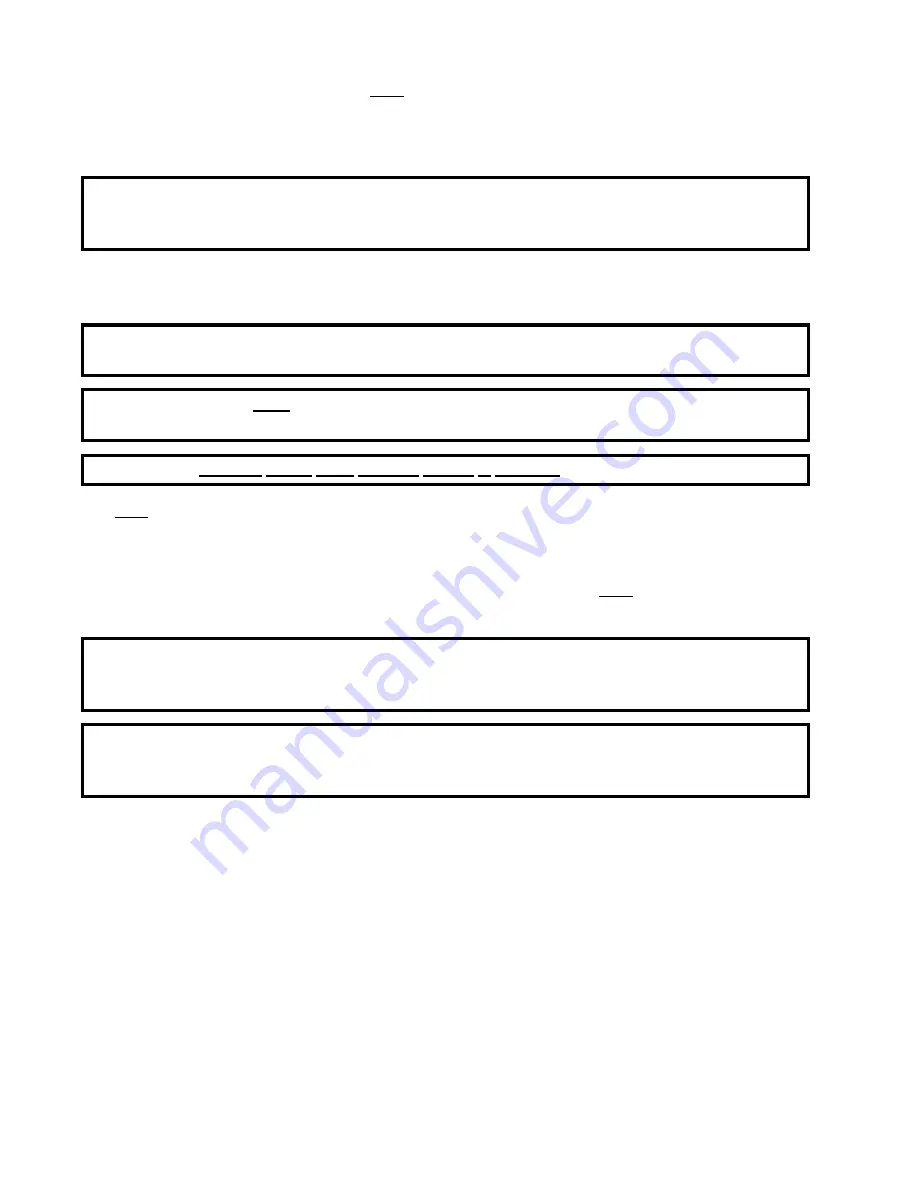
40
Consistent gas pressure is essential at
ALL
gas connections. It is recommended that a 2-inch (5.08 cm)
pipe gas loop be installed in the supply line serving a bank of dryers. An in-line pressure regulator
must be
installed in the gas supply line (header) if the (natural) gas pressure exceeds 12.0 inches of water column
(29.9 mb) pressure.
NOTE:
A water column test pressure of 3.5 inches (8.7 mb) for natural gas and 10.5 inches (26.1
mb) for L.P. (liquid propane) dryers is required at the gas valve pressure tap of each
dryer for proper and safe operation.
A 1/8-inch N.P.T. plugged tap, accessible for a test gauge connection,
must be
installed in the main gas
supply line immediately upstream of each dryer.
IMPORTANT:
Pipe joint compounds that resist the action of natural gas and L.P. gas
must be
used.
IMPORTANT:
Test
ALL
connections for leaks by brushing on a soapy water solution (liquid
detergent works well).
WARNING: NEVER
TEST
FOR
LEAKS
WITH
A
FLAME!!!
ALL
components/materials
must conform
to National Fuel Gas Code Specifications ANSI Z223.1-LATEST
EDITION, or in Canada, CAN/CGA-B149.1-M91 (Natural Gas) or CAN/CGA-B149.2-M91 (L.P. Gas) or
LATEST EDITION (for General Installation and Gas Plumbing), as well as local codes and ordinances and
must be
done by a qualified professional. It is important that gas pressure regulators meet applicable
pressure requirements, and that gas meters be rated for the total amount of
ALL
the appliance BTUs being
supplied.
IMPORTANT:
The dryer and its individual shut-off valve
must be
disconnected from the gas
supply piping system during any pressure testing of that system at test pressures
in excess of 1/2 psig (3.5 kPa).
NOTE:
The dryer
must be
isolated from the gas supply piping system by closing its individual
manual shut-off valve during any pressure test of the gas supply system at test pressures
equal to or less than 1/2 psig (3.5 kPa).
Summary of Contents for ML-410
Page 7: ...3 ML 410 Reference Guide ...
Page 8: ...4 ...
Page 28: ...24 MLG 410 1 Door Forward Tilt with Sprinkler ...
Page 31: ...27 MLS 410 2 Door 2 Way Tilt ...
Page 67: ...ADC 113128 1 03 13 00 25 ...