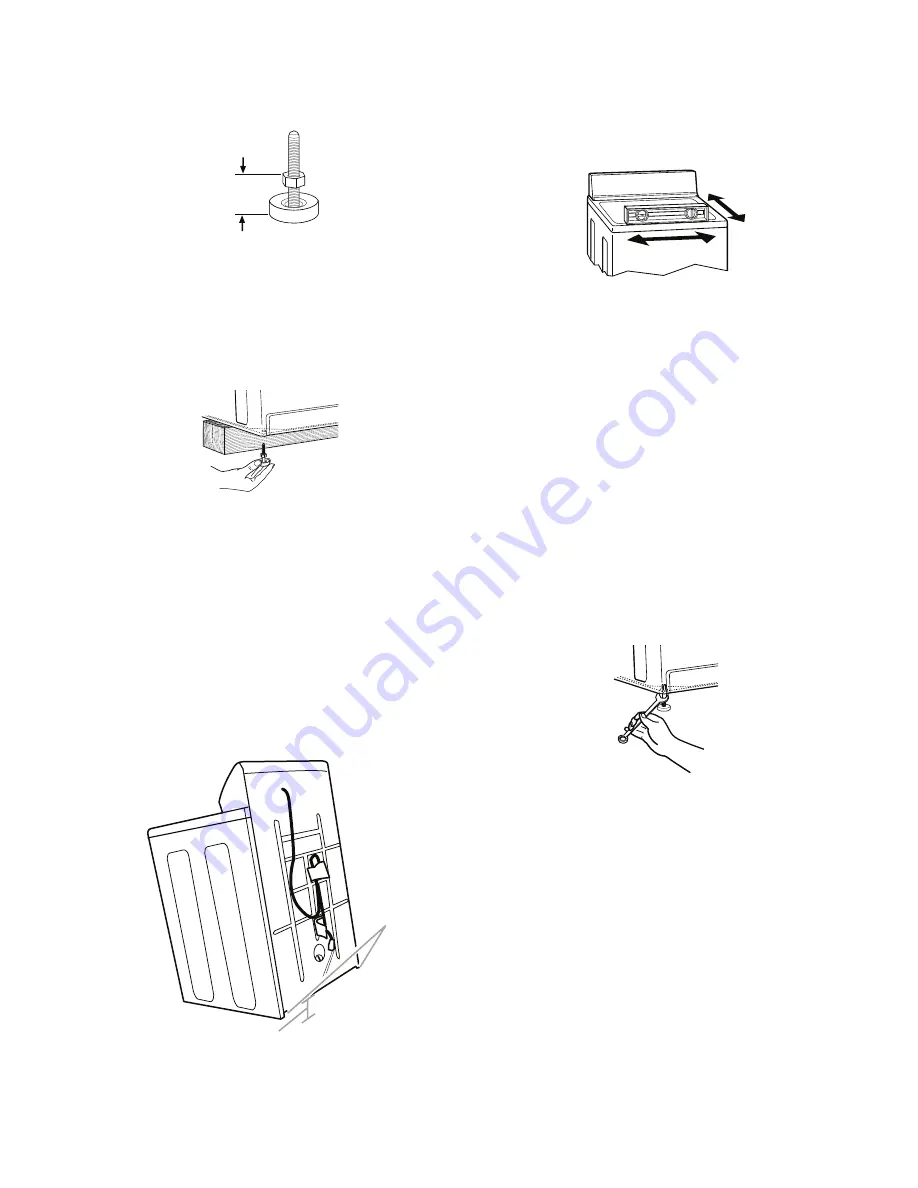
2-
3. Screw the feet into the threaded holes at
the front corner of the washer until the
nuts touch the washer. Twist the feet to
install.
NOTE:
Do not tighten the nuts until the
washer is level.
2. Screw the locknut onto each foot to within
1
˝
(2.5 cm) of the foot base.
"
1
2.5 cm)
(
4. Tilt the washer back and remove the
wood block. Gently lower the washer to
the floor.
Steps in final location
1. Slide the washer to its final location.
2. Tilt the washer forward until the rear of
the washer is at least 4
˝
(10.2 cm) off
the floor. You may hear the self-adjust
-
ing rear feet click into place. Lower the
washer to the floor.
3. Check the levelness of the washer by
placing a level on the top edges of the
washer, first side to side, then front to
back.
4. If the washer is not level, move the wash
-
er out slightly, tip back, prop up the front
of the washer with the wood block and
adjust the feet up or down as necessary
by twisting the feet. Turn the feet clock
-
wise to raise the washer or counterclock
-
wise to lower the washer. Repeat steps 1
through 4 until washer is level.
5. After the washer is in the final location
and level, use a 9/16
˝
or 14 mm open-
end wrench to turn the nuts counter
-
clockwise on the feet tightly against the
washer cabinet.
IMPORTANT:
If the nuts are not tight
against the washer cabinet, the washer
may vibrate.
A. Self-adjusting feet
A
4"
(10.2 cm)
Summary of Contents for NTW5400T
Page 4: ...iv NOTES...
Page 57: ...6 DIAGRAMS AND CHARTS WIRING DIAGRAM...
Page 58: ...6 TIMER SEQUENCE CHART...
Page 59: ...6 FUNCTION FUNCTION TIMER SEQUENCE CHART Cont d...
Page 60: ...6 CYCLE CHARTS Wash Action Switch Option Switch Soak Delay Temperature Switch...
Page 61: ...6 NOTES...
Page 62: ...6 NOTES...
Page 64: ......