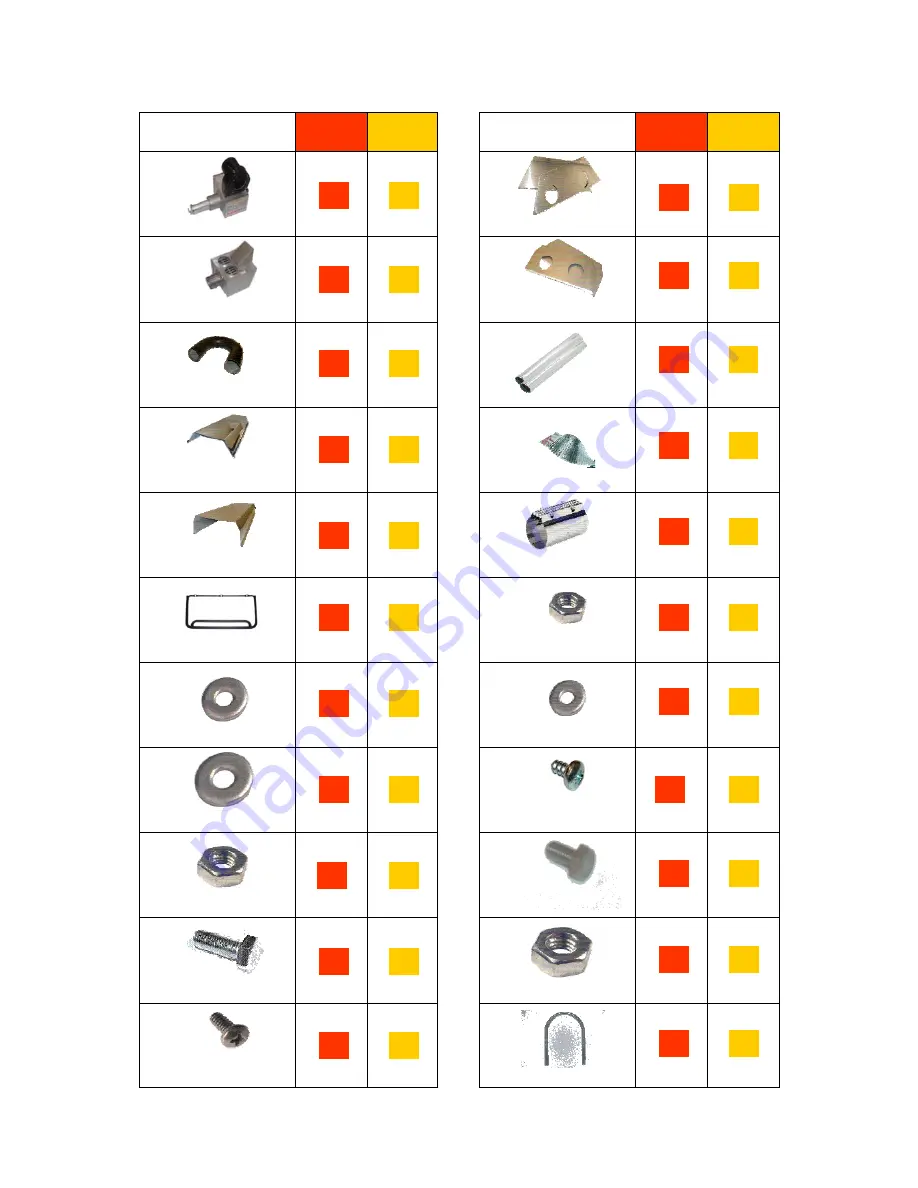
16
COLOUR CODE
VSX90
VSX140
U Bend
Inner
Reflectors
Outer
Canopy
Heat
Exchanger
1x
1x
1x
1x
COLOUR CODE
VSX90
VSX140
1x
1x
2x
3x
2x
3x
Inner
End Caps
Outer
Canopy
End Caps
Tubes
Turbulators
Couplers
2x
2x
2x
2x
2x
2x
2x
3x
2x
2x
Brackets
3x
4x
M4
Full Nut
1x
2x
Burner
M6
Mudwasher
M6
Washer
M6
Full Nut
M4 x 10
Pozi Setpin
No.5
Torque
Screw
M4
Washer
M6 x 15
Setpin
M8
Full Nut
M8 U Bolt
8
6
16
6
10
6
8
12
4
6
4
7
7
13
2
16
8
14
4
22
M6 x 35
Setpin
2.2 Identification check list