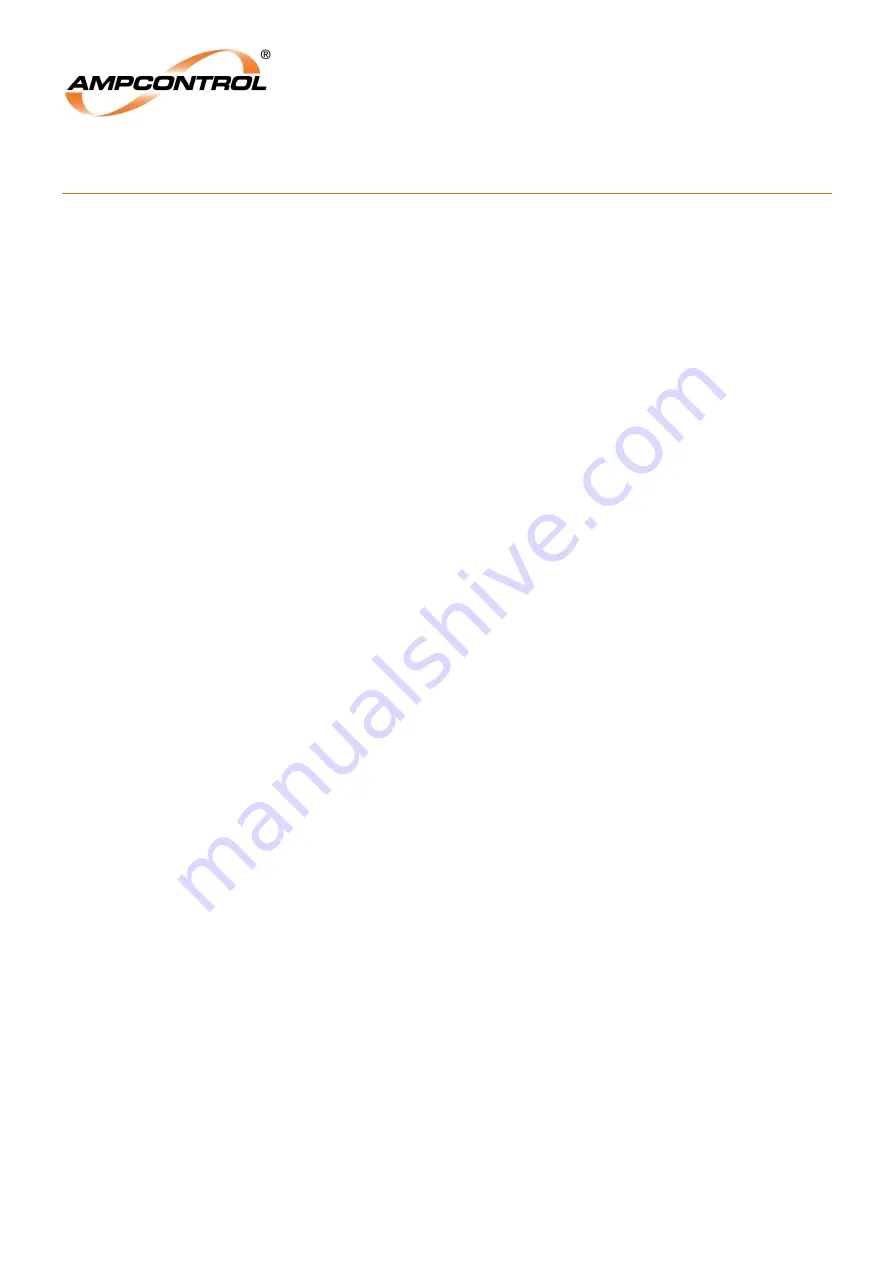
Ampcontrol Pty Ltd
– ABN 28 000 915 542
PF1 USER MANUAL
MAG-165 Version 6
– March/2020
Uncontrolled Copy - Refer to Ampcontrol Website for Latest Version
Page 7 of 71
A
P
P
R
OV
E
D
FOR
E
X
T
E
R
N
A
L
D
IS
TR
IB
U
T
ION
–
P
R
OP
E
R
T
Y
OF
A
M
P
C
ON
TR
OL
P
T
Y
LTD
–
N
O
T
T
O
B
E
R
E
P
R
OD
U
C
E
D
I
N
P
A
R
T
TABLE OF TABLES