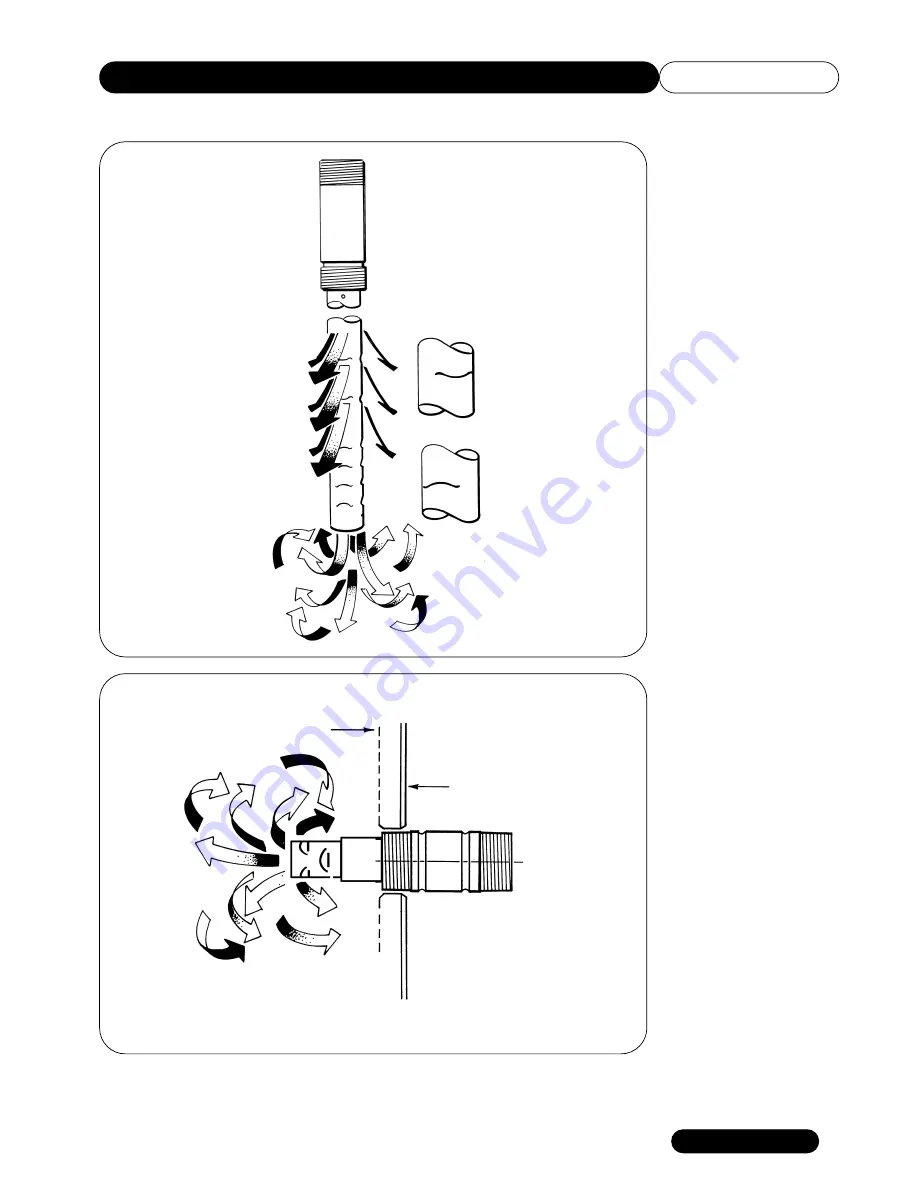
INSTALLATION
SECTION 3
15
WATER
CONNECTIONS
Hydrojet System
Mini
Hydrojet Inlet Nipple
(Side Cold Inlet
Connection)
The upper “jet
ports” direct the flow
outward to begin the
dynamic mixing
action.
The lower “jet ports”
direct the flow
inward to increase
the turbulence.
The heater is fitted with the Hydrojet Total Performance System incorporated in the cold inlet
dip tube. The tube is designed to increase turbulence and reduce sediment build up, reduce
thermal stacking and increase delivery.
All models now incorporate the
new Mini Hydrojet system on
cold inlet side connections.
This system ensures water is
directed onto the tank base
which minimises sediment build
up from day one of installation.
Heater Casing
Tank
Summary of Contents for L24/31
Page 3: ......
Page 5: ......
Page 14: ...INSTALLATION SECTION 3 9 Bulk Storage Vessel Installation Cylinder Installation Fig 3 ...
Page 22: ...INSTALLATION SECTION 3 17 Fig 8 Fig 8a ...
Page 24: ...INSTALLATION SECTION 3 WATER CONNECTIONS 19 Fig 10 Fig 11 ...
Page 27: ...INSTALLATION SECTION 3 WATER CONNECTIONS 22 Fig 14 Fig 15 ...
Page 30: ...INSTALLATION SECTION 3 WATER CONNECTIONS 25 Fig 18 Fig 19 ...
Page 51: ...PARTS LIST AND ILLUSTRATIONS SECTION 9 46 Hi Flo Model L32 143 Hi Flo Models L65 169 L81 251 ...
Page 53: ...PARTS LIST AND ILLUSTRATIONS SECTION 9 48 Hi Flo Models L62 309 L54 399 ...
Page 58: ...NOTES 53 ...
Page 59: ...NOTES 54 ...
Page 60: ......