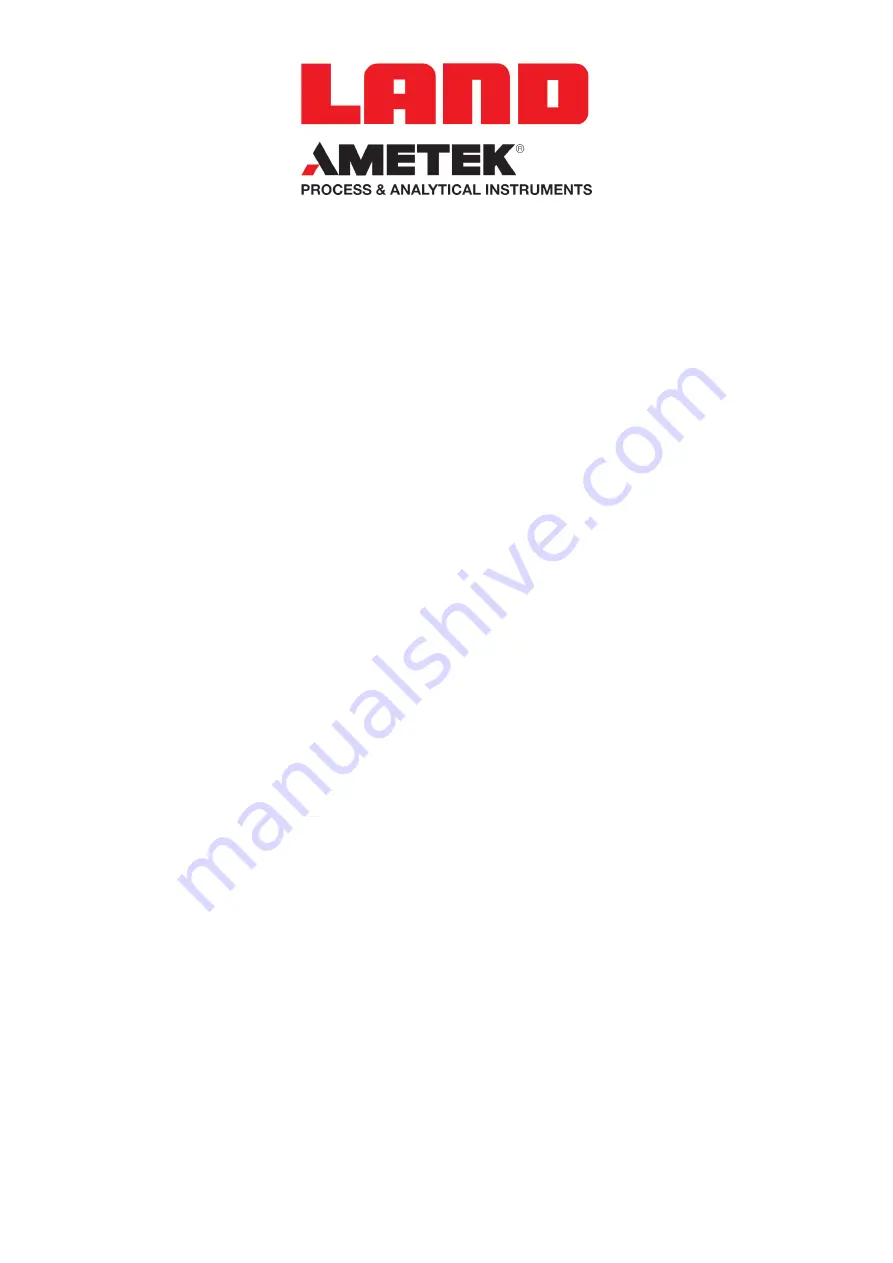
Issue 7 January 2014
Gas Monitoring Products
Standard Terms of Warranty
Land Instruments International warrant all products of our own manufacture to be within specified limits of calibration,
if any, when despatched from our works. Also that they are free from defects in material and workmanship for normal
use and service when used for their intended purpose within the limits of our specification. The period of warranty,
with respect to defects in material and workmanship, will be one year from date of despatch, or readiness for despatch
should delivery be delayed by the customer who has been notified of the readiness at or after the acknowledged
estimated date of despatch.
Land Instruments International guarantees to repair any defective workmanship or replace at its own option any
defective parts in any product of its manufacture, provided that the defective instrument is returned to our works
free of charge and securely packed. Also, provided that the said goods are found to be solely defective due to faulty
design, materials or workmanship and not by improper use or accident.
Items which under their normal course of use or storage, age or deteriorate e.g. measuring cells, batteries, vacuum
tubes, thermocouples, are not covered by this warranty, and will be charged for if replaced together with labour
charges for any work found not to be covered by the warranty and any transport or import charges incurred by Land
Instruments International at the customers expense.
Equipment or components purchased by Land Instruments International from other manufacturers and used with or
within Land Instruments International equipment bear only the warranty of the original manufacturer.
Warranty work will only be carried out on site on receipt of an official order from the customer who will be charged for
all travelling time plus travelling and living expenses involved to carry out the work. Should the said faulty operation
not be the cause of the instrument’s faulty design, materials or workmanship, but due to application conditions,
Land Instruments International reserve the right to charge additionally for all labour on establishing this at the
customer’s works.
Warranty cover is subject to the correct planned maintenance being done in accordance with the published service
schedule. Failure to follow the planned maintenance will void the warranty terms. Any warranty claim in this event will
be at the discretion of Land Instruments International. Whilst every care is taken in the manufacture of our products,
we can accept no responsibility for any consequential loss, however caused, through the failure of any of our products
to operate accurately or correctly.
All products except 4500 MkIII
The standard warranty on new instruments is a 1-year return-to-base warranty. If repairs are performed at site, then
travelling time and expenses will be charged at standard rates. Purchased Spare Parts are warranted for 1 year from
date of shipment, carriage included. If a Spare Part is supplied under warranty, then this part is only warranted for
the residue of the applicable warranty period. Calibration filters are not warranted against any damage or change in
characteristic that may occur due to mishandling.
Model 4500 MkIII
The standard warranty on new instruments is a 3-year return-to-base warranty. If repairs are performed at site, then
travelling time and expenses will be charged at standard rates. Purchased Spare Parts are warranted for 1 year from
date of shipment, carriage included. If a Spare Part is supplied under warranty, then this part is only warranted for
the residue of the applicable warranty period. Calibration filters are not warranted against any damage or change in
characteristic that may occur due to mishandling. The 4500 MkIII light source has a lifetime warranty.
Exclusions
1.
Warranty subject to the analysers being used in the manner for which they were designed.
2.
Warranty subject to all recommended maintenance being performed as defined in the operating or service
manual or in the quotation.
3.
The following consumable items are specifically excluded: All filters, Electrochemical cells, Chemical Drying
Agents, Batteries.
MARCOM0300