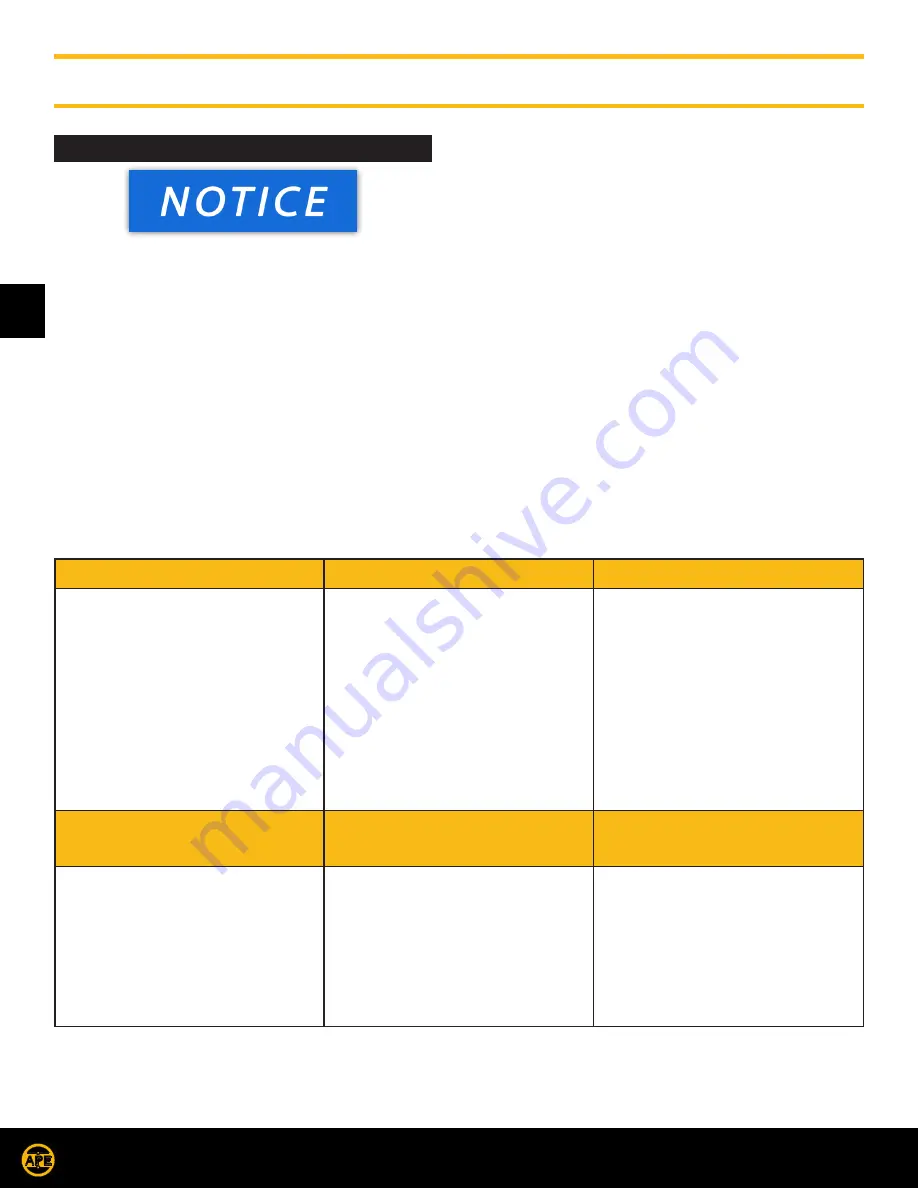
Page 16
AM
ER
IC
AN
P
ILE
DRIVING E
QU
IP
M
EN
T
J&
M
F
O
UN
DAT
ION EQ
UIP
M
EN
T
800-248-8498
800-248-8498
WWW.AMERICANPILEDRIVING.COM
WWW.AMERICANPILEDRIVING.COM
MODEL 300-4 VIBRO
Copyright © 2020 American Piledriving Equipment Inc. All Rights Reserved
AM
ER
IC
AN
P
ILE
DRIVING E
QU
IP
M
EN
T
J&
M
F
O
UN
DAT
ION EQ
UIP
M
EN
T
MAINTENANCE & TROUBLESHOOTING
MAINTENANCE & TROUBLESHOOTING
Maintenance Chart
In addition to keeping the unit in ideal
condition, regular maintenance will help
prevent unexpected machine downtime
by finding minor issues before they can
develop into serious or dangerous problems.
Lubrication, inspection, and replacement of key
parts are the major steps of this maintenance.
Lubrication is especially important and different
components have their own schedules and
lubrication types. Pay special attention to the
lubrication steps noted in the chart above.
At each scheduled interval perform all previous
checks which are due.
During all steps be sure to:
•
Thoroughly clean all lubrication fittings,
caps, filler and level plugs along with their
surrounding surfaces before servicing.
• Prevent dirt and other contaminants from
entering with lubricants.
These service intervals are for normal
operating conditions. Reduce the time by half
when:
•
The average temperature is above 80°F
(26°C) or below -10°F (-23°C).
•
Operating in a dusty or sandy area.
•
Operating for more than 12 hours per day.
Environments that are humid and/or salty do
not change the service intervals. However,
during all procedures check the components
for corrosion.
DAILY
WEEKLY
70 HOURS
•
Check operators report.
•
Check oil level in the gearbox
and bring to correct level.
• Inspect bolts, nuts, and screws
for tightness.
•
Inspect elastomers for cracks.
•
Inspect fittings, hoses, and
manifolds for leaks.
• Inspect hydraulic hoses and
fittings for fraying and leaks.
Replace any hoses with broken
threads.
• Bleed air from the hydraulic
lines as described in the
previous chapter.
•
Inspect gearbox magnetic drain
plug for metal flakes. If flakes
are found see Troubleshooting
chart.
•
Change gearbox oil.
•
Clean gearbox breather and
pop-off valves.
• Cycle oil into the hydraulic
clamps as described later in
this chapter.
250 HOURS
OR 6 MONTHS
1500 HOURS
OR 1 YEAR
6000 HOURS
OR 3 YEARS
•
Inspect eccentric bearings.
•
Check torque on gearbox,
suppressor, and clamp
attachment mounting bolts.
• Inspect hydraulic motors
for leaks, wear, and proper
operation.
•
Replace eccentric bearings.
• Replace eccentrics,
elastomers, and hydraulic
motors.