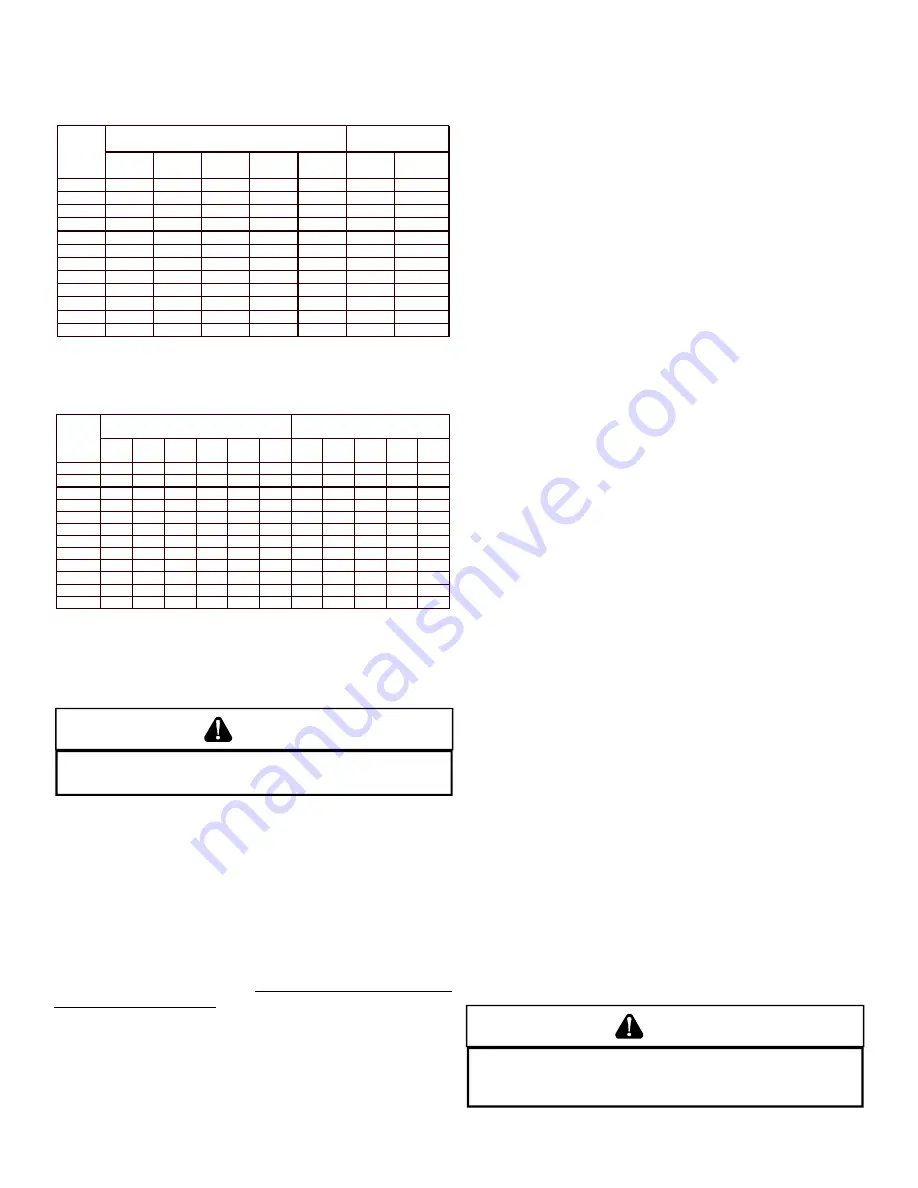
22
When the furnace is used in connection with a cooling unit, the
furnace should be installed in parallel with or on the upstream
side of the cooling unit to avoid condensation in the heating
element. With a parallel flow arrangement, the dampers or other
means used to control the flow of air must be adequate to prevent
chilled air from entering the furnace and, if manually operated,
must be equipped with means to prevent operation of either unit
unless the damper is in the full heat or cool position.
When the furnace is installed without a cooling coil, it is
recommended that a removable access panel be provided in the
outlet air duct. This opening shall be accessible when the furnace
is installed and shall be of such a size that the heat exchanger
can be viewed for visual light inspection or such that a sampling
probe can be inserted into the airstream. The access panel must
be made to prevent air leaks when the furnace is in operation.
When the furnace is heating, the temperature of the return air
entering the furnace must be between 55°F and 100°F.
When a furnace is installed so that supply ducts carry air circulated
by the furnace to areas outside the space containing the furnace,
the return air shall also be handled by a duct sealed to the furnace
casing and terminating outside the space containing the furnace.
F
ILTERS
- R
EAD
T
HIS
S
ECTION
B
EFORE
I
NSTALLING
T
HE
R
ETURN
A
IR
D
UCTWORK
Filters must be used with this furnace. Discuss filter maintenance
with the building owner. Filters do not ship with this furnace, but
must be provided by the installer. Filters must comply with UL900
or CAN/ULCS111 standards. If the furnace is installed without
filters, the warranty will be voided.
NOTE:
An undersized opening will cause reduced airflow.
