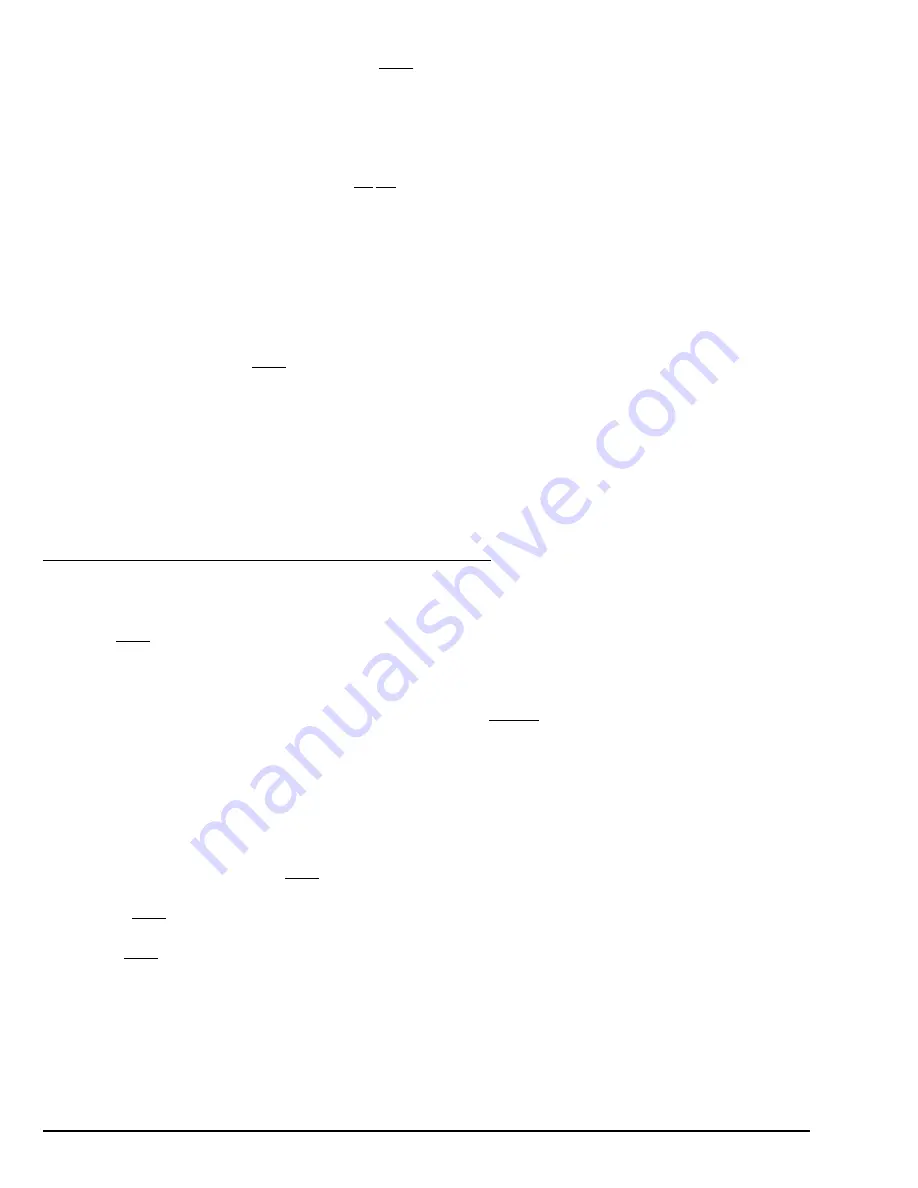
40
American Dryer Corporation
113549 - 8
2) Make a complete operational check of ALL safety related circuits (i.e., lint drawer switch and sail switch
on gas models).
3) Reversing tumbler dryers should never be operated with less than a 132 lb (59.9 kg) load (dry weight),
since the load’s weight affects tumbler coast time during a direction reversal command. It is important that
the tumbler come to a complete stop prior to starting in opposite direction. For automatic (mode) cycle
only, the spin and dwell (stop) times are not adjustable and have been preprogrammed into the microprocessor
controller (computer) for a 2-1/2 minute reverse spin time and a 7-second dwell (stop) time.
TUMBLER COATING
The tumbler is treated with a protective coating. We suggest dampening old garments or cloth material with a solution
of water and nonflammable mild detergent and tumbling them in the tumbler to remove this coating.
4) Each dryer should be operated through one (1) complete cycle to assure that no further adjustments are
necessary and that ALL components are functioning properly.
5) Microprocessor controller (computer) programs/selections...
a) Each microprocessor controller (computer) has been preprogrammed by the factory with the most
commonly used parameter (programs) selections. If computer program changes are required, refer to
the computer programming manual, which was shipped with the dryer.
K. PREPARATION FOR OPERATION/START-UP
The following items should be checked before attempting to operate the dryer:
1. Read ALL “CAUTION,” “WARNING,” and “DIRECTION” labels attached to the dryer.
2. Check incoming supply voltage to be sure that it is the same as indicated on the dryer data label affixed to the right
electrical control panel. In case of 208 VAC, for dryers with sprinkler option, verify single-phase (1ø) voltage is
correct. The supply voltage must match the electrical service exactly.
3. GAS MODELS – check to assure that the dryer is connected to the type of heat/gas indicated on the dryer data
label.
4. GAS MODELS – the sail switch damper assembly was installed and adjusted at the factory prior to shipping.
However, each sail switch adjustment must be checked to assure that this important safety control is functioning.
5. GAS MODELS – be sure that ALL gas shutoff valves are in the open position.
6. Be sure ALL side and base panels are on the dryer.
7. Check ALL service doors to assure that they are closed and secure.
8. Be sure lint drawer is securely in place.