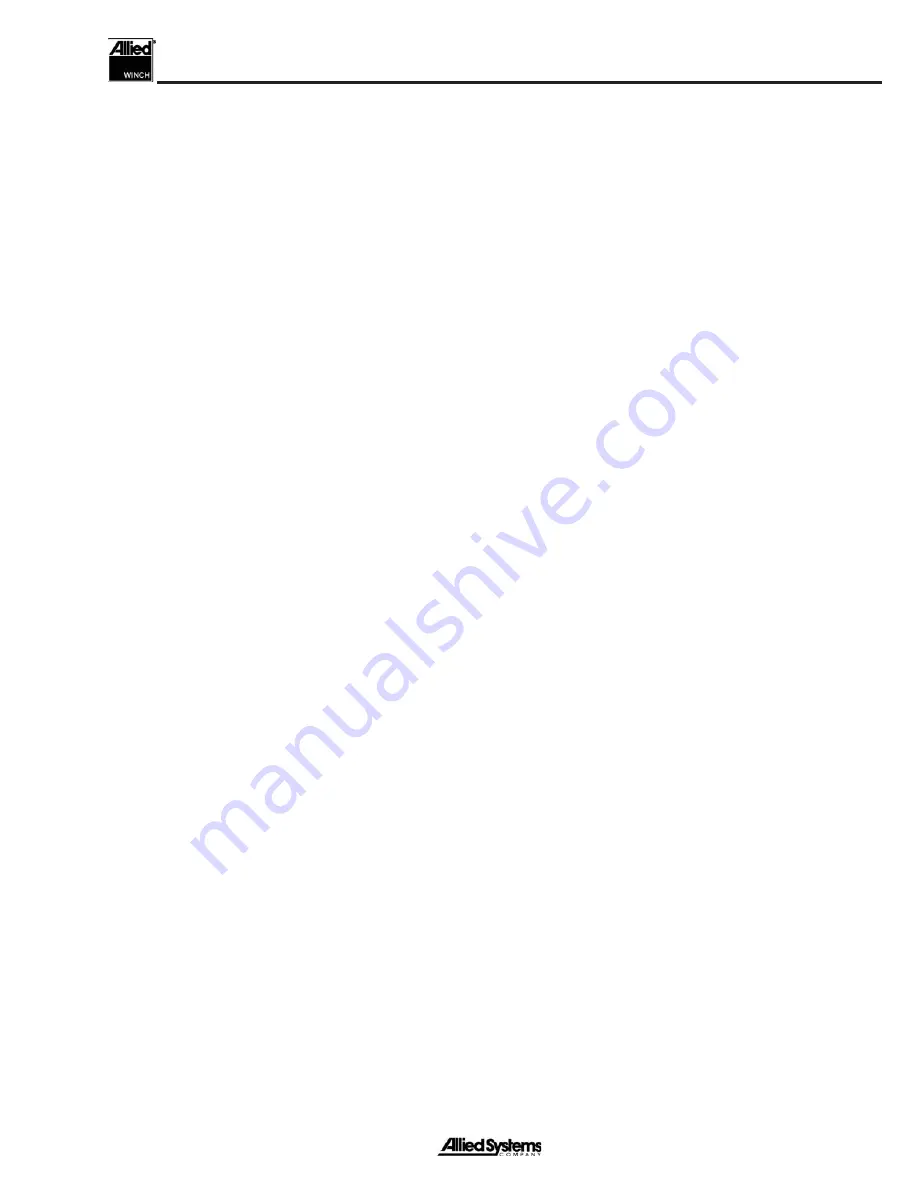
Section 3
3 - 3
3.
Leaking pressure hoses or fi ttings
Maximum Pilot Supply Pressure Check
With the same gauge installed from the Standby Pilot
Pressure Check, bottom tractor blade cylinders and
measure Relief Pilot Supply Pressure. When the tractor
pump senses a load, the maximum pilot supply pressure
is reduced to the setting of the tractor pilot reducing valve.
Excessive pilot supply pressure may cause damage to
tractor and winch components.
If pressure is not as specifi ed in Figure 3-5, check the
following:
1.
Improper pilot supply reducing valve setting or mal-
function (See tractor Service Manual)
2.
Leaking pressure hoses or fi ttings
Counterbalance Valve Pressure Check
With the engine shut off, connect one 5000 psi pressure
gauge to Motor Port B. Start the engine and place control
lever in
LINE-OUT
to build pressure against the counter-
balance valve. Check pressure as indicated in Figure 3-5.
