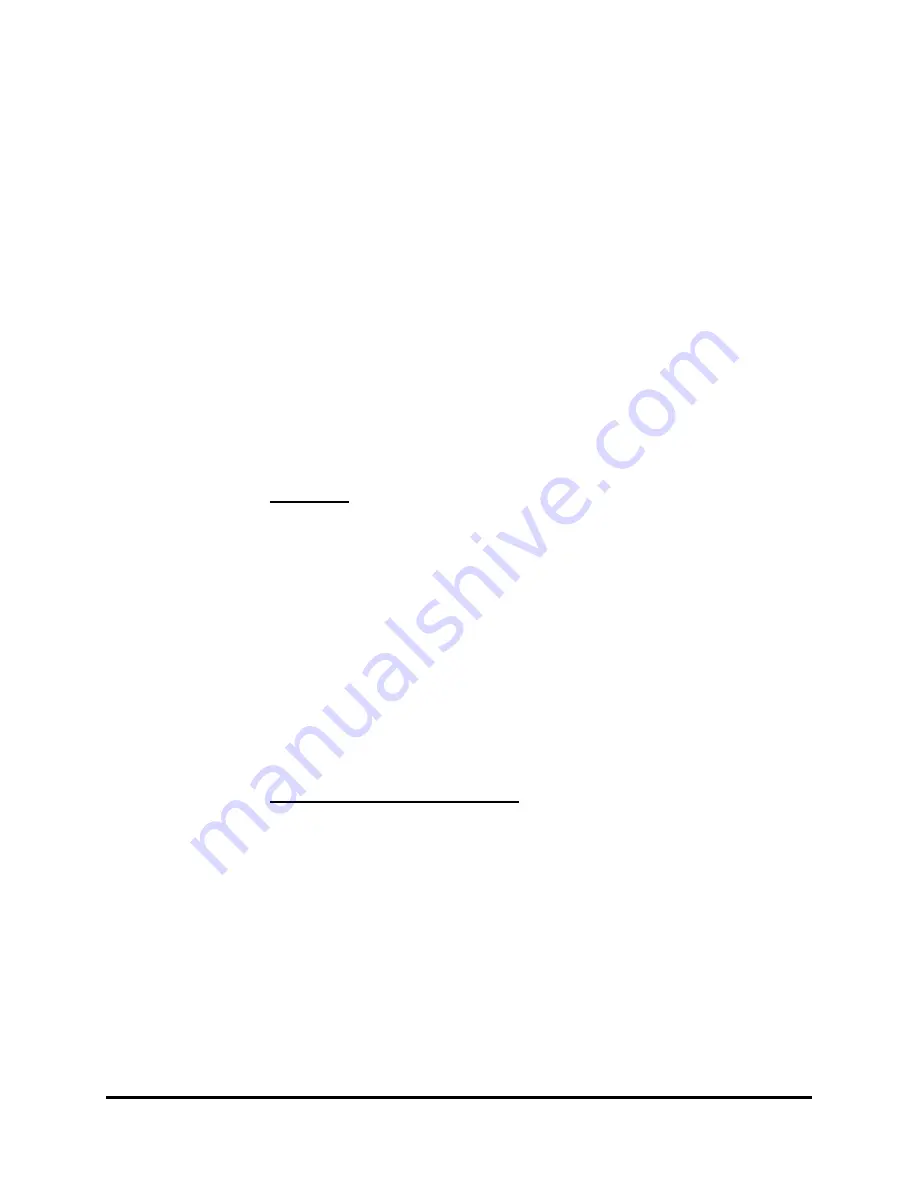
Table of Contents
Copyright 2009, AMS, Proprietary Information, All Rights Reserved
P/N 0010-0667, Rev A
Section Three Installation/Transportation/De-Installation
SYSTEM
INSTALLATION
3-1
Unpacking
the
System
3-1
Condition
of
Laser
and
Container
3-1
Remote Interlock
3-1
ADDING WATER
3-1
Adding
internal
Water
3-1
ELECTRICAL
SERVICE
REQUIREMENTS
3-2
VERIFICATION of SYSTEM OPERATION AND POWER MEASUREMENTS 3-2
DE-INSTALLATION
OF
SYSTEM
3-3
TRANSPORTATION
OF
SYSTEM
3-3
Section Four Cooling
COOLING
SYSTEM
4-1
Solenoid
Water
Valve
4-1
Water to air heat exchanger
INTERNAL
WATER
COOLING 4-1
Description
4-1
Fill
and
Drain
Ports
4-1
Fan
4-1
Pump
and
Motor
4-2
COMPONENT
REPLACEMENT
4-2
Section Five Electronic Components
SYSTEM
PC
BOARD
DESCRIPTIONS
5-1
Fiber Port
5-1
FiberLife
5-1
Resonator
Control
5-1
Touch
Screen
Controller
5-1
Laser
Power
Supply
5-2
Master Control
5-2
Power
Distribution
5-2
COMPONENT
REPLACEMENT
5-2
Summary of Contents for GreenLight XPS
Page 1: ...Service Manual...