For air delivery of less than 1800 CFM, use a one side or bottom
return. For air delivery of 1800 CFM or higher, use either two-
sided returns or a one-sided return with a bottom return. Refer to
Minimum Filter Area tables at the end of this manual to determine
filter area requirements.
U
PRIGHT
I
NSTALLATIONS
Depending on the installation and/or customer preference,
differing filter arrangements can be applied. Filters can be
installed in the central return register or a side panel external filter
rack kit (upflows), or the ductwork above a counterflow furnace. As
an alternative, a media air filter or electronic air cleaner can be
used as the requested filter. The following figures show possible
filter locations.
C
IRCULATION
A
IR
F
ILTERS
One of the most common causes of a problem in a forced air
heating system is a blocked or dirty filter. Circulating air filters
must be inspected monthly for dirt accumulation and replaced if
necessary. Failure to maintain clean filters can cause premature
heat exchanger failure.
A new home may require more frequent replacement until all
construction dust and dirt is removed. Circulating air filters are to
be installed in the return air duct external to the furnace cabinet.
WARNING
B
EFORE PERFORMING ANY SERVICE ON THIS FURANCE, DISCONNECT THE
MAIN POWER SUPPLY.
D
O NOT OPERATE THE FURNACE WITHOUT
CIRCULATIONG AIR FILTERS IN PLACE.
P
ROPANE
G
AS
P
IPING
C
HARTS
Sizing Between First and Second Stage Regulator*
Maximum Propane Capacities listed are based on 2 psig pressure drop at 10 psig setting.
Capacities in 1,000 BTU/hour.
Pipe or
Nominal Pipe Size
Tubing
Tubing Size, O.D. Type L
Schedule 40
Length,
3/8"
1/2"
5/8"
3/4"
7/8"
1/2"
3/4"
Feet
10
730
1,700
3,200
5,300
8,300
3,200
7,500
20
500
1,100
2,200
3,700
5,800
2,200
4,200
30
400
920
2,000
2,900
4,700
1,800
4,000
40
370
850
1,700
2,700
4,100
1,600
3,700
50
330
770
1,500
2,400
3,700
1,500
3,400
60
300
700
1,300
2,200
3,300
1,300
3,100
80
260
610
1,200
1,900
2,900
1,200
2,600
100
220
540
1,000
1,700
2,600
1,000
2,300
125
200
490
900
1,400
2,300
900
2,100
150
190
430
830
1,300
2,100
830
1,900
175
170
400
780
1,200
1,900
770
1,700
200
160
380
730
1,100
1,800
720
1,500
To convert to capacities at 15 psig settings - multiply by 1.130
To convert to capacities at 5 psig settings - multiply by 0.879
Sizing Between Single or Second Stage Regulator and Appliance*
Maximum Propane Capacities Listed are Based on 1/2" W.C. pressure drop at 11" W.C. setting.
Capacities in 1,000 BTU/hour.
Pipe or
Nominal Pipe Size
Tubing
Tubing Size, O.D. Type L
Schedule 40
Length,
3/8"
1/2"
5/8"
3/4"
7/8"
1-1/8"
1/2"
3/4"
1"
1-1/4" 1-1/2"
Feet
10
39
92
199
329
501
935
275
567
1,071
2,205
3,307
20
26
62
131
216
346
630
189
393
732
1,496
2,299
30
21
50
107
181
277
500
152
315
590
1,212
1,858
40
19
41
90
145
233
427
129
267
504
1,039
1,559
50
18
37
79
131
198
376
114
237
448
913
1,417
60
16
35
72
121
187
340
103
217
409
834
1,275
80
13
29
62
104
155
289
89
185
346
724
1,066
100
11
26
55
90
138
255
78
162
307
630
976
125
10
24
48
81
122
224
69
146
275
567
866
150
9
21
43
72
109
202
63
132
252
511
787
200
8
19
39
66
100
187
54
112
209
439
665
250
8
17
36
60
93
172
48
100
185
390
590
*Data in accordance with NFPA pamphlet NO. 54
X. CIRCULATING AIR AND FILTERS
D
UCTWORK
- A
IR
F
LOW
WARNING
N
EVER ALLOW THE PRODUCTS OF COMBUSTION, INCLUDING CARBON
MONOXIDE, TO ENTER THE RETURN DUCTWORK OR CIRCULATION AIR SUPPLY.
Duct systems and register sizes must be properly designed for
the CFM and external static pressure rating of the furnace.
Ductwork should be designed in accordance with the
recommended methods of “Air Conditioning Contractors of
America” Manual D.
A duct system must be installed in accordance with Standards of
the National Board of Fire Underwriters for the Installation of Air
Conditioning, Warm Air Heating and Ventilating Systems.
Pamphlets No. 90A and 90B.
A closed return duct system must be used, with the return duct
connected to the furnace.
NOTE:
Ductwork must never be attached
to the back of the furnace. Supply and return connections to the
furnace may be made with flexible joints to reduce noise
transmission. To prevent the blower from interfering with
combustion air or draft when a central return is used, a connecting
duct must be installed between the unit and the utility room wall. A
room, closet, or alcove must not be used as a return air chamber.