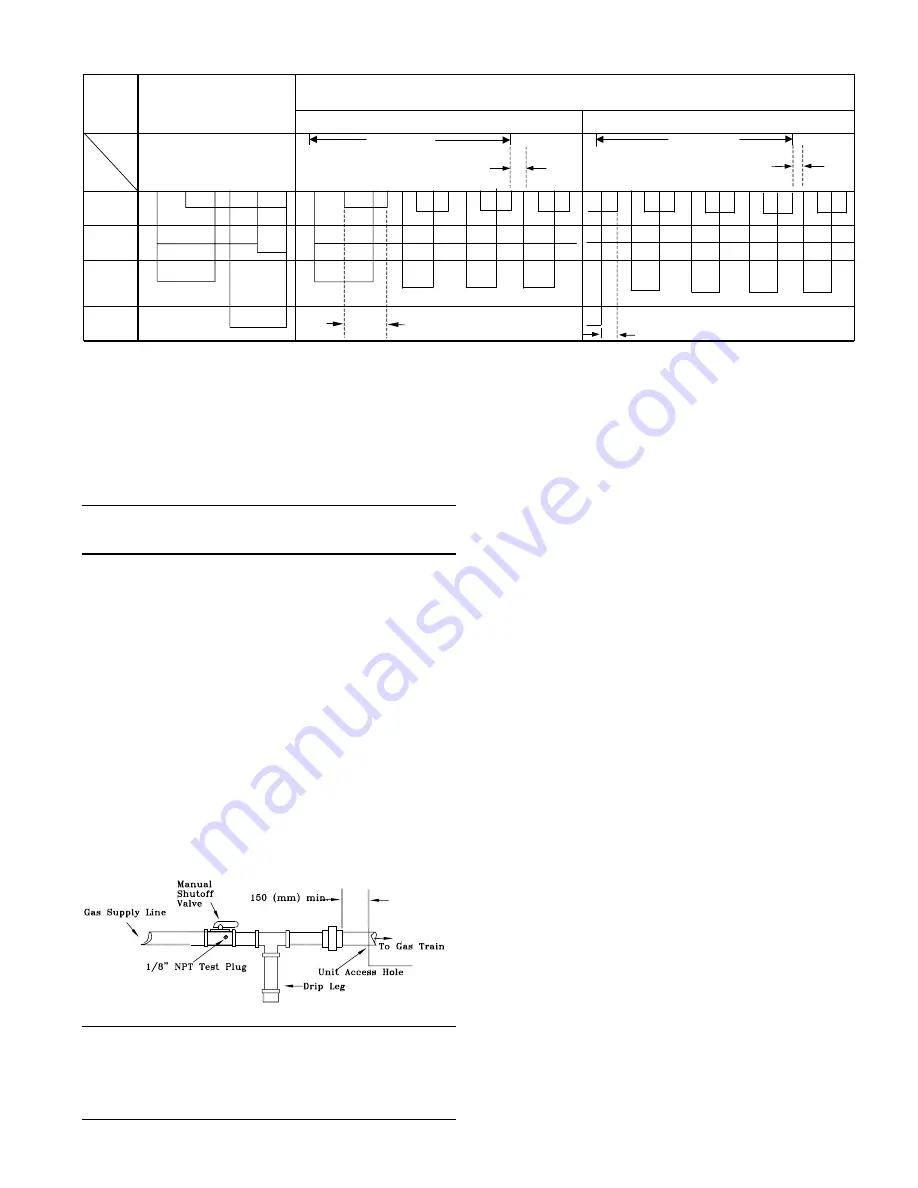
14
Figure 7- Trane Gas Heating Module Ignition Controller Start and Safety Sequence
Normal Sequence
Sequence With Safety Measures
(Stop by Regulation)
At Ignition with Flame Signal Fault
At Disappearance of Flame Signal
Time (s)
3 Retries 186.3 s
3 Retries 186.3 s
Operations
0
54
59.
7
60.
9
Manuel
R
egul
at
io
n
0
54
59.
7
62.
1
72min
etc..
0
0,
98
2
55
59.
7
62.
1
72min
etc..
Gas Valve
Fan
Electrode
Heating
Ionisation
TSA = 8,1s
TSE = 0,96S maxi
Use the following steps to complete the installation of the unit
gas piping. (See Figure 8)
1. Install a tapped, style A (1/8 inch NPT tap) shut-off gas cock
at the end of the gas supply line near the unit. Be sure the
tapped gas cock is downstream of the pressure regulator, if
used.
Note: The shut-off gas cock must be installed
outside the unit, and should meet the specifications
of all applicable National and Local Codes.
2 . Install a ground union joint downstream of the shut-off
cock. This joint must be installed outside of the unit.
3 . Install a drip leg (at least 150 mm (6") in depth) next to the
union as shown in Figure 8. This drip leg is required to col-
lect any sediment that may be deposited in the line.
4 . Before connecting the piping circuit to the unit, bleed the air
from the supply line. Then cap or plug the line and test the
pressure at the tapped shut-off cock. The pressure reading
should not exceed 35 mBar (14 inches water column).
5. Connect the gas piping to the unit. Check the completed
piping for leaks using a soap and water solution, or equiva-
lent.
Figure 8
Gas Piping Schematic
IMPORTANT NOTE: THIS UNIT USES A NEGATIVE
REGULATION GAS VALVE. AT START-UP, THE
OUTLET PRESSURE SHOULD BE CHECKED AND
ADJUSTED IF REQUIRED TO A (NEGATIVE) -50Pa (-
0.2" OF WATER COLUMN.) NEVER ADJUST THE
REGULATOR TO A POSITIVE PRESSURE.
Manifold Pressure
The unit manifold pressure regulator (located on the gas
valve) is factory installed and adjusted to provide the rated unit
heating capacity. The required manifold pressure is factory set
at (negative) - 50 Pa (2 inches of water column) for natural
and LP gas.
Check the manifold pressure at the unit gas valve. Do not ex-
ceed the recommended pressure shown on the unit name-
plate.
Filter Installation
To gain access to filters, remove the evaporator fan access
panel. Each unit ships with 50 mm (2") filters. Number and
size of filters is determined by size and configuration of the
unit. Refer to the unit “Service Facts” for filter requirements.
Evaporator Fan Adjustment
Use the following procedure to determine the proper adjust-
ment of the evaporator fan sheaves for a specific application.
1. Determine total system external static pressure Pa (inches
of water column) with accessories installed. To accomplish
this:
a. Obtain the design airflow rate and the design external
static pressure drop through the distribution system. Your
sales representative or the design engineer can provide
you with these values.
b. Using the table from the Service Facts, add the static
pressure drop of the accessories installed on the unit.
c. Add the total accessory static pressure drop (from step
1b) to the design external static pressure. The sum of
these two values is the total system external static
pressure.
2. Use the table(s) in the Service Facts to find the external
static pressure Pa (inches of water column) that most
closely approximates total system external static pressure.
Then locate the appropriate airflow rate (in m3/h) for your
unit. The value obtained represents the kW for the evapora-
tor fan motor and the fan RPM.
Summary of Contents for YK-IOM-2
Page 10: ...10 Figure 5 Figure 6 Detail of the Gas Section...
Page 17: ...17 Figure 11A Zone Sensor Interconnections...
Page 18: ...18 Figure 11B Conventional Thermostat Interconnections...
Page 23: ...23...
Page 24: ...24...