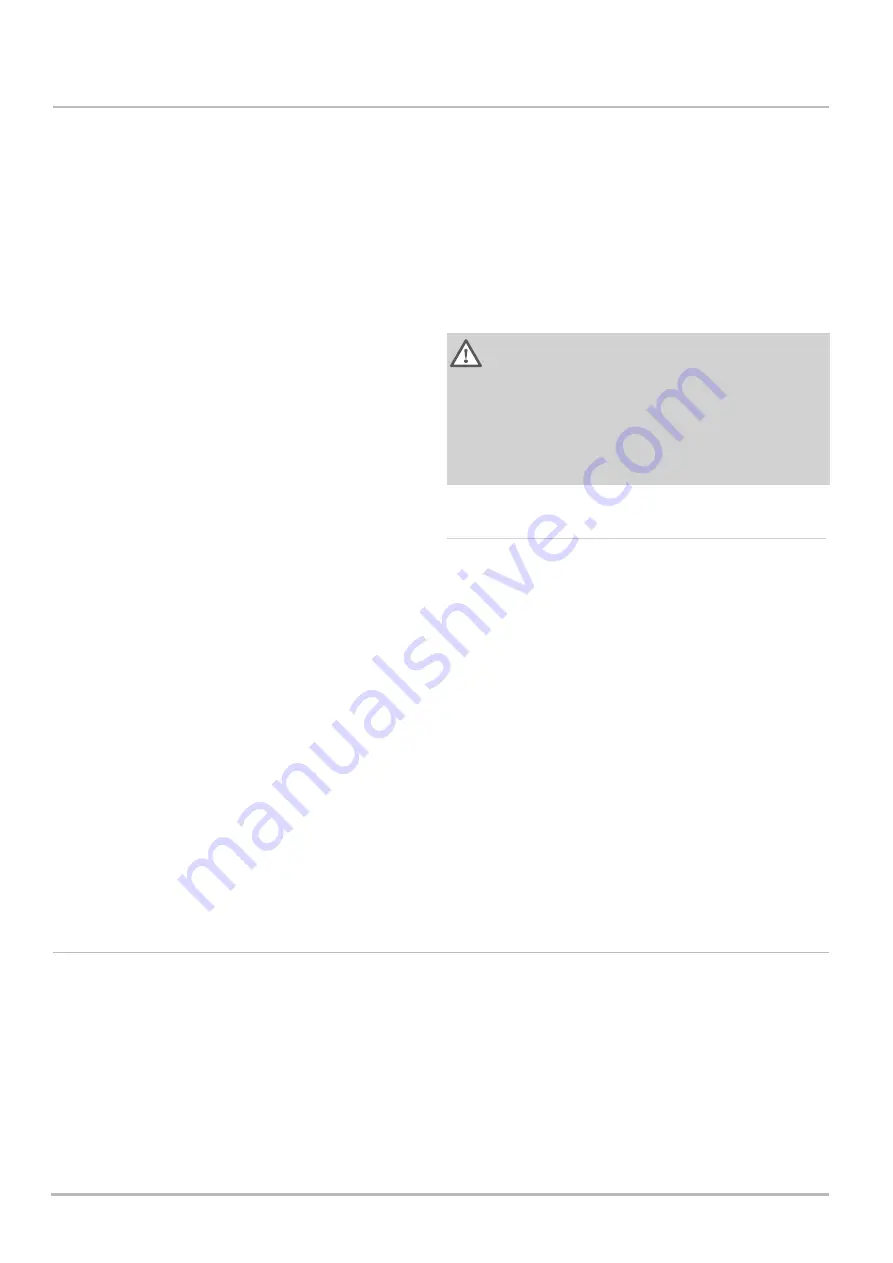
26
Issue 2 14/07/16
3
Installation
Andrews Water Heaters’ ECOflo is a Balanced Flue, Gas Water
Heater where all air for combustion is obtained from the outside
atmosphere and all flue gases are discharged to the outside
atmosphere. The flue system is a single concentric (pipe within
pipe) design where the flue products are discharged through the
inside flue tube and the combustion air supply surrounds the flue
surrounded by the outside pipe. The flue system incorporates
both combustion air supply and the flue exhaust. The flue
system component which is outside the building, takes in the
combustion air supply and discharges the flue products (whilst
keeping them separate) is referred to as the ‘direct flue terminal’.
3.25.1
Direct flue terminal
Shall terminate at least 1.5m (5ft) above any forced air inlet
located on the same wall. This provision does not apply to the
combustion air intake of a direct flue appliance or the circulating
air inlet and flue gas discharge of listed outdoor appliances.
Shall be installed with at least a 300mm (12in) flue termination
clearance from any air opening into a building.
The bottom of the direct flue terminal shall be located at least
300mm (12in) above ground.
Consideration should be given to the location of the flue
terminal. The flue terminal should be located where the
discharge of flue products does not cause a nuisance.
Consideration should also be given with regard to noise that
may be emitted by this flue system. In all cases the flue
termination must meet the requirements of BS6644.
A suitable terminal guard must be fitted if less than 2 metres
above ground level.
This is an open flued arrangement where the air is drawn into
the appliance from within the plant room (boiler house).
Permanent ventilation is required to allow correct operation of
the appliance (refer to BS 6644). Alternatively, the ventilation
can be supplied by running fresh air ducting
(150mm) direct from outside, terminating with a suitable
terminal.
The maximum ‘combined’ flue run is 32 metres. The use of 90°
and 45° bends will reduce the allowed overall length by 1.2m per
90° and 0.7m per 45° bend used along the flue run.
3.25 Flue systems
3.26 Optional conventional flue (open flue)
Warning
The direct flue systems MUST be properly installed.
Failure to do so could results in property damage or
personal injury. DO NOT install any damaged
components. Contact Andrews Water Heaters for
replacement parts. The flow of combustion air must not
be restricted. Keep direct flue terminal openings clear
of any objects likely to cause flow restriction.
Summary of Contents for ECOflo EC230/600
Page 106: ...106 Issue 2 14 07 16 ...