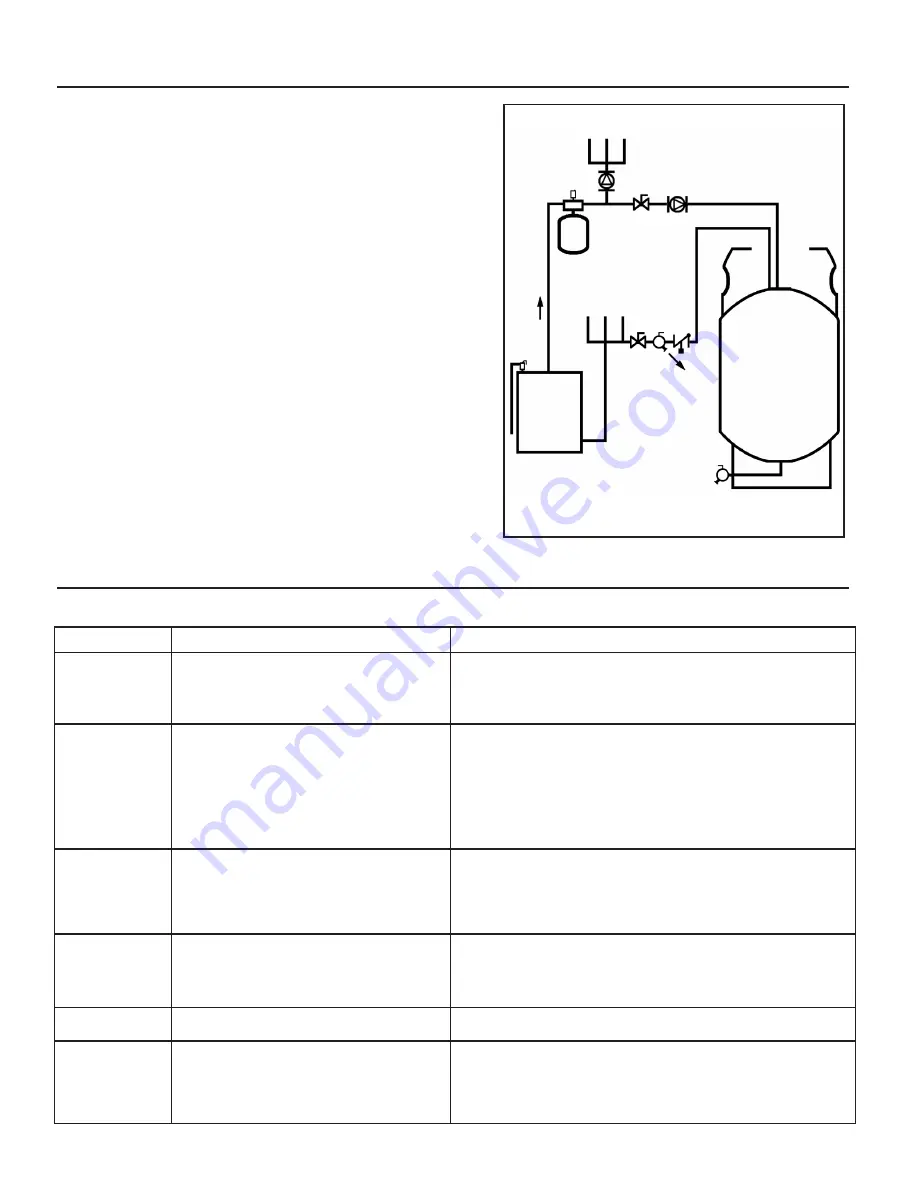
-9-
PROBLEM
POSSIBLE CAUSES
SOLUTION
No hot water
1. No power to unit
2. Circulator air-bound
3. Faulty circulator or zone valve
4. Faulty control
5. Boiler inoperable
1. Check circuit breaker, boiler emergency switch and boiler reset switch.
2. Purge air. Ensure circulator is on Boiler Supply. Check air vents.
3. Check circulator and zone valve. Repair or replace if necessary.
4. Check continuity. Switching circuits should close. If not, replace control.
5. Check boiler system. Boiler must operate to generate hot water.
Insufficient hot water
1. Demand exceeds capacity
2. Temperature too low
3. Boiler lacks output for simultaneous heat & hot water
4. Fouled heat exchanger
5. Insufficient heat exchanger flow
1. Check sizing based on household size and boiler output.
2. Increase temperature setpoint.
3. Set up for priority. If problem persists add storage or increase tank size.
4. Check Boiler Supply/Boiler Return during cold startup. If difference is less
than 20°F, clean heat exchanger as outlined below. Install water treatment
equipment to prevent recurrence.
5. Check for undersized or faulty circulator, stuck or undersized zone valve.
Ensure all shutoff valves are open. Check for stuck flow check valve. Purge
boiler loop to remove air.
Water too hot
1. Improper plumbing
2. Temperature set too high
3. Temperature sensor not fully inserted
4. Stuck zone valve
5. Flow check valve stuck open
1. If Boiler Return is plumbed to the suction-side of a heating circulator, over-
heating will occur when the home’s heat is on. Fix plumbing.
2. Reduce temperature setting.
3. Re-insert temperature sensor.
4. Repair or replace.
5. Clean, repair or replace.
Relief valve dripping
or opening
1. Thermal expansion tank undersized or missing
2. Thermal expansion tank set improperly
3. City pressure too high
4. System over temperature
5. Faulty relief valve
1. Install the properly sized thermal expansion tank.
2. Ensure precharge air pressure matches static water pressure.
3. Install a Pressure Reducing Valve (PRV) if city pressure is over 80 psi.
4. Determine cause of over temperature condition and correct problem.
5. Replace relief valve.
Discolored water
at faucet
1. Poor water quality
2. Sediment or suspended particles
