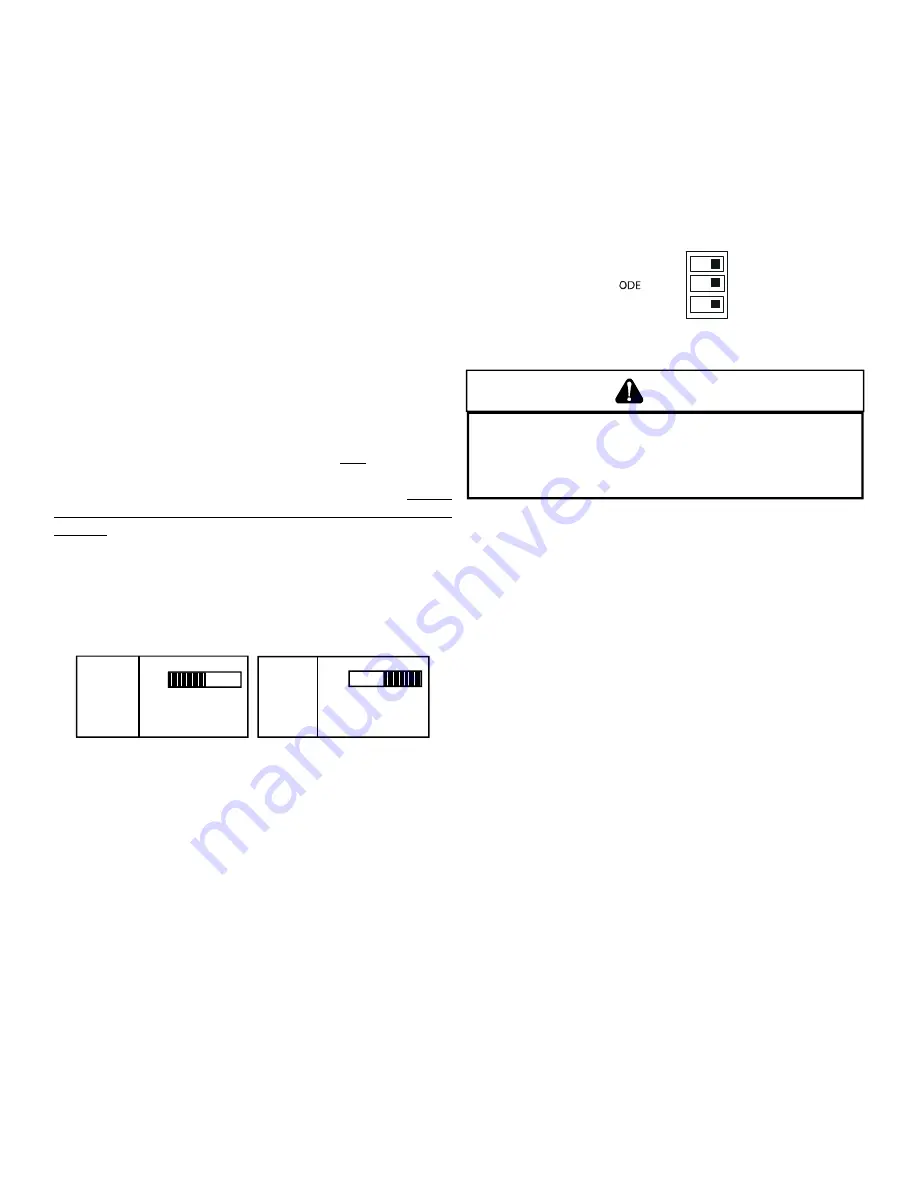
28
2. Select the heating and cooling blower speeds that match
the installation requirements from the airflow table in the
Specification Sheet applicable to your model. (Please
contact your distributor or our website for the applicable
Specification Sheet referred to in this manual.)
3. Relocate desired motor leads to the circulator blower heat
and cool speed terminals on the integrated control module.
(Terminals are identified as LO HEAT, HI HEAT and COOL
(hot)) for *(M,D)H8 / ADSH8, GME8 & AMEH8 models and
HEAT and COOL for *(M,H,D)S8 / ADSS8 models). If a heating
speed and the cooling speed are the same, a jumper wire
must be used between the heat and cool terminals.
4. Connect all unused blower motor leads to the “PARK”
terminals on the integrated control module. Any leads not
connected to the “PARK” terminals must be taped.
