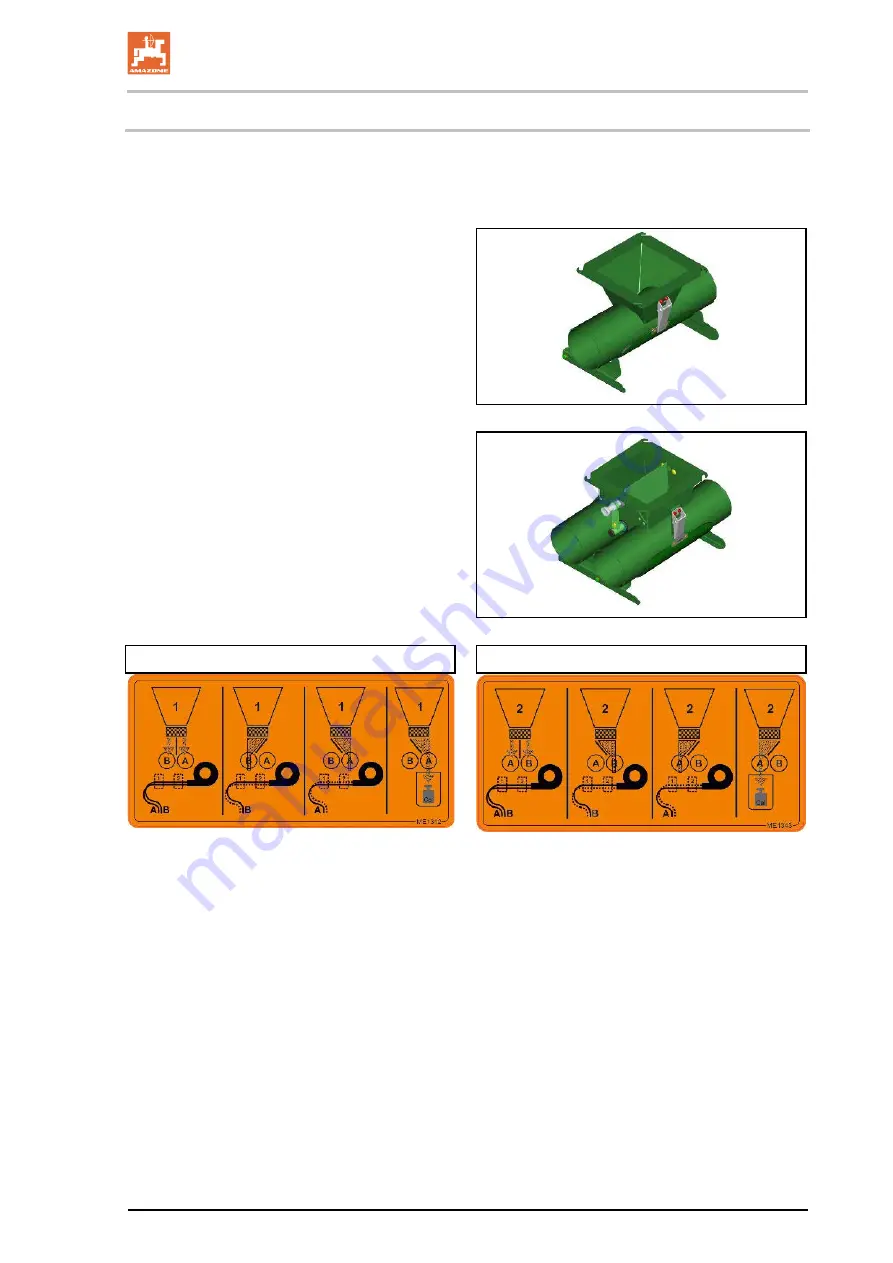
Layout and function
XTender BAG0158.2 03.18
45
5.3.3
Sluices
The sluices are equipped with a calibration flap
and a holder for the calibration sack. Mechanical
one-sided switching is possible with the double
sluice.
Single sluice on single conveyor section
Double sluice with setting flap and setting lever
on double conveyor section
Double sluice:
Hopper 1
Hopper 2
Depending on the position of the setting lever,
the respective double sluice coveys from hopper
1 and 2 in conveyor section A or / and B.
Select conveyor section A for calibration.