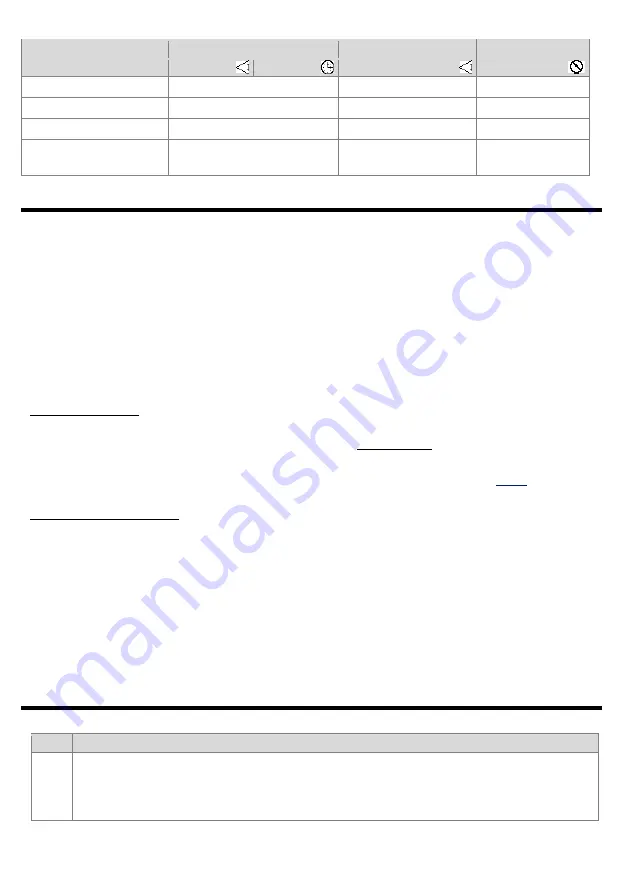
21
The basic configuration parameters for individual stages are summarized in the table below:
Stage parameters
Stage 1
Stage 2
Stage 3
segment 1
segment 2
segment 3
segment 4
Type of stage
48:
tYp1
=
Grti
(2 segments)
53:
tYp2
=
Grti
58:
tYp3
=
StoP
Stage
SP
set point
SP
C
=
Set1
(e.g. 700°C)
SP
K
=
Set2
(e.g. 60°C)
not relevant
Slope (°C/min)
N1
=
GrA1
(e.g. 25°C/min)
N3
=
GrA2
(e.g. -10°C/min)
not relevant
Stage/segment time
T2
=
tiM1
(e.g. 90min)
tiM2
= 0 (segment 2 is
missing)
not relevant
9.7. MIXING VALVE CONTROL. SAMPLE CONFIGURATION.
The device allows you to control a servo valve with two open-close contact inputs, without a feedback signal.
Standard characteristics (heating/cooling) and operating modes (ON-OFF, PID) are binding for valves controlled
by the analog signal mA/V and do not require any additional comments. The servo-type algorithm is implemented
on outputs 1 (open) and 2 (close) as a three-point step control. It requires setting parameter 16:
ctY2
to value
vALc
(which also prevents simultaneous activation of both outputs) and other configuration parameters
(described in the example below and in
chapter 8
). The total time of opening/closing the valve is defined by
parameters 14/21:
PEr1
/
2
.
The valve control is started at the start of control (automatically after switching on the power or manually with the
[F]
,
[SET]
function keys or the
BIN
binary input programmed as output operation start/stop,
chapter 7.1
) and
begins with the valve positioning (complete closing) procedure (with the message
vALc
). This procedure also
takes place after each change of the pulse period for output 2 (parameter 21:
Per2
).
Sample
configuration
(ON-OFF
for
heating
with a set temperature of
50°C and a valve opening/closing time of
100s):
- output 1 parameters (
Table 8, point II
, group
out1
):
ctY1
=
onoF
(recommended),
Fun1
=
in
dH
,
H1
=0°C
,
SET1
=
50°C,
oPF1
=
1%,
PEr1
=
100s,
- output 2 parameters (group
out2
):
ctY2
=
vALc
,
Fun2
=
dEoF
(deviation from
SEt1
,
Table 8, Fig.8.7
),
H2
=
0°C,
SEt2
=
0.5°C
(deviation value),
oPF2
=
100%,
PEr2
=
100s,
Fto2
=
on
(emergency status is on)
Tips
for
adjusting the settings
(
change
only
one
of the
factors
and
observe
the effect on the process):
a) increasing the rate of changes - increase the parameter
oPF1
(recommended 1÷5%) and decrease
PEr1
,
b) reducing overshoots and oscillations - reduce
oPF1
(recommended 1
÷
5%), increase
PEr1
, set
a small dead zone (
SEt2
, e.g. 0.5
°
C), recommended
H1
/
2
= 0°C
Alternatively, for the output 1, the PID control (
chapter 9.3
) can also be used with a larger value of
oPF1
(suggested
10÷20%) , which will result in reaching the setpoint faster, but at the same time, with incorrectly selected PID
parameters, the control may be less accurate (due to overshoots and oscillations). In the range of Pb, the length of
the opening pulse (step) will be variable (depending on the measured value PV, according to the principle of PID
operation). If the PID algorithm is used, the P variant control is recommended (proportional, e.g. Pb=5°C,
Ti=Td=0s) or PD (proportional-differential, e.g. Pb=5°C, Ti=0, Td=30s).
10. SIGNALING MESSAGES AND ERRORS
a)
measurement errors:
Code
Possible causes of the error
^^^^
____
----
- exceeding the measurement range of the sensor/signal above (
^^^^
) or below (
____
)
- incorrectly connected or different sensor/signal than set in the configuration (
chapter 8
,
parameter 0:
inP
)
- missing sensor/measuring signal or input damage (
----
with a critical message
EinP
)