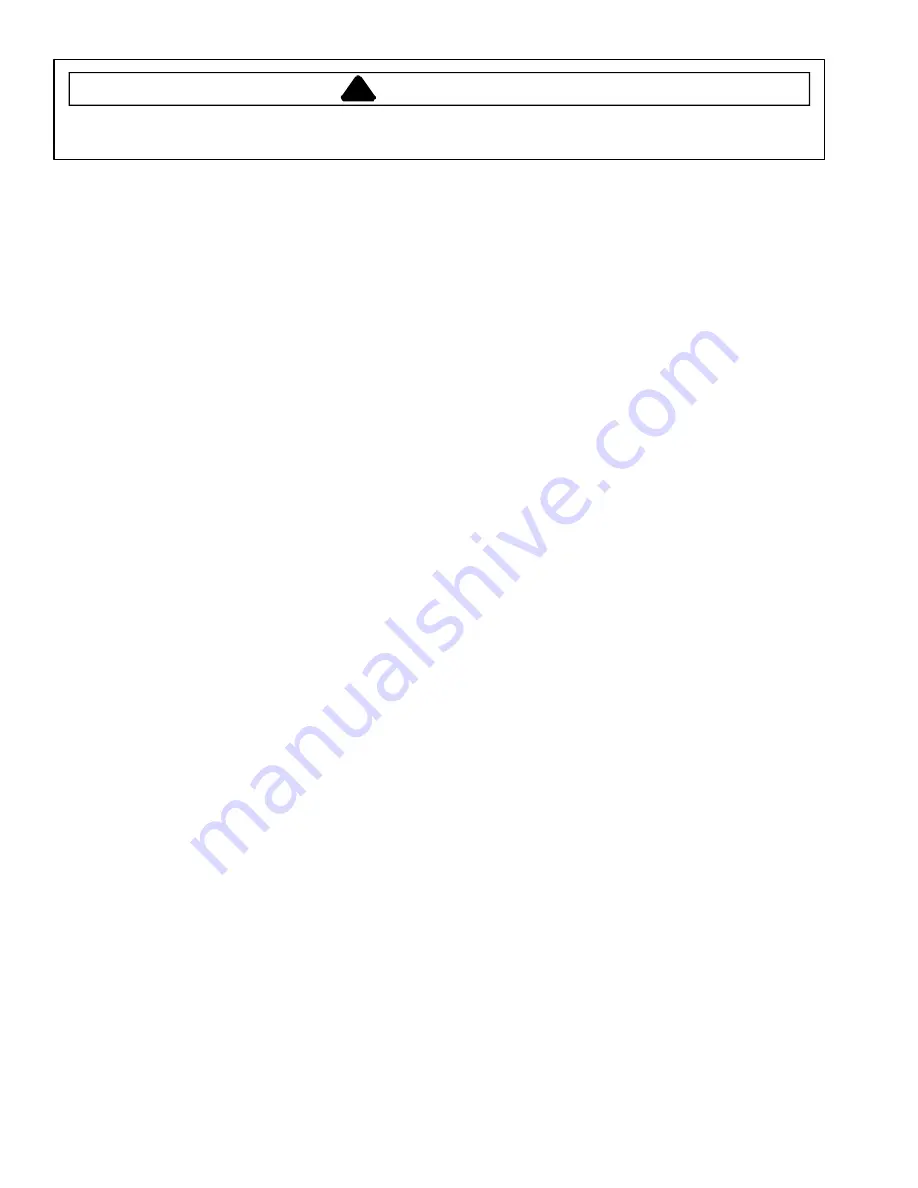
RS1300005 Rev. 0
4
Product Design
To avoid risk of electrical shock, personal injury, or death, disconnect electrical power source to unit, unless test
procedures require power to be connected. Discharge capacitor through a resistor before attempting to service.
Ensure all ground wires are connected before certifying unit as repaired and/or operational.
!
WARNING
Refrigeration System
Compressor forces high temperature vapor into fan
cooled tube and wire condenser where vapor is cooled
and condensed into high pressure liquid by circulation
of air across condenser coil. (See Refrigerant Flow
Diagram, page 18)
High pressure liquid passes into post-condenser loop
which helps to prevent condensation around freezer
compartment opening and through molecular sieve
drier and into capillary tube. Small inside diameter of
capillary offers resistance, decreasing pressure, and
temperature of liquid discharged into evaporator.
Capillary diameter and length is carefully sized for
each system.
Capillary enters evaporator at top back. Combined
liquid and saturated gas flows through back to bottom
of coil and into suction line. Aluminium tube evaporator
coil is located in freezer compartment where
circulating evaporator fan moves air through coil and
into fresh food compartment.
Large surface of evaporator allows heat to be
absorbed from both fresh food and freezer
compartments by airflow over evaporator coil causing
some of the liquid to evaporate. Temperature of
evaporator tubing near end of running cycle may vary
from -13° to -25°F.
Saturated gas is drawn off through suction line where
superheated gas enters compressor. To raise
temperature of gas, suction line is placed in heat
exchange with capillary.
Temperature Controls
Freezer compartment temperature is regulated by air
sensing thermostat at rear back of fresh food
compartment which actuates compressor. Control
capillary is inserted in well which routes capillary into
freezer. Control should be set to maintain freezer
temperature between 0° to -2°F.
Fresh food compartment temperature is regulated an
air damper control governing amount of refrigerated
air entering fresh food compartment from freezer.
Fresh food compartment temperature should be
between 38° and 40°F.
Defrost Timer System (some models)
Every 8 hours of compressor run time defrost timer
activates radiant electric defrost heater suspended
from evaporator. After 33 minutes of defrost cycle
time, timer restores circuit to compressor.
Defrost terminator (thermostat) is wired in series with
defrost heater. Terminator opens and breaks circuit
when preset high temperature is reached. After
defrost thermostat opens, thermostat remains open
until end of defrost cycle when cooling cycle starts and
terminator senses present low temperature and
closes.
Defrost heater is suspended on left side of evaporator
coil and across bottom to keep defrost drain free
flowing during defrost. Defrost water is caught in
trough under evaporator coil and flows through drain
hole in liner and drain tubing into drain pan. Air
circulated by condenser fan over pan evaporates
water.
Adaptive Defrost System (some models)
The ADC adapts the compressor run time between
defrosts to achieve optimum defrost intervals by
monitoring the cold control and length the defrost
heater is on.
Summary of Contents for 22 Cu. Ft
Page 48: ...1 A RS1300005 Rev 0 Appendix A...
Page 72: ......