Pressure on the B side of the motor is a ratio of the relief
setting of the counterbalance valve. If pressure is not as
specifi ed in Figure 3-5, do not adjust valve until remaining
pressure diagnostics are performed and other problems
are identifi ed.
Counterbalance Valve Adjustment:
1.
Start engine and place control lever in
LINE-OUT
position until drum just being rotating.
2.
Measure pressure at Motor Port B.
3.
Loosen counterbalance valve locknut. Turn counter-
balance valve adjusting capscrew IN to decrease
pressure and OUT to increase pressure. Adjust
pressures as shown in Figure 3-5.
Motor Supply Pressure Check
With the engine shut off, connect one 5000 psi pressure
gauge to Motor Port A and one 5000 psi gauge to Motor
Port B. Disconnect and plug the brake release hose from
the brake. This will lock the winch brake to build pressure
in the motor. Check pressure as indicated Figure 3-5. If
pressure is too high adjust the load sense relief valve. If
it is too low proceed with pressure diagnostics to identify
other possible problems. A damaged motor or pump can
cause low pressure at the motor.
Load Sense Valve Adjustment:
1.
Leave the brake pressure supply disconnected.
2.
Start the engine and operate the winch in
LINE-IN
or
LINE-OUT
.
3. Measure the pressure at Motor Port A for
LINE-IN
or Port B for
LINE-OUT
.
4.
Loosen load sense valve locknut. Turn adjusting cap-
screw OUT to decrease pressure and IN to increase
pressure. Adjust pressures as shown in Figure 3-5.
5. Reconnect brake pressure supply hose.
NOTE: Port B pressure may be lower than Port A, but
it will not affect winch performance.
Brake Pressure Check
With the engine shut off, connect one 1000 psi pressure
gauge to the BR pressure test port on the logic control
manifold. Start the engine and operate the winch in
LINE
-IN
and
LINE-OUT
. Check pressure as indicated Figure
3-5. The brake requires a minimum of 200 psi to release.
Low pressure will result in premature wear of the friction
discs and added heat generation.
If the brake pressure is not as specifi ed in Figure 3-5,
check for:
1.
Improper pilot supply pressure.
2.
Malfunctioning control lever; low RI and/or RO pres-
sure.
3.
Leaking pressure hoses or fi ttings.
4.
Restriction in pressure hose or manifold port.
Brake Valve Pressure Check
With the engine shut off, connect one 1000 psi pressure
gauge to the BR pressure test port and one 1000 psi
pressure gauge to the RI pressure test port on the logic
control manifold. Start the engine and slowly meter the
control lever into the
LINE-IN
position while monitoring
both gauges. BR pressure will jump to full pilot supply
pressure when RI reaches the RI pilot setting of the valve.
Check pressure as indicated Figure 3-5. The brake valve
sets the overlap between the hydraulic motor drive and
brake release. A low setting on the brake release valve will
release the brake before the motor begins driving. A high
setting on the brake release valve will momentarily drive
Summary of Contents for H6G
Page 6: ...iv Notes ...
Page 8: ...vi Notes ...
Page 22: ...General 1 14 Figure 1 16 Hydraulic System LINE IN ...
Page 24: ...General 1 16 Figure 1 17 Hydraulic System HI SPEED LINE IN ...
Page 26: ...General 1 18 Figure 1 18 Hydraulic System LINE OUT ...
Page 28: ...General 1 20 Figure 1 19 Hydraulic System HI SPEED LINE OUT ...
Page 30: ...General 1 22 Figure 1 20 Hydraulic System FREESPOOL ...
Page 32: ...General 1 24 Notes ...
Page 33: ...Section 1 1 25 Figure 1 22 H6G Schematic ...
Page 34: ...General 1 26 Intentionally Blank ...
Page 41: ...Section 2 2 7 Notes ...
Page 42: ...Troubleshooting 2 8 Notes ...
Page 49: ...Section 3 3 7 Notes ...
Page 50: ...Service 3 8 Notes ...
Page 57: ...Section 3 3 7 Notes ...
Page 58: ...Service 3 8 Notes ...
Page 77: ...Section 4 4 19 12 Remove the spool assembly ...
Page 109: ...Section 4 4 51 Notes ...
Page 110: ...Repairs 4 52 Notes ...
Page 111: ......