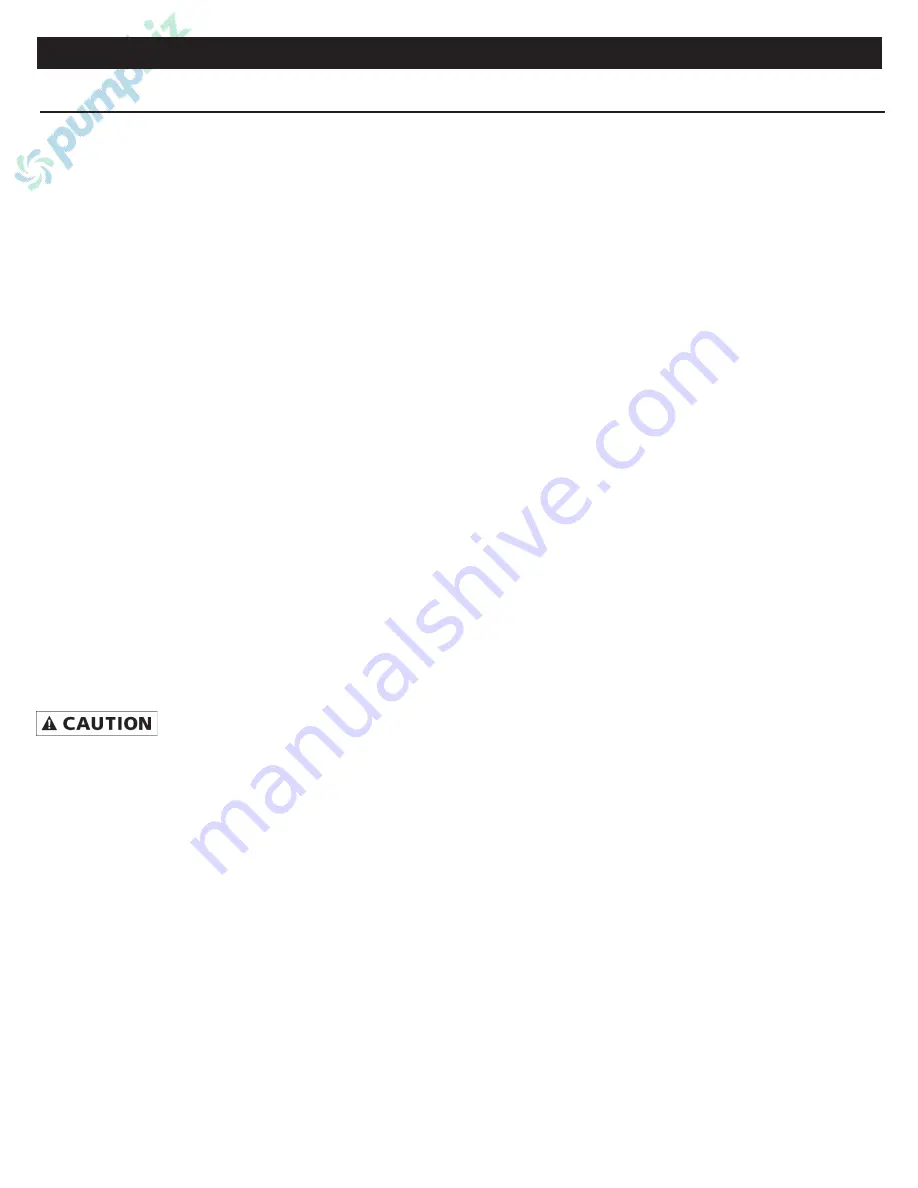
Specifications Information and Repair Parts Manual
316A-95, 316B-95, 393A-95, 393B-95,
394G-95, 394H-5, 394J-95, 394K-95, 399D-95
394K-250-00
2
1/2017
8. Remove the shaft sleeve from the motor shaft if the sleeve is damaged or
scored. The shaft sleeve is fixed to the motor shaft with pliable sealant,
heat may be required to breakdown the sealant. If the shaft sleeve is
smooth it does not need to be replaced. Clean shaft sleeve of any debris
or remnants of the old seal head. Replace damaged shaft sleeve with
new replacement. IMPORTANT: Before installing a new shaft sleeve apply
a bead of non-hardening pliable sealant (such as Permatex® Form-A-
Gasket® No. 2) to motor shaft shoulder.
394 & 399:
1. Remove four bolts (Ref. No. 19). Pull casing assembly (Ref. No. 16) from
adapter.
2. Remove casing O-ring (Ref No. 33). Remove two screws (Ref. No. 15).
Pull volute (Ref. No. 14) from adapter.
3. Using a hex key remove impeller screw (Ref. No. 11) and O-ring Ref. No.
34). Slide impeller (Ref. No. 10) from motor shaft.
4. Remove the impeller shim(s) (Ref. No. 13) and impeller drive key (Ref.
No. 12).
5.
Slide the seal head (Ref. No. 9) off the shaft sleeve (Ref. No. 5).
