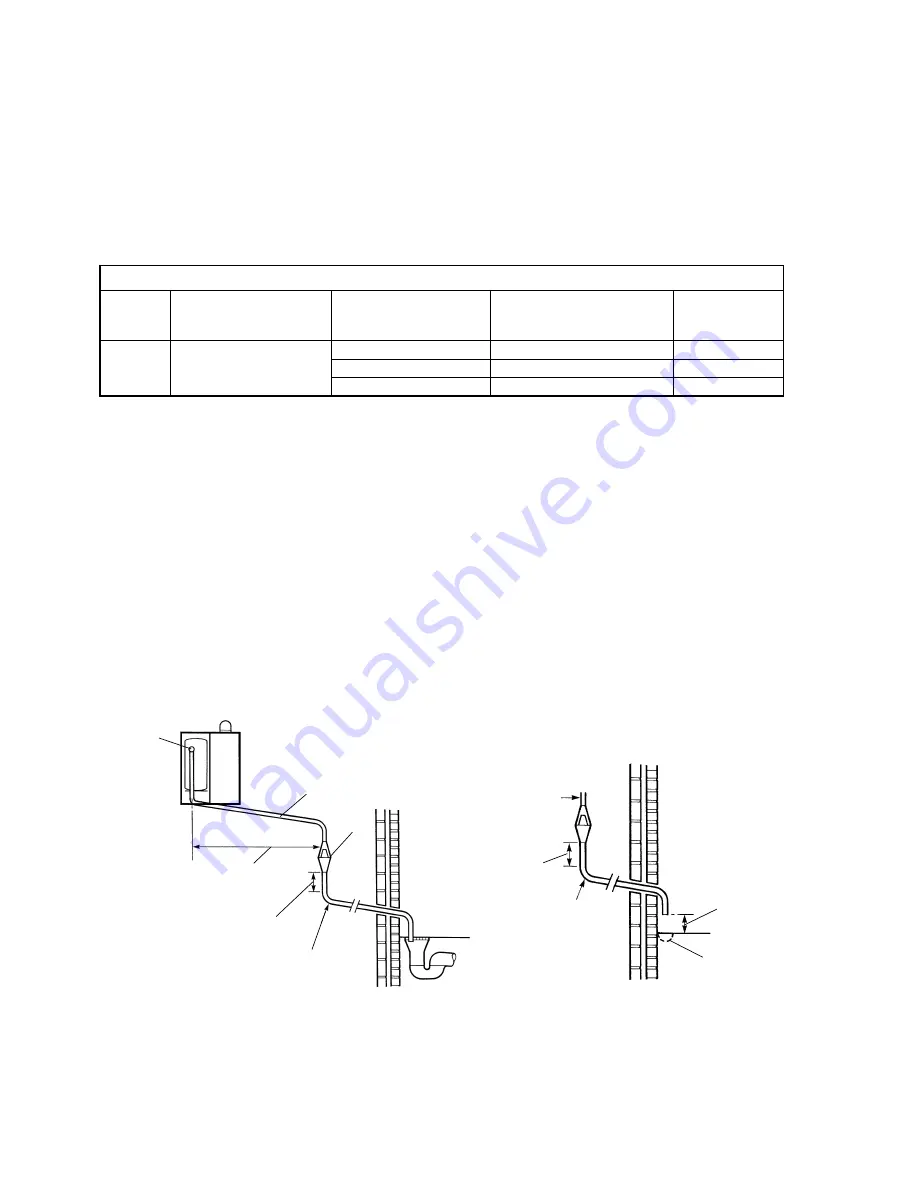
6
Alpha CombiMax 350 and 600
3.4
UNVENTED HOT WATER STORAGE SYSTEM
The installation is subject to Building Regulations approval and the Local Authority must be notified of the intent to install.
The CombiMax store is supplied with the components required for an unvented hot water system, i.e. temperature/pressure and
expansion relief valves, expansion vessel, check valve and tundish. All these components are factory fitted, except for the expansion
vessel, which is to be connected to the top of the storage cylinder after installation, and the tundish which must be installed as follows:-
Discharge pipe - The discharge pipes from both the temperature/pressure and expansion relief valves have been joined together
within the appliance. The combined discharge pipe from the appliance must be routed to the tundish supplied in 15 mm pipe.
Tundish - The tundish must be positioned within 500 mm of the appliance, so that it is visible to the User and away from electrical
devices. The minimum size of the discharge pipe downstream of the tundish is given in the following table.
Fig. 1a
300 mm
minimum
Tundish
500 mm max.
from appliance
Metal discharge pipe (D2) from
tundish with continuous fall
Metal discharge pipe (D1)
from relief valves to tundish
Temperature/pressure
relief valve
300 mm
minimum
100 mm max.
70 mm min.
Gulley if
available
Pipe close to wall to
allow water to fan out
safely
Ground level
D2
D1
LOW LEVEL TERMINATION
Resistance created
by each elbow
or bend
0.8 m
1.0 m
1.4 m
Maximum resistance allowed,
expressed as a length of straight
pipe (i.e. no elbows or bends)
up to 9 m
up to 18 m
up to 27 m
Minimum size of discharge
pipe 'D2' from tundish
22 mm
28 mm
35 mm
Minimum size of discharge
pipe 'D1' to tundish
15 mm
Valve
outlet size
G½
Sizing of copper discharge pipe 'D2' - refer also to Figs. 1a and 1b
The discharge pipework from the tundish:-
a. Shall fall continuously through its length.
b. Shall be of a heat resistant material, e.g. metal.
c. Shall not be fitted with any valves or taps.
d. Shall discharge to a safe visible position, e.g. onto the surface of an external wall or into a gulley.
e. Shall have a minimum of 300 mm straight pipework directly from the tundish.
Note: Where children may play or otherwise come into contact with discharges, a wire cage or similar guard must be
positioned to prevent contact whilst maintaining visibility.
Refer to Figs. 1a and 1b for suggested methods of terminating the discharge pipe safely.
Where a single pipe serves a number of discharges, such as in blocks of flats, the number served should be limited to not more
than 6 systems so that any installation can be traced reasonably easily. The single common discharge pipe should be at least
one pipe size larger than the largest individual discharge pipe to be connected.
If the system is installed where discharges from safety devices may not be apparent, i.e. in dwellings occupied by blind, infirm or disabled
people, consideration should be given to the installation of an electronically operated device to warn when discharge takes place.