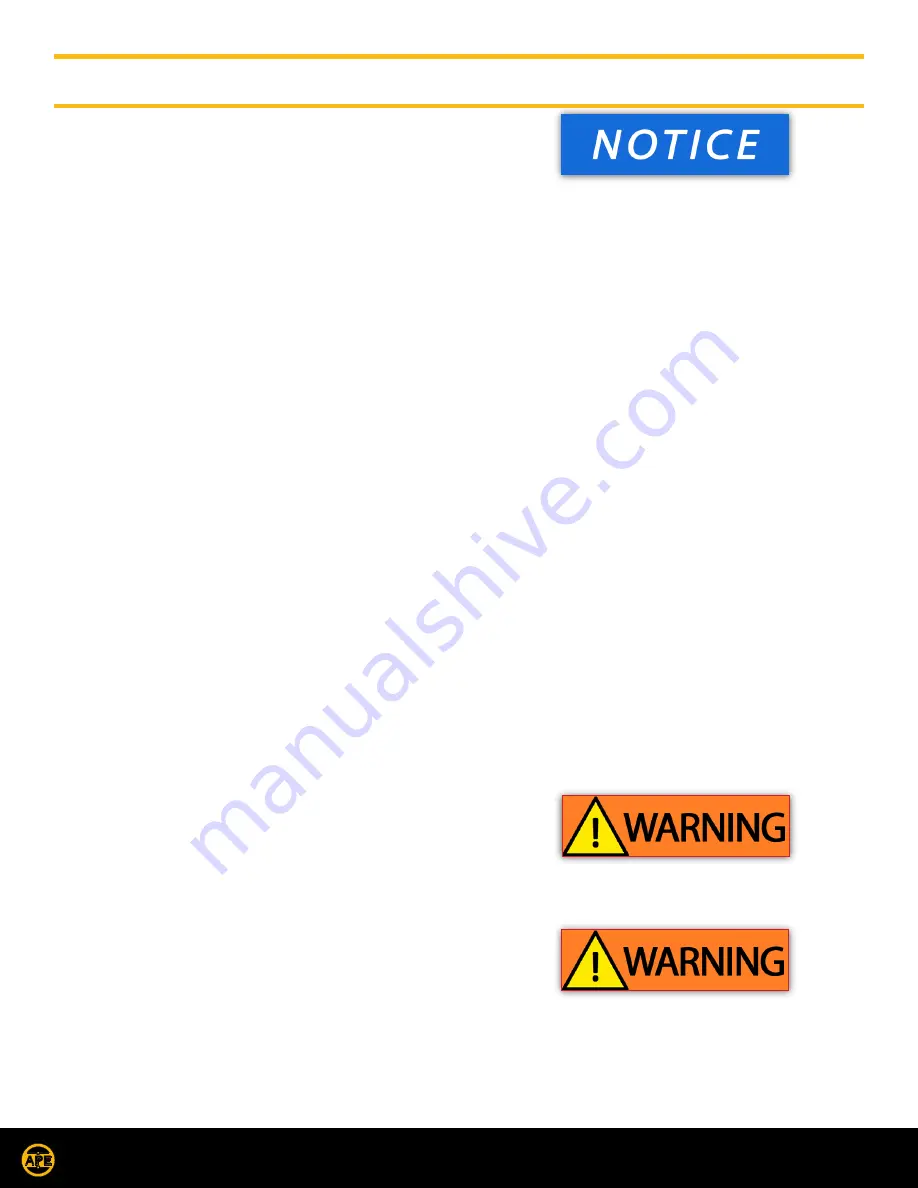
Page 4
AM
ER
IC
AN
P
ILE
DRIVING E
QU
IP
M
EN
T
J&
M
F
O
UN
DAT
ION EQ
UIP
M
EN
T
AM
ER
IC
AN
P
ILE
DRIVING E
QU
IP
M
EN
T
J&
M
F
O
UN
DAT
ION EQ
UIP
M
EN
T
800-248-8498
800-248-8498
WWW.AMERICANPILEDRIVING.COM
WWW.AMERICANPILEDRIVING.COM
MODEL 300-4 VIBRO
Copyright © 2020 American Piledriving Equipment Inc. All Rights Reserved
13.
