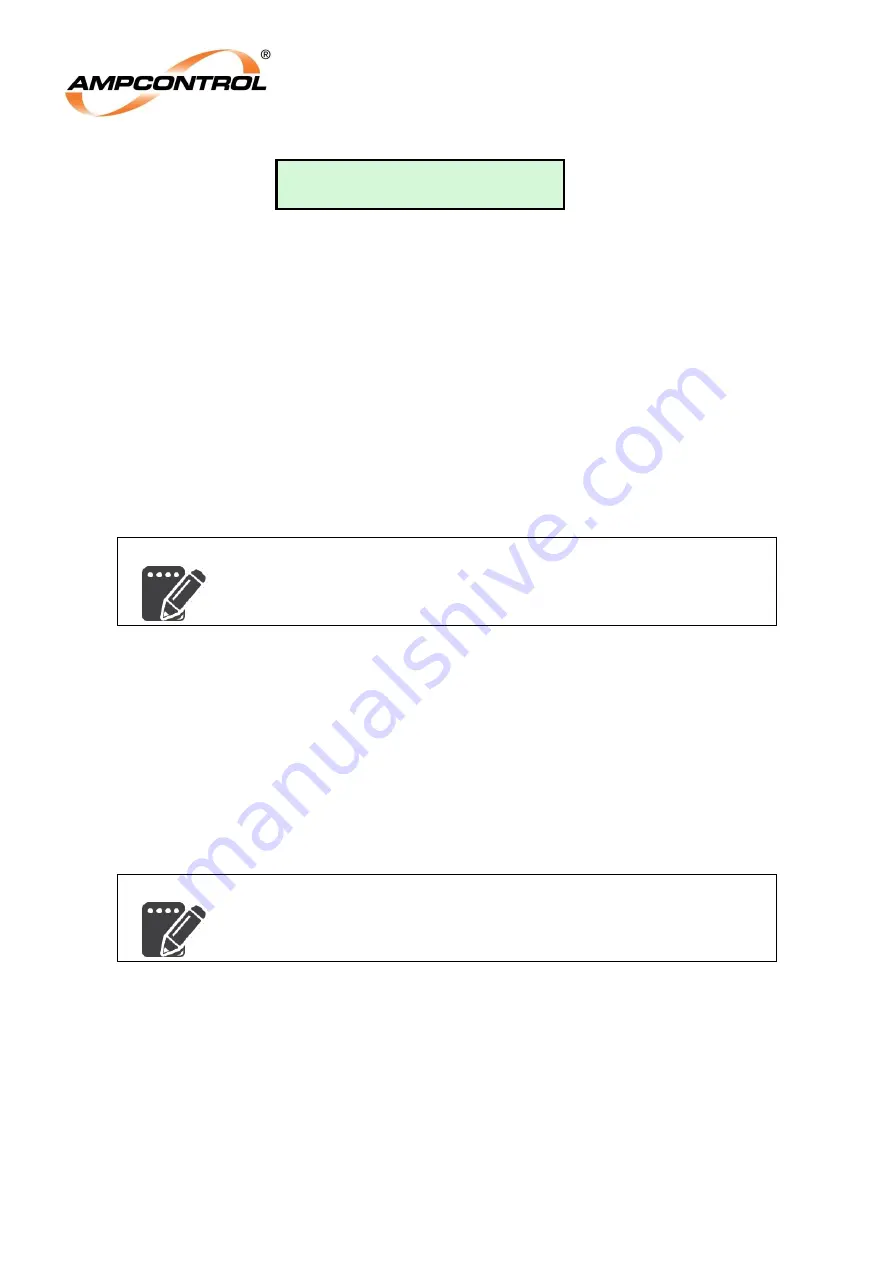
Ampcontrol Pty Ltd
– ABN 28 000 915 542
IPM V2 USER MANUAL
IPM2B003 Revision 15
– MAY/18
Uncontrolled Copy - Refer to Ampcontrol Website for Latest Version
Page 39 of 83
A
P
P
R
OV
E
D
FOR
E
X
T
E
R
N
A
L
D
IS
TR
IB
U
T
ION
–
P
R
OP
E
R
T
Y
OF
A
M
P
C
ON
TR
OL
P
T
Y
LTD
–
N
O
T
T
O
B
E
R
E
P
R
OD
U
C
E
D
I
N
P
A
R
T
Ave: 0 Amp Ir: 0%
Ibal: 0% Iel: 0%
7.4 Residual Current Signal
The three phase current signals are summed electronically in the IPM to produce a residual current
signal that can be used to detect earth fault currents. If the residual current signal exceeds the trip level
for the selected trip time, a trip occurs, tripping the MCR relay. The fault is latched.
To reset the relay following a residual current trip, operate the reset key/digital input.
L2: Displays the 3 phase currents as a % of the FLC
L
3: Displays the average current and the % residual current as „Ir‟
L4: Displays the current balance and the % of leakage current
The trip level is selected via the „Residual iTrp‟ setting (Level 6, Screen 11) and is adjustable from 10%
to 250% FLC and „off‟. The trip time is selected via the „Res.trip time‟ setting (Level 6, Screen 12) and is
adjustable from 100ms to 5 seconds. Setting the trip level to „off‟ disables this function.
NOTE
The residual current function can be used even if a core balance toroid
is used for earth leakage protection. It can be used to provide some
detection of wiring/CT/internal relay faults.
7.5 Undercurrent Trip
Undercurrent protection is enabled as soon as the main contactor is closed (indicated by closing the MCI
input). Selecting a value of
“None” will inhibit this function. If any phase drops below the selected trip
setting for a period of 4 seconds then the outlet
is stopped. This raises the “Under Current Trip” alarm
and is recorded in the event log as “Und.I Trp”. To reset the relay, operate the reset button.
The trip level is selected via the „Under I Level‟ setting (Level 6, Screen 10). The trip level is selectable at
32%, 40%, 48%, 56%, 64%, 72%, 80%, 88%, and 96%. Setting the trip level to
“None” disables this
function.
NOTE
This function is used when in snore mode and must be set to an
appropriate level
– note that there is a 4 second delay before a trip.