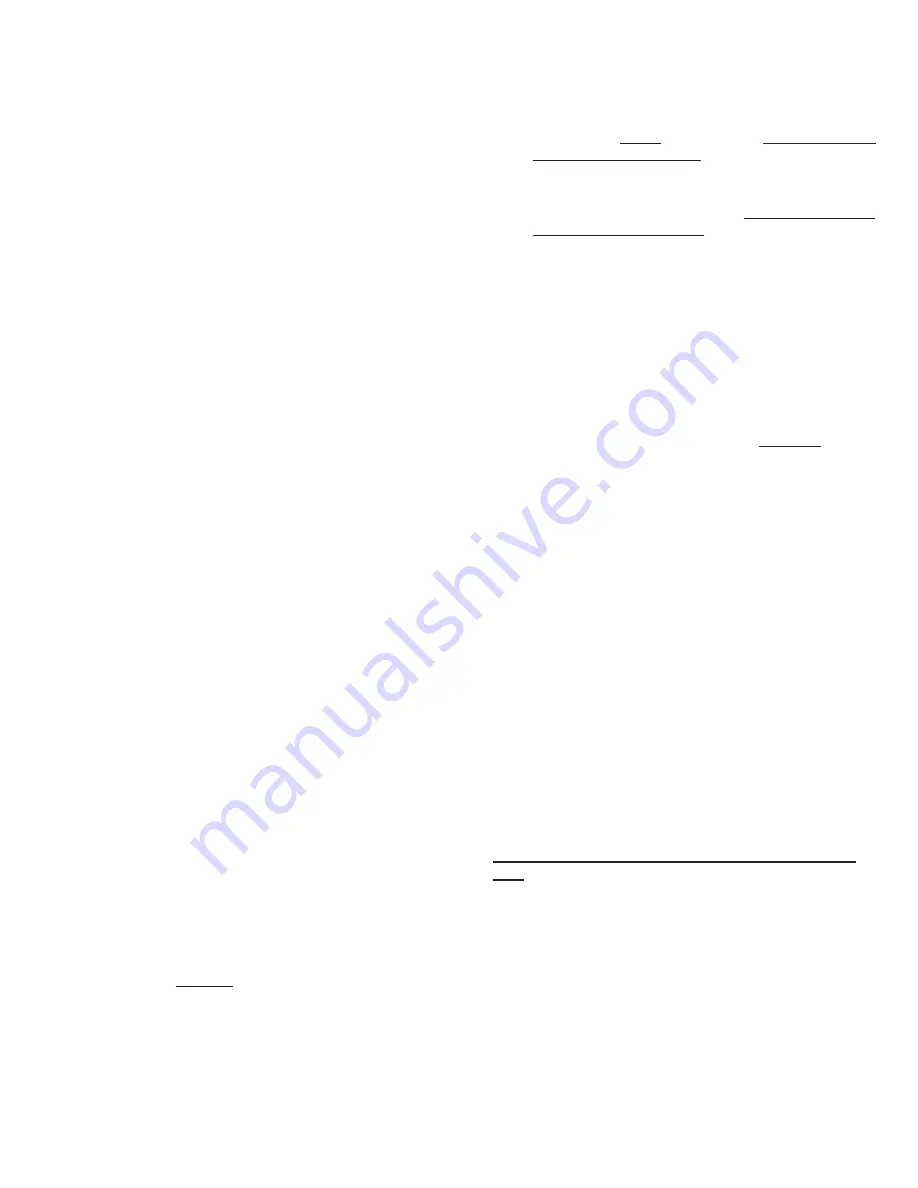
SERVICING
49
S-120 REFRIGERANT PIPING
The piping of a refrigeration system is very important in
relation to system capacity, proper oil return to compressor,
pumping rate of compressor and cooling performance of the
evaporator.
This long line set application guideline applies to all ARI listed
R22 air conditioner and heat pump split system matches of
nominal capacity 18,000 to 60,000 Btuh. This guideline will
cover installation requirements and additional accessories
needed for split system installations where the line set
exceeds 50 feet in actual length.
Additional Accessories:
1.
Crankcase Heater
- a long line set application can
critically increase the charge level needed for a system.
As a result, the system is very prone to refrigerant
migration during its off-cycle and a crankcase heater will
help minimize this risk. A crankcase heater is recom-
mended for any long line application (50 watt minimum).
2.
TXV Requirement:
All line set applications over 50 ft will
require a TXV.
3.
Hard Start Assist
- increased charge level in long line
applications can require extra work from the compressor
at start-up. A hard start assist device may be required to
overcome this.
4.
Liquid Line Solenoid
- A long line set application can
critically increase the charge level needed for a system.
As a result, the system is very prone to refrigerant
migration during its off-cycle and a liquid line solenoid will
help minimize this. A liquid line solenoid is recom-
mended for any long line application on straight cooling
units.
Tube Sizing:
1. In long line applications, the “equivalent line length” is the
sum of the straight length portions of the suction line plus
losses (in equivalent length) from 45 and 90 degree
bends.
Select the proper suction tube size based on
equivalent length of the suction line (see Tables 8 &
9) and recalculated system capacity.
Equivalent length = Length hori Length ve
Losses from bends (see Table 9)
2.
For any residential split system installed with a long
line set, the liquid line size must never exceed 3/8".
Limiting the liquid line size to 3/8" is critical since an
increased refrigerant charge level from having a larger
liquid line could possibly shorten a compressor’s lifespan.
3.
Single Stage Condensing Unit:
The maximum length
of tubing must not exceed 150 feet.
•
50 feet
is the maximum recommended vertical differ-
ence between the condenser and evaporator when the
evaporator is above the condenser. Equivalent length
is not to exceed 150 feet.
• The vertical difference between the condenser and
evaporator when the evaporator is below the condenser
can approach 150 feet, as long as the equivalent length
does not exceed 150 feet.
• The distance between the condenser and evaporator in
a completely horizontal installation in which the indoor
and outdoor unit do not differ more than 10 feet in
vertical distance from each other can approach 150
feet, as long as the equivalent length does not exceed
150 feet.
4.
Two-Stage Condensing Unit:
The maximum length of
tubing must not exceed 75 feet here indoor coil is located
above the outdoor unit.
NOTE: When the outdoor unit is located above the
indoor coil, the maximum vertical rise must not exceed
25 feet. If the maximum vertical rise exceeds 25 feet,
premature compressor failure will occur due to inad-
equate oil return.
5.
Vibration and Noise:
In long line applications, refriger-
ant tubing is highly prone to transmit noise and vibration
to the structure it is fastened to. Use adequate vibration-
isolating hardware when mounting line set to adjacent
structure.
Most refrigerant tubing kits are supplied with 3/8"-thick
insulation on the vapor line. For long line installations over
50 feet, especially if the line set passes through a high
ambient temperature, ½”-thick suction line insulation is
recommended to reduce loss of capacity. The liquid line
should be insulated if passing through an area of 120°F or
greater. Do not attach the liquid line to any non-insulated
portion of the suction line
Table 8 lists multiplier values to recalculate system-
cooling capacity as a function of a system’s equivalent
line length (as calculated from the suction line) and the
selected suction tube size. Table 2 lists the equivalent
length gained from adding bends to the suction line.
Properly size the suction line to minimize capacity
loss.