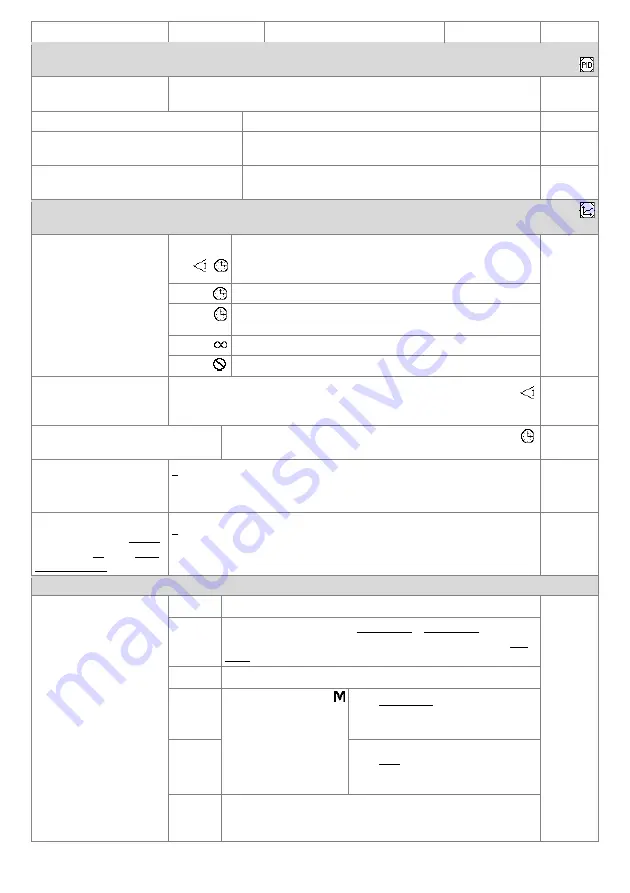
15
35:
ctoP
upper correction
-4.00
÷
0.50
mA/V
changes
of0.05
mA/V
for 20mA or 10V
IV. PID ALGORITHM CONFIGURATION
(1÷3), submenu
Pid1
÷
Pid3
, in the 3 groups
Pid1
/
2
/
3
there are the same
parameter sets with different indices and numbering in the names, description in
chapters 9.3÷9.5
36/40/44:
tun1
/
2
/
3
type of
PID tuning (autotuning)
0:
oFF
=disabled, 1:
Auto
=smart logic, 2:
S tEP
= step response method
(fast), 3:
oSct
= oscillation method (longer),
chapter 9.4
oFF
37/41/45:
Pb1
/
2
/
3
Pb
proportional band
0.1
÷
1800
or
1
÷
9999
units
(2)
1.0
°C
38/42/46:
ti1
/
2
/
3
integral time
Ti
0÷
3600
s, PID algorithm integral action time,
0
turns off the
integral element
0
sec.
39/43/47:
td1
/
2
/
3
derivative time
Td
0
÷
999
s, PID derivative action time,
0
turns off the derivative
element
0
sec.
V. CONFIGURATION OF THE PROCESS CONTROLLER
(programmable operating characteristic, ramping), submenu
ProG
, description -
chapter 9.6
48/53/58:
tYP1
/
2
/
3
stage
type 1/2/3
0:
Grti
stage consisting of 2 segments: reaching the setpoint
11:
SEt1
/
2
/
3
with the
slope
defined
by
parameter
49:
GrA1
/
2
/
3
(ramping) and countdown (50:
tiM1
/
2
/
3
) after reaching it
Grti
1:
tiME
countdown of time after reaching the setpoint
SEt1
/
2
/
3
(
±
H
/2)
2:
toti
countdown of time for the entire stage (regardless of the
setpoint)
3:
EndL
continuous - no time limit
4:
StoP
end - the last stage of the program, available only for stage 2/3
49/54/59:
GrA1
/
2
/
3
slope
of the segment of the
stage 1/2/3
pace of changes (gradient) for the 1st segment of the type stage
Grti
,
ramping,
-30.0
÷
30.0
°
C/min or -
300
÷
300
units/min
(2)
1.0
°C/min
50/55/60:
tiM1
/
2
/
3
time
for
stage
1/2/3
0
÷
1440
min,
duration of the
segment for the stage with
countdown
60
min
51/56/61:
PSE1
/
2
/
3
control
algorithm for step 1/2/3
1:
onof
=ON-OFF with hysteresis, 2/3/4:
Pid1
/
2
/
3
=PID with parameter set
1/2/3 (
chap. 9.3
, not
recommended
for the
stage
Grti
-
gradient
may
disturb
PID operation
)
onof
52/57/62:
ASt1
/
2
/
3
state of
the auxiliary output
during
stage 1/2/3, 63:
AStE
after
the completion of stage 3
1:
oFF
= disabled, 2:
on
= enabled, 3:
hAnd
= manual mode with a set output
signal level (parameter 67:
HSEt
), selection of the auxiliary output (1/2/3) is
defined by the parameter 9/16/23:
ctY1
/
2
/
3
=
PrGA
oFF
VI. KEYS, ACCESS OPTIONS AND OTHER CONFIGURATION PARAMETERS
, submenu
othE
64:
FunF
function
of
[F]
key
65:
Funb
function of the
binary input
BIN
66:
FunS
additional
function of the
[SET]
key
1.
detailed description in
chapter 7.1
)
2.
values 3÷8 ( quick
manual mode) interrupts
and resets the tuning and
0:
nonE
inactive - device status (description,
chapter 7, point a
)
nonE
1:
Set3
step change of the
setpoint
with the set of
parameters for
outputs
1
and 3
(day = 11:
Set1
/night = 25:
Set3
)
,
both outputs
work
the
same
(copy)
2:
bLoc
keyboard lock
,
messages
bLoF
(stop)/
bLon
(start,
default)
3:
hd1A
5:
hd2A
7:
hd3A
unconditional manual
mode
for
the output
1/2/3
with
the output
signal level (MV) set by
parameter 67:
HSEt
,
messages
hnd1
/
2
/
3
(start)/
hoF1
/
2
/
3
(stop)
start (unchanged) with an initial value
for 67:
HSEt
taken from the current
automatic control mode
4:
hd1w
6:
hd2w
8:
hd3w
start (step) with the preset value of
parameter 67:
HSEt
9:
cLEA
(also
10/11)
deleting errors and alarm memory (LATCH) of the
STB
safety
controller with the message
cLEA
or
none
(when there are no
errors and alarms)