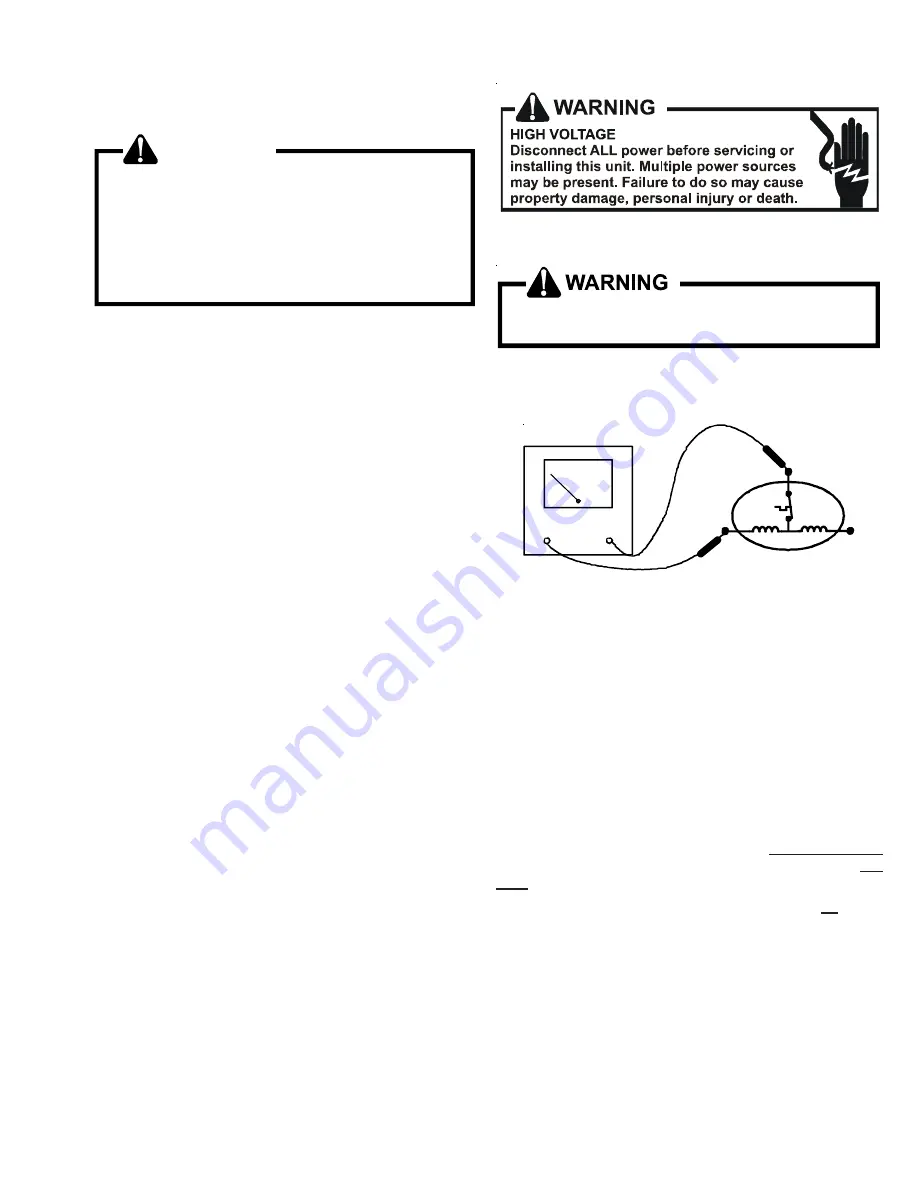
SERVICING
35
S-17 CHECKING COMPRESSOR
WARNING
Hermetic compressor electrical terminal venting can
be dangerous. When insulating material which
supports a hermetic compressor or electrical terminal
suddenly disintegrates due to physical abuse or as a
result of an electrical short between the terminal and
the compressor housing, the terminal may be
expelled, venting the vapor and liquid contents of the
compressor housing and system.
If the compressor terminal PROTECTIVE COVER and gas-
ket (if required) are not properly in place and secured, there
is a remote possibility if a terminal vents, that the vaporous
and liquid discharge can be ignited, spouting flames several
feet, causing potentially severe or fatal injury to anyone in its
path.
This discharge can be ignited external to the compressor if
the terminal cover is not properly in place and if the discharge
impinges on a sufficient heat source.
Ignition of the discharge can also occur at the venting
terminal or inside the compressor, if there is sufficient
contaminant air present in the system and an electrical arc
occurs as the terminal vents.
Ignition cannot occur at the venting terminal without the
presence of contaminant air, and cannot occur externally
from the venting terminal without the presence of an external
ignition source.
Therefore, proper evacuation of a hermetic system is
essential at the time of manufacture and during servicing.
To reduce the possibility of external ignition, all open flame,
electrical power, and other heat sources should be extin-
guished or turned off prior to servicing a system.
If the following test indicates shorted, grounded or open
windings, see procedures S-19 for the next steps to be taken.
S-17A RESISTANCE TEST
Each compressor is equipped with an internal overload.
The line break internal overload senses both motor amperage
and winding temperature. High motor temperature or amper-
age heats the disc causing it to open, breaking the common
circuit within the compressor on single phase units.
Heat generated within the compressor shell, usually due to
recycling of the motor, high amperage or insufficient gas to
cool the motor, is slow to dissipate. Allow at least three to
four hours for it to cool and reset, then retest.
Fuse, circuit breaker, ground fault protective device, etc. has
not tripped -
1. Remove the leads from the compressor terminals.
See warnings S-17 before removing compressor
terminal cover.
2. Using an ohmmeter, test continuity between terminals S-
R, C-R, and C-S, on single phase units or terminals T2,
T2 and T3, on 3 phase units.
S
R
C
COMP
OHMMETER
TESTING COMPRESSOR WINDINGS
If either winding does not test continuous, replace the
compressor.
NOTE:
If an open compressor is indicated, allow ample time
for the internal overload to reset before replacing compressor.
S-17B GROUND TEST
If fuse, circuit breaker, ground fault protective device, etc., has
tripped, this is a strong indication that an electrical problem
exists and must be found and corrected. The circuit protective
device rating must be checked, and its maximum rating
should coincide with that marked on the equipment name-
plate.
With the terminal protective cover in place, it is acceptable to
replace the fuse or reset the circuit breaker ONE TIME ONLY
to see if it was just a nuisance opening. If it opens again, DO
NOT continue to reset.
Disconnect all power to unit
, making sure that
all
power
legs are open.
1. DO NOT remove protective terminal cover. Disconnect
the three leads going to the compressor terminals at the
nearest point to the compressor.
2. Identify the leads and using a Megger, Hi-Potential Ground
Tester, or other suitable instrument which puts out a
voltage between 300 and 1500 volts, check for a ground
separately between each of the three leads and ground
(such as an unpainted tube on the compressor). Do not
use a low voltage output instrument such as a volt-
ohmmeter.