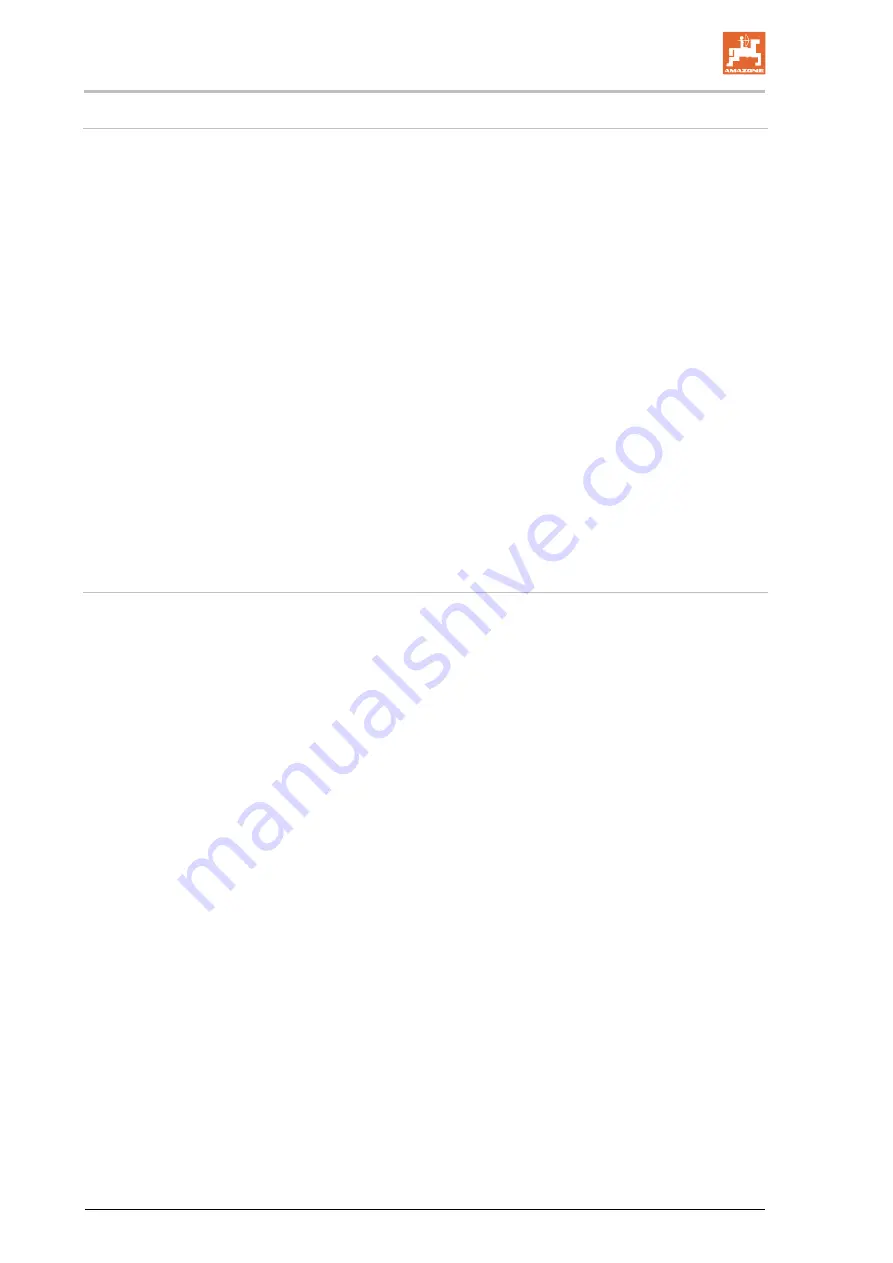
Foreword
4
Catros BAG0046.7 03.14
Foreword
Dear
Customer,
You have chosen one of the quality products from the wide product
range of AMAZONEN-WERKE, H. DREYER GmbH & Co. KG. We
thank you for your confidence in our products.
On receiving the implement, check to see if it was damaged during
transport or if there are any parts missing. Using the shipping
statement, check that the implement was delivered in full including
any special order equipment. Replacement will only be made if a
claim is filed immediately!
Please read and follow this operator’s manual—in particular, the
safety instructions—before operating the implement. Only after careful
reading of this manual, will you be able to benefit from the full scope
of your newly purchased implement and will be able to operate this
implement in a safe manner.
Please ensure that all implement operators have read this operator’s
manual before they operate this implement.
Should you have problems or questions, please consult this opera-
tor’s manual or give your Amazone dealer a call.
Regular maintenance and timely replacement of worn or damaged
parts increases the lifespan of your implement.
User evaluation
Dear
Reader,
We update our operator’s manuals regularly. Your suggestions for
improvement help us to create ever more user-friendly manuals. Send
us your suggestions by fax.
AMAZONEN-WERKE
H. DREYER GmbH & Co. KG
Postfach 51
D-49202 Hasbergen
Germany
Phone:
Fax:
E-mail:
+49 5405 501-0
+49 5405 501-234
Summary of Contents for CATROS 7501-2T
Page 111: ...Catros BAG0046 7 03 14 111 ...