Remove all tools, parts and electrical cords
before starting the unit.
14.
Do
NOT
smoke or use an open flame while
servicing batteries. Batteries generate explosive
gas during charging. Keep the area ventilated.
15. When filling the fuel tank do
NOT
smoke or use
an open flame in the vicinity.
16.
If abnormal equipment operation is observed,
stop use immediately and correct the problem.
17. Store oily rags in approved containers and
away from the engine exhaust system.
18.
Do
NOT
adjust the hydraulic pressures higher
or lower than those specified in this manual.
19.
Do
NOT
operate this equipment with hydraulic
hoses that are damaged or ‘kinked’. Replace
damaged hoses immediately.
20.
Do
NOT
support hydraulic hoses with wire rope.
21.
Do
NOT
allow hydraulic hoses to snag during
movement of the unit.
22.
Do
NOT
pull on and/or attempt to move
equipment with the hydraulic hoses.
23.
Do
NOT
attempt to locate hydraulic leaks with
your hands. High-pressure leaks can penetrate
skin and cause severe damage, blood
poisoning, and/or infection.
24.
Do
NOT
attempt to repair leaks while the
equipment is in operation.
25.
Do
NOT
attempt to tighten and/or loosen fittings
and/or hoses when the machine is in operation.
26. When moving and/or transporting this
equipment, insure that the vehicle or vessel is
of sufficient capacity to handle the load. Make
sure that the equipment is properly tied down.
27. When moving this equipment be sure that the
QD Dust Caps are tight and that the cap safety
cables are in place. Be sure that all equipment
parts are tight and properly secured before
shipment. Unsecured parts may vibrate loose
and fall causing injury and/or property damage.
28. Rounded and/or damaged bolt heads and nuts
should be replaced. Proper torque values are
necessary to prevent parts on this equipment,
leads, and crane booms from loosening and
falling. Refer to the torque chart in this manual.
29. Keep limbs and tools clear of the clamp jaws.
30.
Do
NOT
allow clothing, hoses, ropes, etc., to
become entangled in moving components,
including the clamp and suppressor.
31.
Keep excavator, piles, vibrator, wire rope, and
other equipment at least 15 feet (5 meters) from
electrical power lines, transformers, and other
electrical equipment, or at such distance as
required by applicable safety codes.
32. Never disconnect the excavator and vibrator
while the vibrator is on pile. Loss of hydraulic
pressure will cause vibrator to fall. Lay vibrator
down when not in use.
33. When extracting piles always attach a safety
line between the pile and the excavator.
34. When extracting piles, check excavator load/
radius tables to be sure capacity is adequate for
maximum allowable extraction pull.
35. When extracting or driving piles always be sure
that the excavator bucket pivot pin is aligned
with the centerline of the pile. Do not side load
the vibrator. Vibrator damage will result.
36. When extracting piles, do not exceed the
capacity of the vibrator suppressor.
37.
Check vibrator suppressor for broken or
damaged elastomers daily. Do not operator
vibrator with damaged elastomers.
38. Always start both driving and extraction of piles
in an unloaded condition.
39.
Do
NOT
run the vibrator without clamp jaws
closed.
40. Guide the vibrator with a tag line when possible.
(These precautions must be followed at all times to ensure personal and equipment safety.)
A properly maintained fire extinguisher,
suitable for oil fires, MUST be kept in
the immediate vicinity of operations.
Keep hands, feet, and/or tools well
clear of all clamp jaws and suppressor
elastomers.
Do not attempt to lift or walk with
piles exceeding 10 tons weight.