1. Have water tested for contaminants.
2. Install sediment filter, purge unit more often to avoid future problems.
Boiler will not operate
when calling for
hot water
1. Improper or loose wiring
2. Boiler high limit has been reached
3. Post Purge (POS) set too high
4. Problem with boiler system
1. Check connections against wiring diagrams in this manual.
2. Boiler will periodically cycle on and off during operation.
3. Post Purge shuts the boiler off prior to reaching domestic setpoint. If set too
high, the boiler may not have enough energy to raise the water temperature
to setpoint. Reduce POS or set to 0 if the problem persists.
5. Have boiler diagnosed for proper operation.
8. Startup Procedure
9. Troubleshooting
1. PURGE HEAT EXCHANGER:
The heat exchanger should be free
of large air pockets to allow the circulator to operate properly. Using
the diagram below as a guide, isolate the boiler return line and
flush the loop until large air pockets are purged. After this, the air
elimination equipment will collect smaller air bubbles.
2. FILL TANK:
Open the hot water fixture furthest from the heater.
Open the cold water supply and allow the water to run until air stops
emerging. Air pockets may appear at any hot water fixture. This is
considered normal and will clear as hot water is used.
3. START HEATER:
Turn power on to the unit. Digital Control models
come pre-set to 120°F for safety. Mechanical controls should have
the knob rotated to the 120°F mark. The circulator or zone valve
should operate and the boiler should start.
4. CHECK OPERATION:
The water heater will begin to heat.
Depending upon the size of the water heater, output of the boiler
and the space heating load, the unit should typically reach set
temperature within 15 to 60 minutes. If heating does not occur,
consult the troubleshooting section in this manual.
Note:
Large
heaters coupled with small boilers may exceed this time period
upon initial startup.
5. SET TEMPERATURE:
The control should be set to the minimum
temperature consistent with the user’s needs. This maximizes
efficiency and reduces scald potential.
6. The water heater and system should be periodically checked by a
licensed professional at least annually and more often as system ages.
1. Close
Return
3.
Purge
Air
2. Fill
Boiler