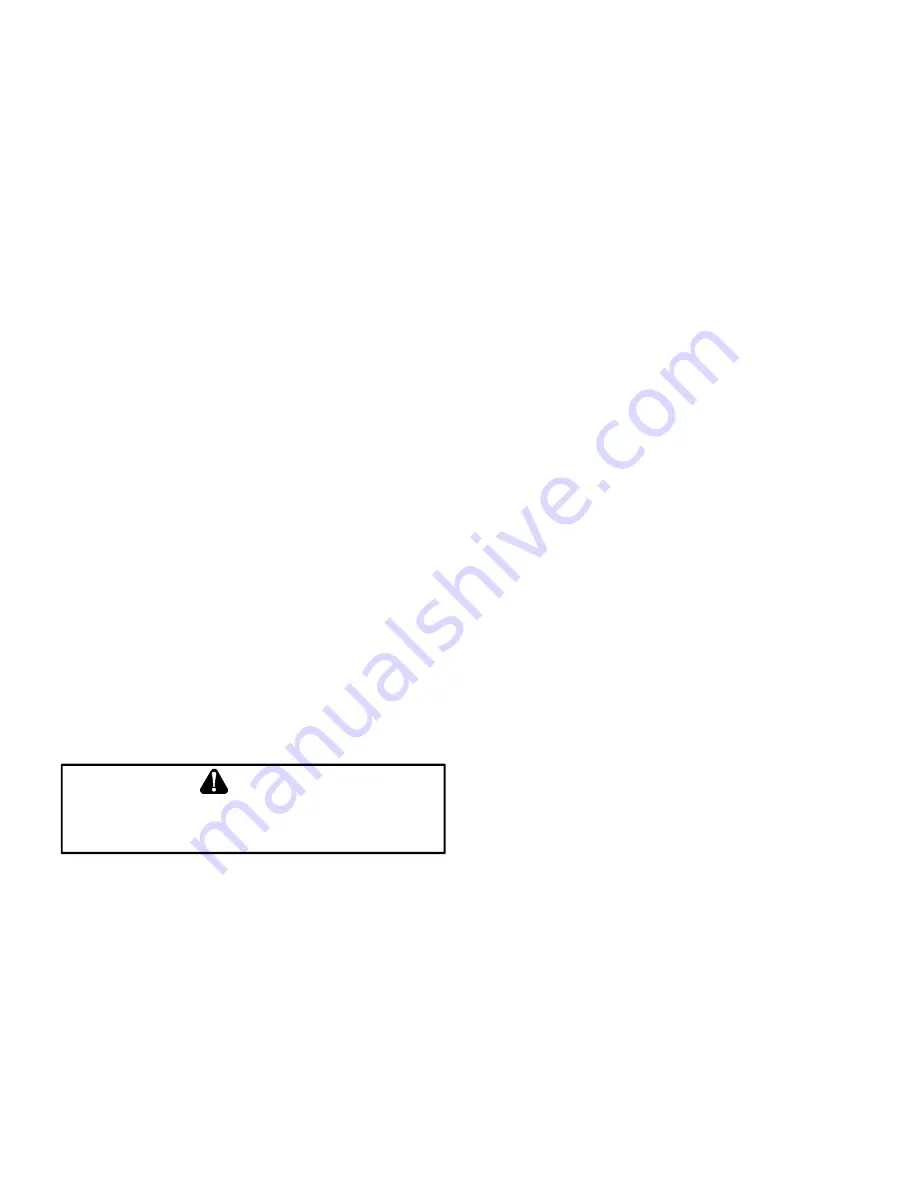
5
E
LECTROSTATIC
D
ISCHARGE
(ESD) P
RECAUTIONS
NOTE:
Discharge body’s static electricity before touching unit. An
electrostatic discharge can adversely affect electrical components.
Use the following precautions during furnace installation and ser-
vicing to protect the integrated control module from damage. By
putting the furnace, the control, and the person at the same elec-
trostatic potential, these steps will help avoid exposing the inte-
grated control module to electrostatic discharge. This procedure
is applicable to both installed and non-installed (ungrounded)
furnaces.
