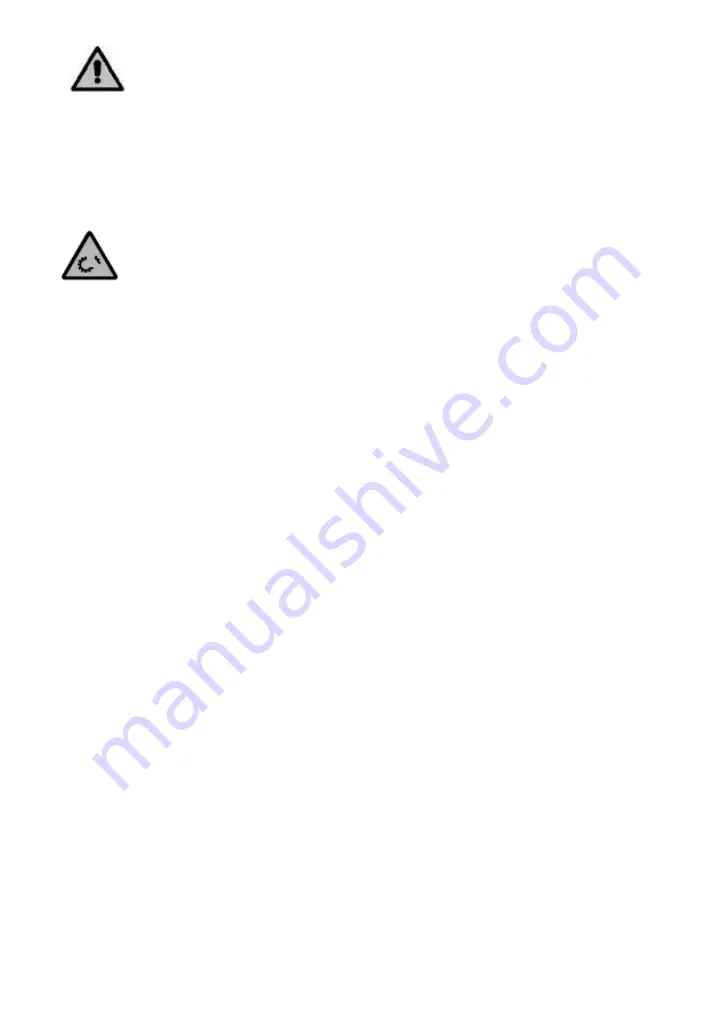
Monitor the concentration of cleaning solutions, it could give rise to the deterioration of the
pump sealing gaskets.
In order to remove any remains of cleaning products, ALWAYS rinse the element in question with clean water after
completing the cleaning process.
7.3.2. Automatic SIP [sterilization-in-place)
The process of sterilization with steam is applied to all the equipment including the pump.
Do NOT start the pump during the process of sterilization with steam. The parts/materials
suffer no damage if the indications specified in this manual are observed,
No cold liquid can enter the pump till the temperature of the pump is lower than 60°C (140°F).
A flow by-pass is recommended to be used in order to assure the flow of sterile product after
the pump.
Maximum conditions during the SIP process with steam or overheated water
a.
Max temperature : 140C
b.
Max time : 30 min
c.
Colling : sterile air inert gas
d.
Materials : EPDM (RECOMMENEND) - NBR NOT RECOMMEND
7.4 DISMANTLING / ASSEMBLY
Before Dismantling, Isolate Electrical Circuits; Close Isolation Valve On The Suction And Discharge To The Pumps
For Prevention Of Liquid Escaping Form The Pipe line System.
7.4.1 Stator removal
Unscrew the four domed nuts (50) fitted with end cover (12), end of the rods (27) and remove the end cover.
Unscrew the tie rod from the pump housing and withdraw the middle support (17), if provided. To unscrew the
stator form the rotor (19), hold the stator stationary and rotate the pump coupling /pulley , or hold the coupling
stationary and rotate the stator , whichever is easier. If the stator offers some resistance , pour little water through
the opening to ease the stiffness.
7.4.2 Rotor & universal joint assembly
Open the four domed nuts (41) and withdraw the pump housing. Slip out the boot seal retainer (26) & slip back the
Pin Retainer Sleeve (24) over the boot seal (33) and slide it over the augur coupling rod (20) from the rotor end.
Knock out the coupling rod pin (21). withdraw the rotor and remove the
Ό
' ring (32). Execute the same operation at
the end of the coupling rod and withdraw the coupling rod from the shaft head.
7.4.3 Bracket
a. Knock out the spring dowel pin (36) from the pump shaft (18) and withdraw the geared motor shaft (65).
b. Pump shaft along with stuffing box assembly or mechanical seal housing assembly, and water thrower (63), will
come out of the bracket (10). Remove all the components from the shaft.
CLEAN ALL THE PARTS REMOVED. REPLACE THE WORN OUT PARTS WITH ORIGINAL
ALPHADYNAMIC PUMPS Co.
7.4.4 Universal joint
Universal joints are to be lubricated with wheel bearing grease. (Soda base grease with medium fiber structure)
7.4.5 Pump housing assembly
While assembling the pump housing, care must be taken so that the pump Housing does not rub against the rotor
or the coupling rod as the scratches may substantially reduce the life of the Rotor / Coupling Rod. Also ensure that
the rotor is supported at a comfortable height and is not left freely hanging during assembly.
-14-
Summary of Contents for ATLAS C Series
Page 1: ...Installation OperationandMaintenance E ProgressiveCavityPumps K ATLAS...
Page 4: ......
Page 21: ...1 1 1 Atlas S 1 2 1 3 1 3 1 1 4 21...
Page 22: ...1 4 1 O 8 1 4 2 T 8 standard IP 55 1 4 3 K 8 1 4 4 1 4 5 ATLAS S C W O 22...
Page 23: ...3 3 1 ATLAS S ALPHADYNAMIC Co 3 2 a b c 4 4 1 ALPHADYNAMIC Co CE 4 1 1 23...
Page 24: ...4 2 ATLAS S 4 3 4 4 4 5 24...
Page 25: ...4 6 4 7 O 3 4 2 1 2 U 4 8 4 9 25...
Page 26: ...5 4 5 1 8 ALPHADYNAMIC Co 5 1 1 5 1 2 5 2 BY PASS by pass by pass by pass 6 bar 26...
Page 33: ...1 1 1 Atlas S 1 2 1 3 1 3 1 1 4 1 4 1 8 33...
Page 34: ...1 4 2 8 IP 55 1 4 3 8 1 4 4 1 4 5 ATLAS S C W 34...
Page 35: ...3 3 1 t ATLAS S C W ALPHADYNAMIC PUMPS Co 3 2 a b c 4 4 1 ALPHADYNAMIC PUMPS Co 35...
Page 36: ...4 1 1 4 2 ATLAS S C W 4 3 8 4 4 4 5 36...
Page 37: ...4 6 4 7 3 4 2 1 2 U 4 8 4 9 37...
Page 38: ...5 4 5 1 8 ALPHADYNAMIC Co 5 1 1 5 1 2 5 2 6 38...
Page 43: ...NOTES...
Page 44: ...ATLAS ProgressiveCavityPumps K...