6. Remove four screws (Ref. No. 3). Pull adapter (Ref. No. 2) from motor.
7. Push seal seat (Ref. No. 6) from adapter. Clean seal seat bore in adapter.
8. Remove the shaft sleeve from the motor shaft if the sleeve is damaged or
scored. The shaft sleeve is fixed to the motor shaft with pliable sealant,
heat may be required to breakdown the sealant. If the shaft sleeve is
smooth it does not need to be replaced. Clean shaft sleeve of any debris
or remnants of the old seal head. Replace damaged shaft sleeve with
new replacement. IMPORTANT: Before installing a new shaft sleeve apply
a bead of non-hardening pliable sealant (such as Permatex® Form-A-
Gasket® No. 2) to motor shaft shoulder.
IMPORTANT:
Care should be taken to ensure that the same number of impeller
shims are replaced behind the impeller as were removed. The impeller shims
are located directly behind the impeller.
The precision lapped faces on the mechanical seal are easily damaged.
Handle your replacement seal carefully.
9. Carefully wipe the polished surface of the new seal seat with a clean cloth.
10. Wet rubber portion of the seal seat with a light coating of soapy water.
11. While wearing clean gloves or using a clean rag, press seal seat squarely
into adapter recess. Avoid scratching the polished surface. If seal seat will
not position properly, place a cardboard washer over the polished surface
and use a piece of pipe to press in, firmly but gently.
12. After seal seat is in place, dispose of cardboard washer. Check that seat
is clean and has not been marred.
13. Using a clean cloth, wipe the shaft and make certain that it is perfectly
clean.
14. Secure the adapter on the motor mounting surface with fasteners.
15. 15. Wet the rubber portion of the new seal head with a light coating of
soapy water. Slide seal head over motor shaft (316) or shaft sleeve (393,
394, & 399) until rotating ring of seal head meets seal seat face.
16. Reinstall any impeller shims that have been removed. (See “Shim
Adjustment” section).
NOTE:
Always inspect O-ring seals. Replace when cracked or worn. Wet
O-ring with soapy water for ease of installation.
17. 316; screw impeller back in place. Tighten until it is seated against shims
and shaft shoulder. 393, 394 & 399; Install impeller drive key into motor
shaft keyway. Align impeller keyway with drive key, slide impeller onto
motor shaft. Replace impeller O-ring and install impeller screw. Tighten
screw until impeller is seated against shims and shaft sleeve.
18. Remount volute with screw(s).
19. Refer to section entitled “Shim Adjustment” at this time if shaft sleeve or
any parts, other than shaft seal, have been replaced.
20.
316 & 393; Inspect position of flapper valve (Ref. No. 16) to ensure proper
movement and sealing. 394 & 399; Inspect position of volute gasket (Ref.
No. 35) to ensure proper sealing of volute to casing.
21.
Replace casing O-ring seal on volute outside flange diameter.
22. Remount casing.
23. Remount any other parts.
SHIM ADJUSTMENT
When installing a replacement impeller, motor, shaft sleeve, adapter or volute,
it may be necessary to adjust the number of impeller shims to ensure proper
running clearance between impeller and the volute wear surface. Proceed as
follows:
NOTE:
Proper running clearance is 0.020”.
1. For impeller replacement, add one (1) shim in addition to those removed
originally.
2. For motor replacement, add one (1) shim in addition to the shims removed
during disassembly.
3. Reassemble the pump as described in steps 16, 17, and 18. (See
“MECHANICAL SEAL REPLACEMENT” section).
IMPORTANT:
Check the shaft to make sure it is turning freely (rotate the
impeller by the impeller lock bolt with an Allen wrench or by the acorn nut
with a socket wrench). If it turns freely, check to ensure that the volute and
adapter are fitted metal-to-metal where they meet on the outside. If they are not
metal-to-metal, tighten fasteners and recheck the shaft for free turning. Tighten
carefully, turning the shaft while tightening so that the motor bearings are not
damaged in the event that too many shims were installed. If shaft seizes before
fasteners are completely tight, disassemble the pump and remove one (1) shim
and repeat reassembly.
NOTE:
When adding or removing shims, it is best to proceed with a 0.010”
increment each time. If motor shaft does turn freely, add shims until it does
strike, then remove a 0.010” shim. This will ensure maximum performance.
IMPELLER, WEARPLATE, AND VOLUTE REPLACEMENT
316: Impeller (Ref. No. 3) and volute (Ref. No. 2), 393: Impeller (Ref. No. 3),
volute (Ref. No. 2), and wear plate (Ref. No. 23), 394 & 399: Impeller (Ref. No.
10), volute (Ref. No. 14), and wear plate (Ref. No. 6) are subject to wear only
by abrasive sand or sediment laden liquids. If badly worn, all these parts can
be replaced easily and the pump thus restored to full efficiency.
Sewage/Trash Pumps
Summary of Contents for 316A-95
Page 15: ......
Page 16: ...www amtpump com...