1. Disconnect all power to the furnace. Do not touch the
integrated control module or any wire connected to the
control prior to discharging your body’s electrostatic
charge to ground.
2. Firmly touch a clean, unpainted, metal surface of the
furnaces near the control. Any tools held in a person’s
hand during grounding will be discharged.
3. Service integrated control module or connecting wiring
following the discharge process in step 2. Use caution not
to recharge your body with static electricity; (i.e., do not
move or shuffle your feet, do not touch ungrounded objects,
etc.). If you come in contact with an ungrounded object,
repeat step 2 before touching control or wires.
4. Discharge your body to ground before removing a new
control from its container. Follow steps 1 through 3 if
installing the control on a furnace. Return any old or new
controls to their containers before touching any ungrounded
object.
T
O
T
HE
I
NSTALLER
Before installing this unit, please read this manual thoroughly to
familiarize yourself with specific items which must be adhered to,
including but not limited to: unit maximum external static pres-
sure, gas pressures, BTU input rating, proper electrical connec-
tions, circulating air temperature rise, minimum or maximum CFM,
and motor speed connections, and venting. These furnaces are
designed for Category I venting only.
T
O
PREVENT
PROPERTY
DAMAGE
,
PERSONAL
INJURY
OR
DEATH
DUE
TO
FIRE
,
DO
NOT
INSTALL
THIS
FURNACE
IN
A
MOBILE
HOME
,
TRAILER
,
OR
RECREATIONAL
VEHICLE
.
WARNING
P
RODUCT
A
PPLICATION
This furnace is primarily designed for residential home-heating
applications. It is NOT designed or certified for use in mobile
homes, trailers or recreational vehicles. Neither is it designed or
certified for outdoor applications. The furnace
must
be installed
indoors (i.e., attic space, crawl space, or garage area provided the
garage area is enclosed with an operating door).
This furnace can be used in the following non-industrial commer-
cial applications:
Schools, Office buildings, Churches, Retail stores,
Nursing homes, Hotels/motels, Common or office areas
In such applications , the furnace must be installed with the fol-
lowing stipulations:
•
It must be installed per the installation instructions
provided and per local and national codes.
•
It must be installed indoors in a building constructed on
site.
•
It must be part of a ducted system and not used in a free
air delivery application.
•
It must not be used as a “make-up” air unit.
•
All other warranty exclusions and restrictions apply.
This furnace may be used as a construction site heater
ONLY
if the
following conditions are met:
•
The vent system is permanently installed per these
installation instructions.
•
A room thermostat is used to control the furnace. Fixed
jumpers that provide continuous heating CANNOT be used
and can cause long term equipment damage. Bi-metal
thermostats, or any thermostat affected by vibration must
not be used during construction.
•
Return air ducts are provided and sealed to the furnace.
•
A return air temperature range between 60ºF (16ºC) and
80ºF (27ºC) is maintained.
•
Air filters are installed in the system and replaced daily
during construction and upon completion of
construction.
•
The input rate and temperature rise are set per the furnace
rating plate.
•
100% outside air must be used for combustion during
construction. Temporary ducting may be used to supply
outside air to the furnace for combustion – do not connect
this duct directly to the furnace. Size this duct according
to NFPA 54/ANSI Z223.1 section for Combustion and
Ventilation Air.
•
The furnace heat exchanger, components, duct system,
air filters and evaporator coils are thoroughly cleaned
following final construction clean up by a qualified
person.
•
All furnace operating conditions (including ignition,
input rate, temperature rise and venting) are verified by
a qualified person according to these installation
instructions.
•
Furnace doors must be in place on the furnace while the
furnace is operating in any mode.
Damage or repairs due to failure to comply with these require-
ments are not covered under the warranty
.
NOTE:
The Commonwealth of Massachusetts requires that the
following additional requirements must also be met:
•
Gas furnaces must be installed by a licensed plumber or
gas fitter.
•
A T-handle gas cock must be used.
•
If the unit is to be installed in an attic, the passageway to
and the service area around the unit must have flooring.