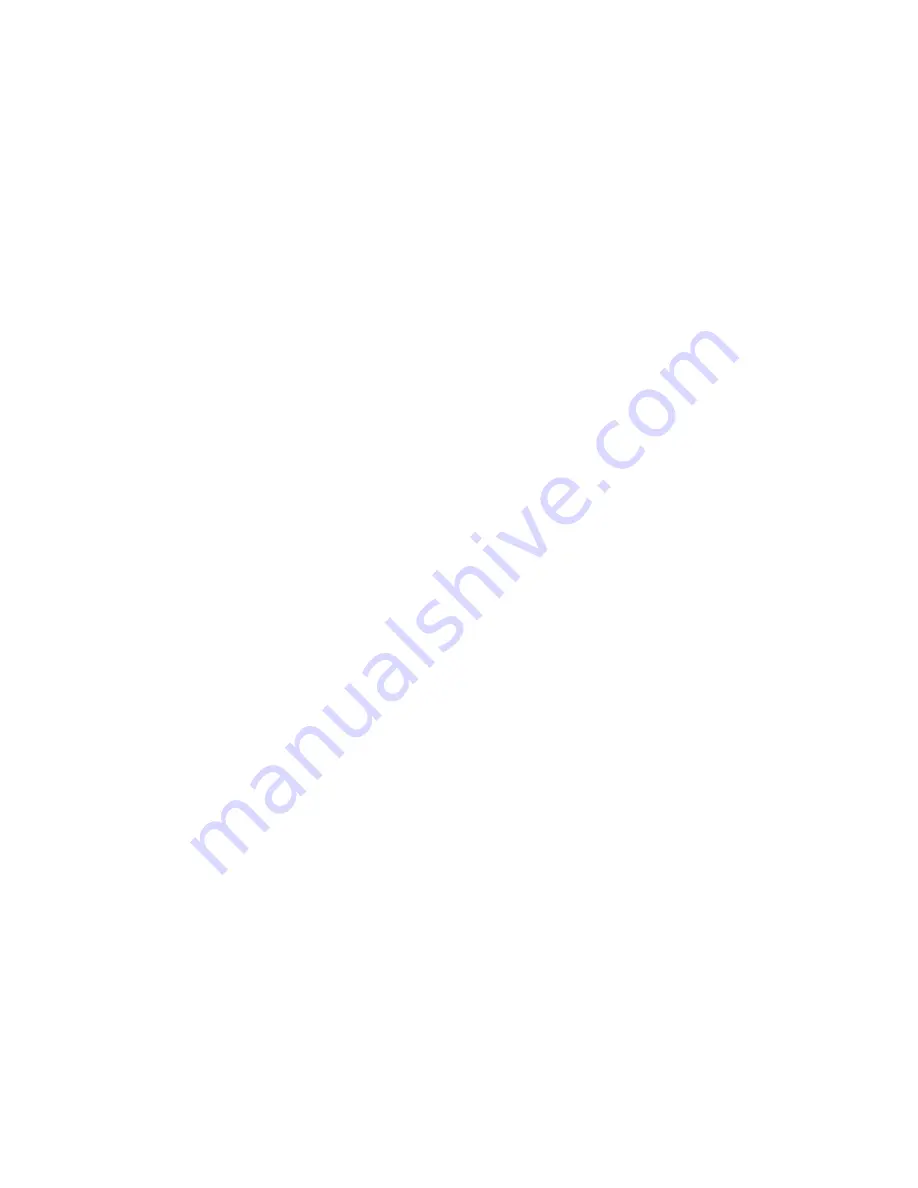
7
2.10 STANDARD EQUIPMENT
The equipment listed below are the standard
o n e s :
2.10.1 Standard accessories
Once you have removed the packing, please check
the presence of following accessories:
- N.1 nail head
mm. 7
- N.1 nail head
mm.10
- N.1 nail head
mm.15
- N.1 L shaped pressure pad
- N.1 Allen Wrench 5 mm. for V-nails head replacement
- N. 4 adjustable feet.
- N.1 pressure gauge
- N.1 fast clutch fitting
- N.1 Brass rod magnet to remove V-nails
- N.1 double hydraulic hold down
- N.1 double & triple mechanical hold down
2.10.3.Customized optional accessories
Thanks to its versatility this machine can be
‘custom-made’ to meet our users’ requirements,
by using additional accessories that can make
frame assembling easier: e.g. special fences
for peculiar moulding shapes, special clamps
to ensure the mouldings are locked properly
during V-nail firing, and so on. You can have
your local machine shop make these for you.
2.10.2 Upgrading and implementing mechanical
parts
The machine has been designed and developed
based on modular standards, therefore the
existing equipment can be further upgraded with
additional accessories that will not alter its
basic structure.
Technical upgrades on the machine model, if
any, will be such that they can be installed at
any time without requiring any substantial
modifications to the machine structure.
2.9 TECHNICAL DATA
We have listed below the Machine data and
technical characteristics to which you can make
reference for any eventual contact with Producer
for Technical Assistance.
- Frames thickness min-max
.197” - 3.15”
- Frames width
min-max
.39” - 3.94”
- Max distance between V- nails
4.72”
- V-nail magazine capacity
n. 220
- V-nails size
7, 10, 15 mm.
- V-nails size on request
3, 5, 12 mm.
- Pneumatic supplying
Psi 80-110
- Power supplying
120 V
- Weight
about 254 LB
- Height of working bench
37.8”
- Overall dimensions 30.3”x30.3”x5.9”
- Max programming capacity
n. 1400
- Max V-nails inserting position n. 10
- Max V-nails stacking per position n. 9
- Serial linking support
type RS 232
- Air consumption per cycle
4 NI/5 Bar
2.11 ELECTROMAGNETIC AMBIENT
The Machine is designed to operate properly in
an industrial electromagnetic ambient, being
included in the following Norms about Emission
and Immunity:
EN 50081-2 Electromagnetic compatibility-
Generic Norm on Emissions-2nd part-Industrial
Environment-(1993)
EN 50082-2 Electromagnetic compatibility-
Generic Norm on Immunity-2nd part-Industrial
Environment-(1995)
Summary of Contents for Mitre-Mite VN4 MemoryProgram
Page 1: ......
Page 32: ...32...
Page 33: ...33...
Page 38: ...38 ATTACHMENT C PLATES DISLOCATION...
Page 41: ...41...