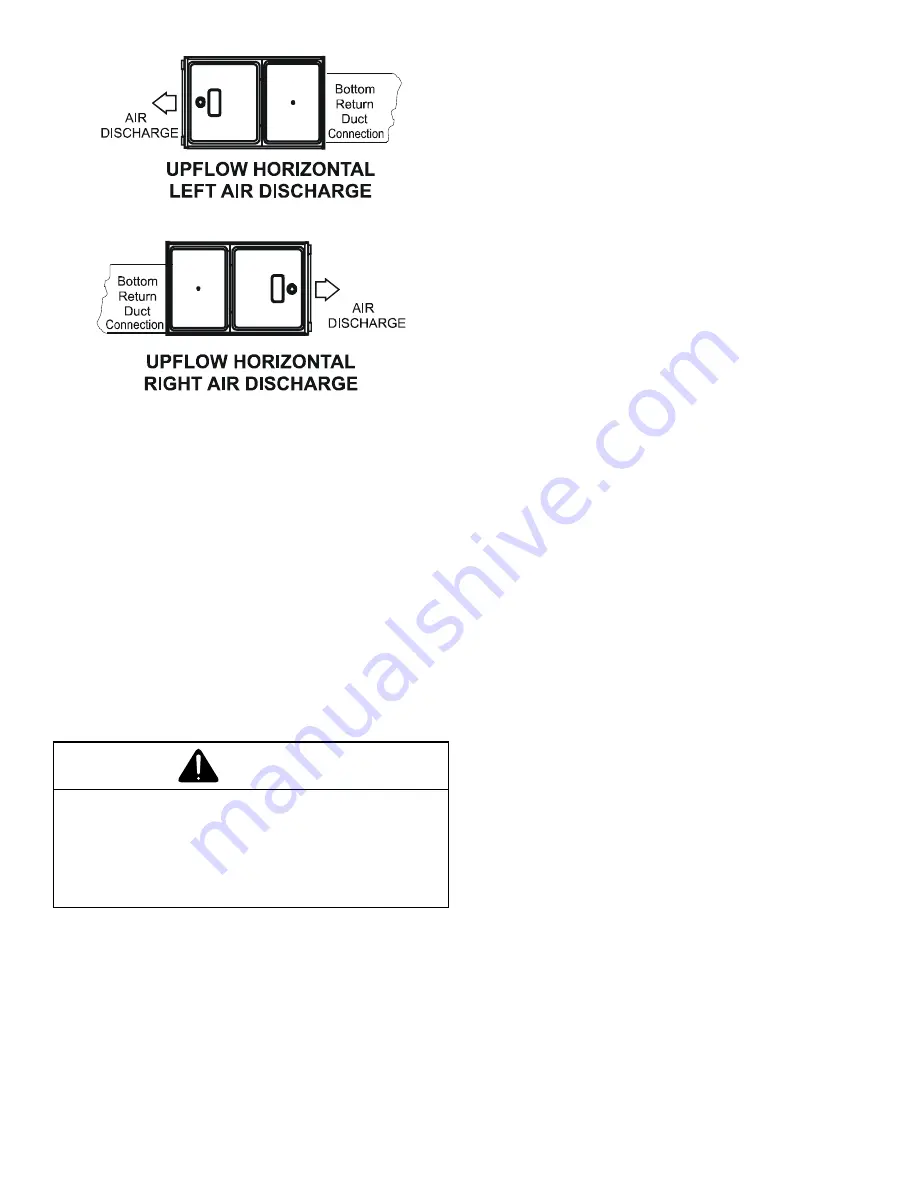
11
MATERIALS - INSTALLATIONS IN THE
U.S.A
PVC, CPVC, or ABS pipe & fittings are typically used as
venting and intake pipe materials. All 90° elbows must
be medium or long radius types. A medium radius elbow
should measure ~3-1/16” minimum from the plane of
one opening to the center line of the other opening for 2”
diameter pipe, and ~4-9/16” minimum for 3” pipe.
In addition to these materials, Innoflue® by Centrotherm
Eco Systems and PolyPro® by M&G Duravent are
also approved vent and combustion air materials for
installations in the U.S.A. Manufacturers Installation
instructions for these products must be followed. These
products have specific instructions for installing, joining
and terminating. Do not mix materials or components of
one manufacturer with materials or components of another
manufacturer. Refer to the following chart for plastic pipe &
fittings specifications
MATERIALS - INSTALLATIONS IN CANADA
All installations in Canada must conform to the
requirements of CAN/CSA B149.1-15 code. All vent
components, including primer and cement, must be listed
to ULC S636. The certified pipe and fittings should be
clearly marked with the ULC standard “S636”. The primer
and cement used must be of the same manufacturer as
the vent system. For Royal Pipe System 636; use GVS-
65 Primer (Purple) and GVS-65 PVC Solvent Cement.
For IPEX System 636, use PVC/CPVC Primer, Purple
or clear. Use PVC Solvent cement (Gray). For Canadian
installations, ABS may be used as a combustion air pipe
only. ABS is not an approved vent material in Canada.
If ABS is used as a combustion air pipe, it must be CSA
certified. Always follow the manufacturer’s instructions
in the use of primer and cement. Do not use primer and
cement around potential sources of ignition. Do not use
primer or cement beyond its expiration date.
Figure 3B
Recommended Installation Positions
Figure 3C
Alternate Electrical and Gas Line Connections
This furnace has provisions allowing for electrical and gas
line connectios through either side panel. In horizontal
applications the connections can be made either through
the “top”or “bottom” of the furnace.
Drain Pan
A drain pan must be provided if the furnace is installed
above a conditioned area. The drain pan must cover the
entire area under the furnace (and air conditioning coil if
applicable).
Freeze Protection
Refer to
Horizontal Applications and Conditions - Drain
Trap and Lines.
WARNING
Possible property damage, personal injury or
death may occur if the correct conversion kits
are not installed. The appropriate kits must
be applied to ensure safe and proper furnace
opearation. All conversions must be performed
by a qualified installer or service agency.
VENT PIPE & COMBUSTION AIR
This manual will refer to the pipe that discharges products
of combustion to the outdoors as the “vent” pipe or
“flue” pipe. The pipe that supplies air for combustion
to the furnace will be referred to as the “intake” pipe or
“combustion air” pipe.
This furnace is dual certified and may be installed as a
non-direct vent (single pipe) or direct vent (dual pipe)
appliance.