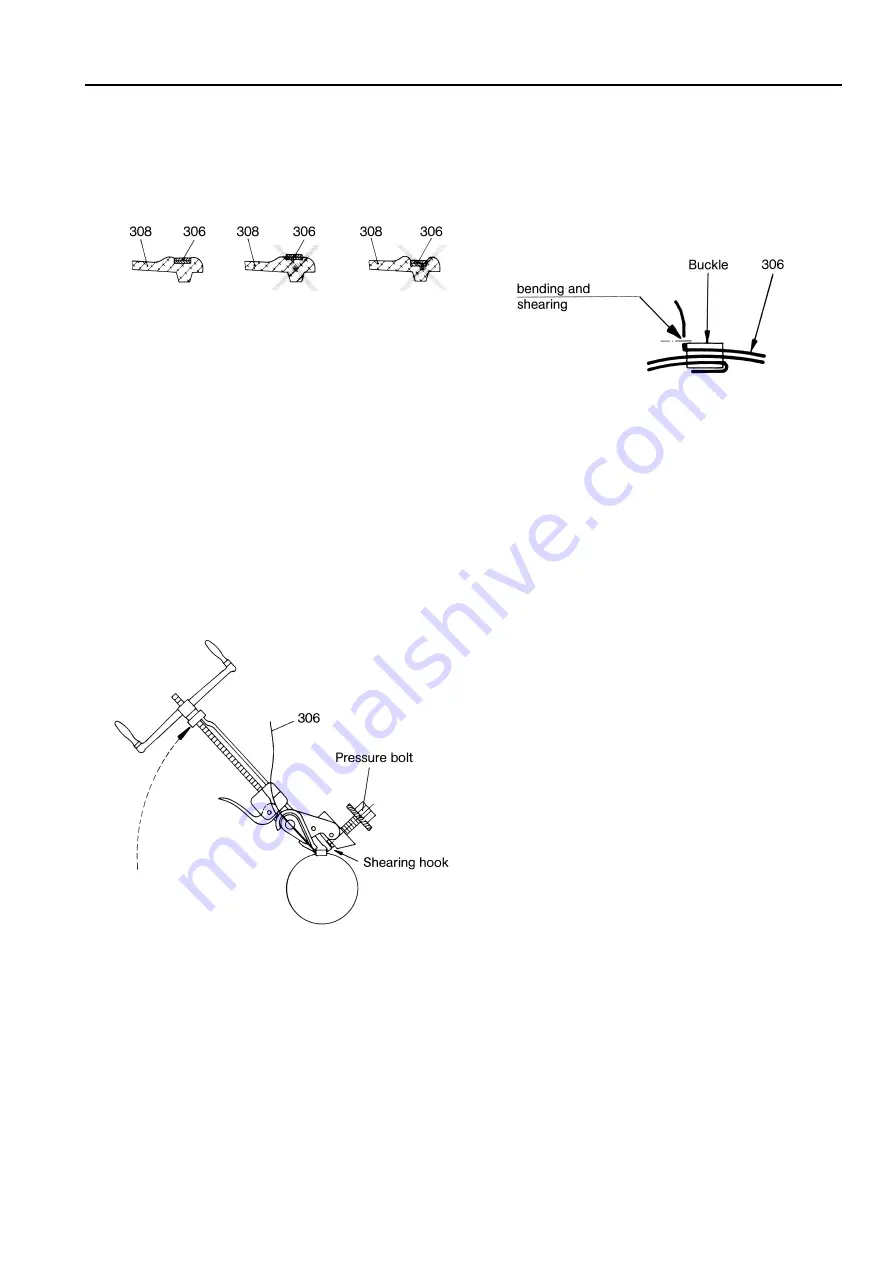
x
Clamping with clamping tool Pok-It II
– When using clamping tool PoK-It II, bend clamping
band (306) after clamping at the clamping band
buckle by swinging the clamping tool so that the
band cannot glide back through the buckle. After
bending at the clamping band buckle, the clamping
band must be sheared with sheet metal shears and
the cutting edges deburred (please refer to Figure 12
below).
Figure 12: Bending and shearing of the clamping band.
B
Check whether the clamping band is
bent so that it cannot glide back
through the clamping band buckle (please refer to
Figure 12 above). If this was not achieved, the clamping
band must be removed and replaced by a new one.
7.2.2.4 Mounting the coupling rod and drive-side joint
– Mount drive-side joint as described under Section
7.2.2.3 above against the drive shaft (118) and/or hol-
low shaft (125).
– In doing so, push coupling rod into the joint head of
the drive shaft (118) and/or hollow shaft (125).
– Secure retaining sleeve (304) as depicted with a cen-
ter punch mark.
– Mount cover sleeve (308), fill joint space with joint
lubricant (305) and fix clamping bands as described.
– Insert gasket for discharge casing (511).
– Push discharge casing (504) over the rotor (401). In
doing so, make sure that the precision-machined
rotor is not damaged.
– Fix discharge casing (504) with hexagon screws
(617), spring ring (619) and hexagon nuts (618) to the
bearing bracket (110) and/or lantern (122).
– Tighten socket-head cap screw (620) and check by
means of hexagon nut (626).
Note:
Prior to tightening the socket-head cap screw
(620), attend to proper position of the connections in
the shaft sealing housing (204) and/or mechanical
seal housing (214).
– Mount vent line for mechanical seal (224).
7.2.2.5 Mounting the stator
– Prior to mounting, coat stator (402), rotor (401) and
O-ring (517) with lubricant (silicon oil, Polydiol, soft
soap or the like).
B
Do not use ordinary oil.
– Mount stator (402) on the rotor (401).
Note:
In case of stiffness, simultaneously turn stator
(402) by means of chain tongs. For these purposes,
fix drive shaft (118) and/or hollow shaft (125).
– Mount O-ring (517) and stator shell (516).
– Screw up discharge casing (504), stator (402) and
suction cover (505) with the tie rods (611) and hexa-
gon nuts (609). In doing so, uniformly tighten hexa-
gon screws.
Wrong
Clamping band
(306) too tight.
Sleeve is dam-
aged/sheared.
Figure 10: Clamping of clamping bands.
– Check whether on the entire circumference of the
cover sleeve (308), the clamping band (306) lies in
the sleeve groove.
– Slowly turn clamping tool upwards through approx.
60
h
until the shearing hook grips behind the clamping
band buckle (please refer to Figure 11 below).
– Tighten pressure screws by hand until the clamping
band is firmly clamped.
Figure 11: Shearing of the clamping band.
– By means of a spanner or ratchet, turn pressure
screw clockwise until the clamping band is sheared.
B
If the clamping band is slightly lifted
on the sheared side, this must be
compensated for by careful realignment. Hammering
or beating against the clamping band buckle is not
permitted as otherwise, there may be a danger of
sleeve damage.
Note:
In case of clamping bands of Hastelloy mate-
rial, shearing with the clamping tool is not possible.
After bending at the clamping band buckle, the clam-
ping band must be sheared by means of sheet metal
shears and the cutting edges deburred (please refer
to Figure 12 below).
Series SLTP, SETP, SNTP, SLTBP, SETBP, SNTBP
ALLWEILER
a
13
Note:
Proper clamping of the clamping bands (306) is
shown in Figure 10.
Correct
Clamping band
(306) has
slightly drawn in
sleeve outside
and fits tight.
Wrong
Clamping band
(306) too loose,
may glide down.