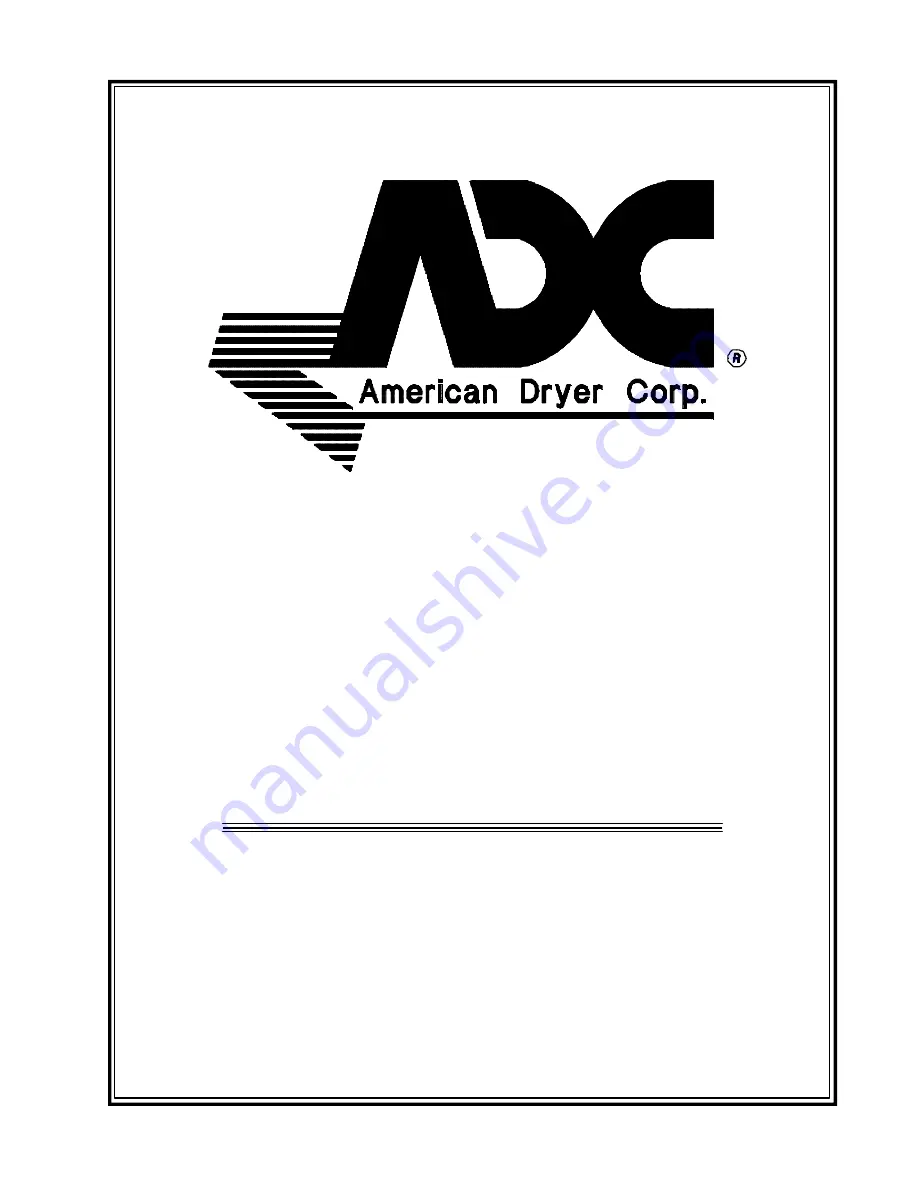
AD-758
Service Manual
052802ASILVA/mcronan
ADC
Part No. 450418
American Dryer Corporation
88 Currant Road
Fall River, MA 02720-4781
Telephone: (508) 678-9000 / Fax: (508) 678-9447
e-mail: [email protected]
www.amdry.com
Summary of Contents for AD-758
Page 61: ...ADC 450418 1 06 16 02 20 ...