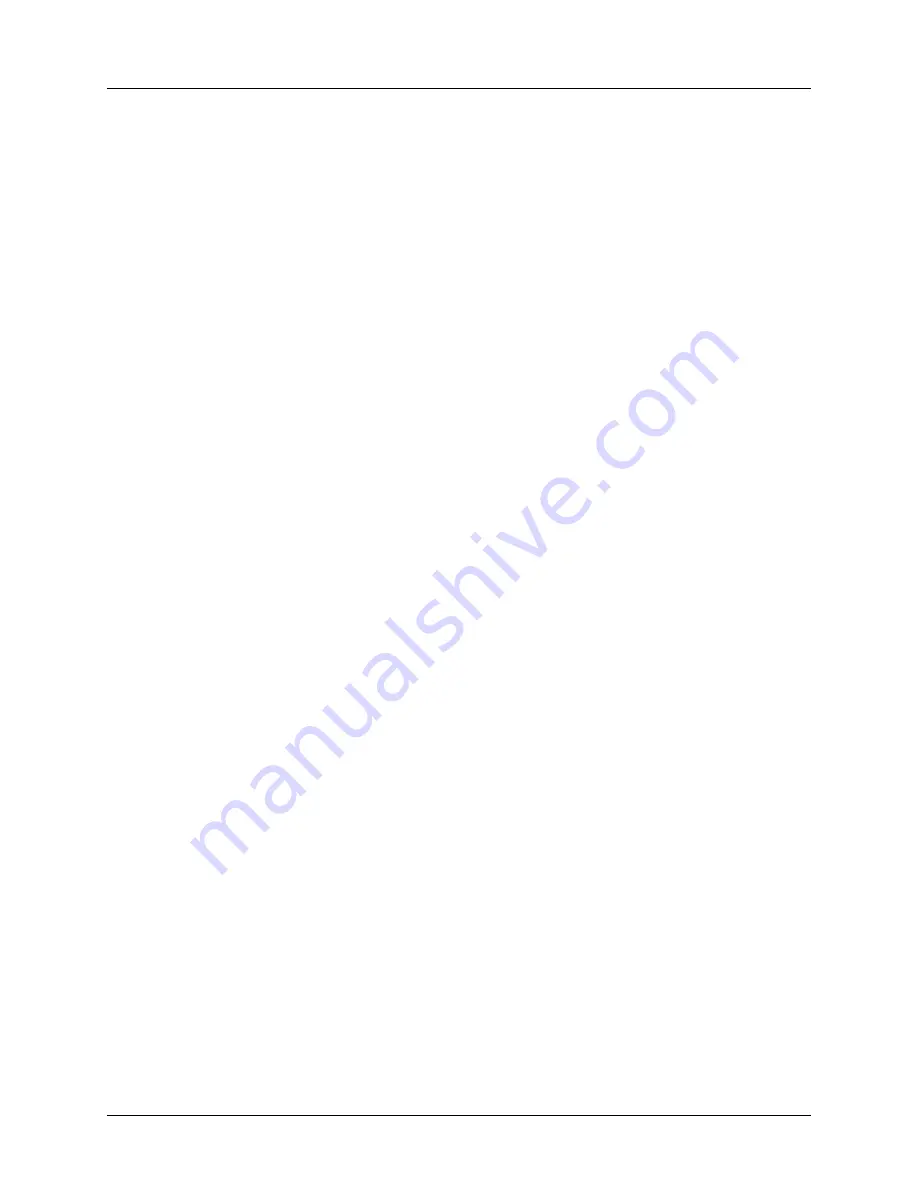
Model 420 Power Supply Programmer
Model 420 Power Supply Programmer Configuration
AMI Order Number:_____________________
Shipping Date:_________________________
Model 420 Serial #:______________________
Firmware Revision:_____________________
Input Power Requirements:___________________________________________________________
Configuration Notes:
_____________________________________________________________________________________
_____________________________________________________________________________________
_____________________________________________________________________________________
_____________________________________________________________________________________
_____________________________________________________________________________________
_____________________________________________________________________________________
_____________________________________________________________________________________
_____________________________________________________________________________________
AMI Warranty
All products manufactured by AMI are warranted to be free of defects in materials and
workmanship and to perform as specified for a period of one year from date of shipment. In
the event of failure occurring during normal use, AMI, at its option, will repair or replace all
products or components that fail under warranty, and such repair or replacement shall
constitute a fulfillment of all AMI liabilities with respect to its products. Since, however,
AMI does not have control over the installation conditions or the use to which its products
are put, no warranty can be made of fitness for a particular purpose, and AMI cannot be
liable for special or consequential damages. All warranty repairs are F.O.B. Oak Ridge,
Tennessee, USA.
Copyright © 2002 by American Magnetics, Inc., Oak Ridge, Tennessee, USA
Rev. 7
1 Configuration
Summary of Contents for 420
Page 2: ......
Page 4: ......
Page 6: ......
Page 12: ...x Rev 7 List of Tables ...
Page 18: ...xvi Rev 7 Foreword Safety Summary ...
Page 22: ...4 Rev 7 Introduction Front Panel Layout ...
Page 24: ...6 Rev 7 Introduction Rear Panel Layout ...
Page 30: ...12 Rev 7 Introduction Operating Characteristics ...
Page 54: ...36 Rev 7 Installation Power Up Procedure ...
Page 82: ...64 Rev 7 Operation Summary of Operational Limits ...