5. Turn ON power to furnace.
6. Verify proper temperature rise as outlined in
Temperature
Rise section
.
C
IRCULATOR
B
LOWER
F
AN
T
IMING
A
DJUSTMENT
NOTE:
Items in this section refer to the
air circulator blower fan
in
the *(M,D)H8 / ADSH8, GME8 & AMEH8 models, NOT to the induced
draft blower. The induced draft blower timing sequence is not
adjustable. The circulator blower fan timing is adjustable only on
models with optional “heating fan OFF delay” adjustment pins or
switches. It is NOT adjustable in any other circumstances.
As shipped, the circulator blower fan will remain on for 150 sec-
onds after the gas valve closes. When a call for cooling occurs,
the circulator fan comes on and remains on for 45 seconds after
the call for cooling ends. During normal heating operation, the
circulator fan will come on approximately 34 seconds after the
gas valve opens.
O
N
O
F
F
O
N
O
F
F
1
150
SECOND
DELAY
100
SECOND
DELAY
1
Switch viewed in an upflow installation.
Adjustment Switch
S
ETTING
F
URNACE
O
PERATING
M
ODE
(GDH8, GME8, *MH8,
AMEH8
AND
ADSH8
MODELS
ONLY
)
This furnace is designed to operate with either a single gas input
rate or with two discrete gas input rates. The Mode DIP switch
is used to select the single gas input rate or two discrete input
rates.
Setting the Mode switch to “1 STG” forces the furnace to operate
at the furnace’s highest input rate only. Operation is as de-
scribed under
Sequence of Operation (Integrated Ignition Control)
– Mode DIP Switch is set to “1 STG” position
.
Setting the Mode switch to “2 STG” allows the furnace to operate
at the furnace’s highest input AND at an input rate that is 75% of
the highest input rate. For this mode of operation, the furnace
operates at the low input rate for a pre-determined time period
then steps to the high input rate. Operation is as described
under
Sequence of Operation (Integrated Ignition Control) – Mode
DIP Switch is set to “2 STG” position
.
The time period is determined by the 2
nd
Stg Dly DIP switch.
Setting the 2
nd
Stg Dly DIP switch to 5 minutes fixes the delay
period at 5 minutes. Setting the 2
nd
Stg Dly DIP switch to Auto
enables an algorithm that calculates a delay period based on
the heating cycle time and the total cycle time. The delay period
can range from 1 minute to 12 minutes.
5 MIN
OFF
ON
1 STG
AUTO
2 STG
M
2
ND
STG DLY
O
PERATIONAL
C
HECKS
WARNING
T
O AVOID PERSONAL INJURY OR DEATH, DO NOT REMOVE ANY INTERNAL
COMPARTMENT COVERS OR ATTEMPT ANY ADJUSTMENT.
E
LECTRICAL
COMPONENTS ARE CONTAINED IN BOTH COMPARTMENTS.
C
ONTACT A
QUALIFIED SERVICE AGENT AT ONCE IF AN ABNORMAL FLAME APPEARANCE
SHOULD DEVELOP.
C
HECKING
D
UCT
S
TATIC
Refer to your furnace rating plate for the maximum ESP (external
duct static) rating.
Total external static refers to everything external to the furnace
cabinet. Cooling coils, filters, ducts, grilles, registers must all be
considered when reading your total external static pressure. The
supply duct pressure must be read between the furnace and the
cooling coil. This reading is usually taken by removing the “A”
shaped block off plate from the end on the coil; drilling a test hole
in it and reinstalling the block off plate. Take a duct static reading
at the test hole. Tape up the test hole after your test is complete.
The negative pressure must be read between the filter and the
furnace blower.
Too much external static pressure will result in insufficient air
that can cause excessive temperature rise. This can cause limit
switch tripping and heat exchanger failure.
To determine total external duct static pressure, proceed as fol-
lows;
1. With clean filters in the furnace, use a draft gauge (inclined
manometer) to measure the static pressure of the return
duct at the inlet of the furnace. (Negative Pressure)
2. Measure the static pressure of the supply duct. (Positive
Pressure)
3. The difference between the two numbers is .4” w.c.
Example:
static reading from return duct = -.1" w.c.
static reading from supply duct = .3" w.c.
total external static pressure on this system = .4" w.c.