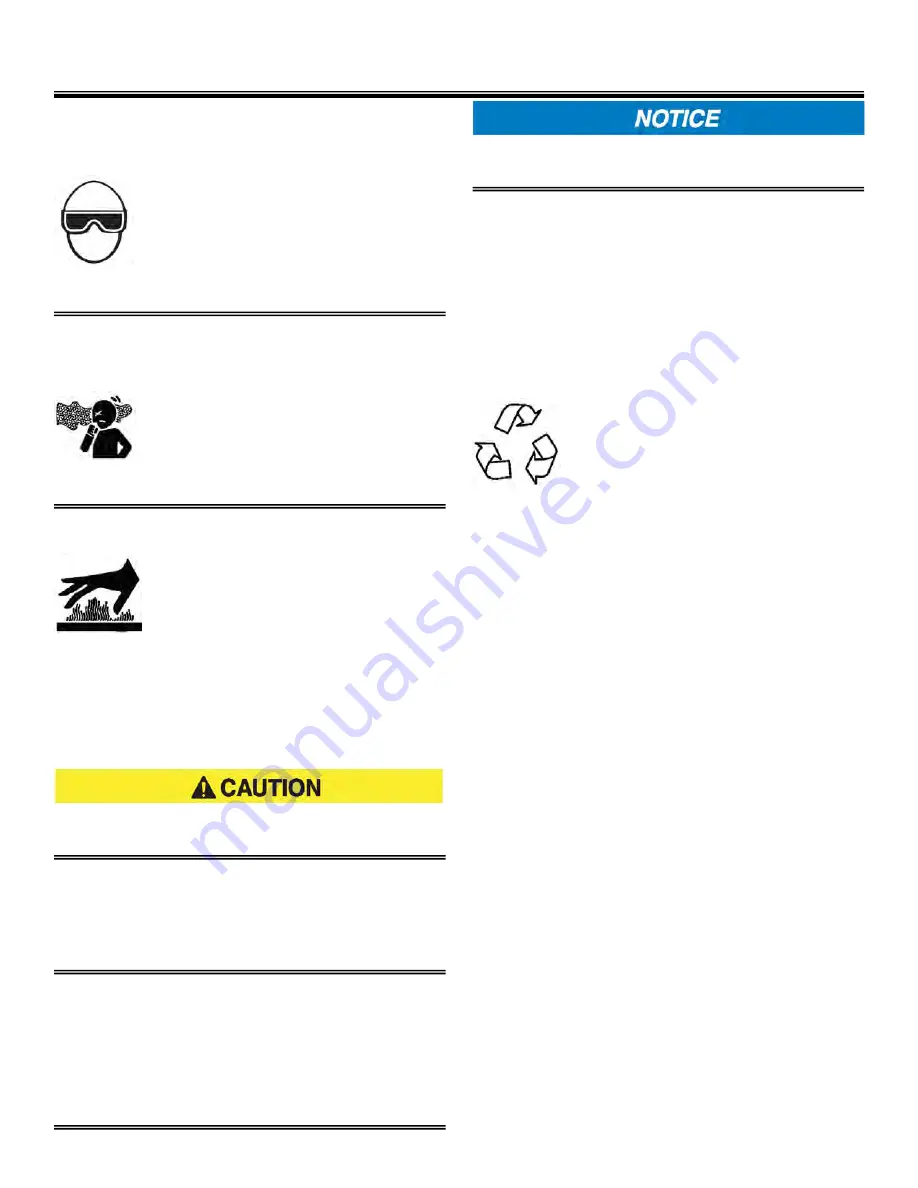
10
SAFETY
FLYING OBJECT HAZARD
Always wear eye protection when
cleaning the equipment with
compressed air or high pressure
water. Dust, flying debris,
compressed air, pressurized
water or steam may injure your
eyes.
COOLANT HAZARD
Wear eye protection and rubber
gloves when handling engine
coolant. If contact with the eyes or
skin should occur, flush eyes and
wash immediately with clean
water.
BURN HAZARD
light fixtures and some of the
engine surfaces become very hot
during operation and shortly after
shutdown.
Keep hands and other body parts away from
hot engine surfaces.
Handle hot components, such as light
fixtures, with heat resistant gloves.
The safety messages that follow have
CAUTION level hazards.
TOOL HAZARD
Always use tools appropriate for the task at
hand and use the correct size tool for
loosening or tightening equipment parts.
SLIP HAZARD
Immediately clean up any spilled liquid on
the shop floor.
Clean up accumulated dirt and debris on the
shop floor at the end of each shift.
The safety statements that follow have
NOTICE level .
Any part which is found defective as a result
of inspection or any part whose measured
value does not satisfy the standard or limit
MUST be replaced.
Always tighten components to the specified
torque. Loose parts can cause equipment
damage or cause it to operate improperly.
Only use replacement parts specified.
Other replacement parts may effect
warranty coverage.
Clean all accumulated dirt and debris away
from the body of the equipment and its
components before you inspect the
equipment or perform preventative
maintenance procedures or repairs. Oper-
ating equipment with accumulated dirt and
debris will cause premature wear of
equipment components.
Never dispose of hazardous materials by
dumping them into a sewer, on the ground,
or into groundwater or waterways.
Retrieve any tools or parts that may have
dropped inside of the equipment to avoid
improper equipment operation.
Follow the guidelines of the EPA
or other governmental agencies
for the proper disposal of
hazardous materials such as
engine oil, diesel fuel and engine
coolant.
If any alert indicator illuminates during
equipment operation, stop the engine
immediately. Determine the cause and re-
pair the problem before continuing to oper-
ate the equipment.
Not
for
Reproduction
Summary of Contents for MAXI-LITE AS3000
Page 46: ...46 MAINTENANCE RECORD DATE SERVICE DESCRIPTION SERVICED BY N o t f o r R e p r o d u c t i o n...
Page 47: ...47 SCHEMATICS N o t f o r R e p r o d u c t i o n...
Page 48: ...48 SCHEMATICS N o t f o r R e p r o d u c t i o n...
Page 49: ...49 SCHEMATICS N o t f o r R e p r o d u c t i o n...
Page 50: ...50 SCHEMATICS N o t f o r R e p r o d u c t i o n...
Page 51: ...51 SCHEMATICS N o t f o r R e p r o d u c t i o n...
Page 52: ...52 WARRANTY N o t f o r R e p r o d u c t i o n...
Page 53: ...53 WARRANTY N o t f o r R e p r o d u c t i o n...