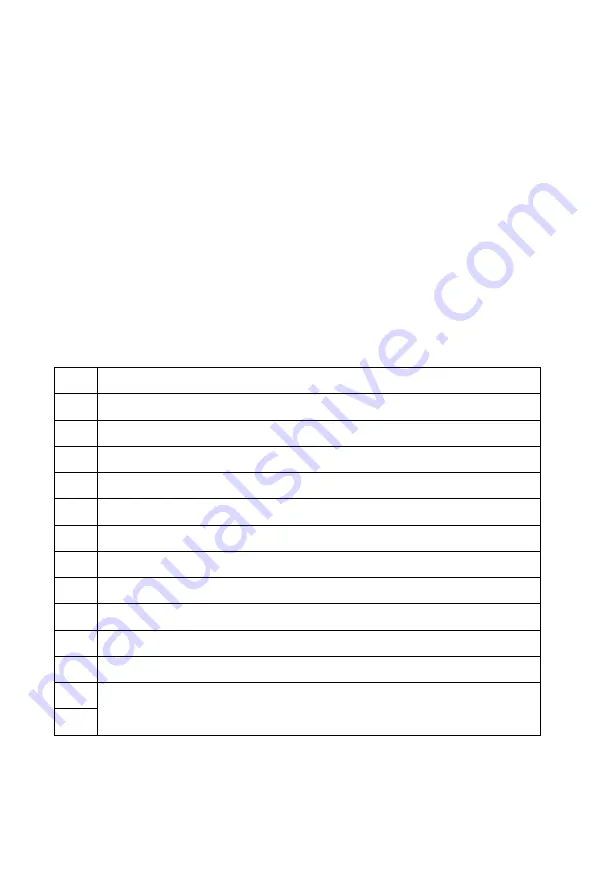
21
1.Output terminal (+)
Connect electrode holder when in SMAW mode; Connect with the work piece when in
TIG mode.
2.Control socket
Connect to torch trigger.
3.Output terminal (-)
Connect work piece when processing SMAW; connect with TIG torch when processing
TIG welding.
4.Water inlet
Connect water hose of TIG torch.(optional).
5.Gas outlet
Connect gas hose of TIG torch.
6.Analog control socket(optional,only ATIG***P-C welding machine has this socket)
Connect to analog remote controller or other special device.
Table 4-6-1 Description of analog control socket
7.Digital remote control socket(optional,only ATIG***P-C welding machine has this
socket) Connect to digital remote controller or other 485 communication device.
Pin No.
Description
1
Chassis Ground
,
connect with shield layer of control cable.
2
Null
3
Power supply of remote control current given potentiometer:10VDC
4
Remote control current input signal (0-10VDC).
5
Remote control current GND.
6
Welding machine start signal, short circuit with pin 8 ,welding machine start
7
Gas test signal, short circuit with pin 8,the gas valve on.
8
GND.
9
Arc voltage output,0-10VDC(10V equals to 100V arc voltage).
10
Welding current output signal,0-10VDC(10V equals to Max. rated output current).
11
GND
12
Successful arc start signal: Standby: pin 12 and pin 13 open, successful arc start:
pin12and pin13 short circuit
13