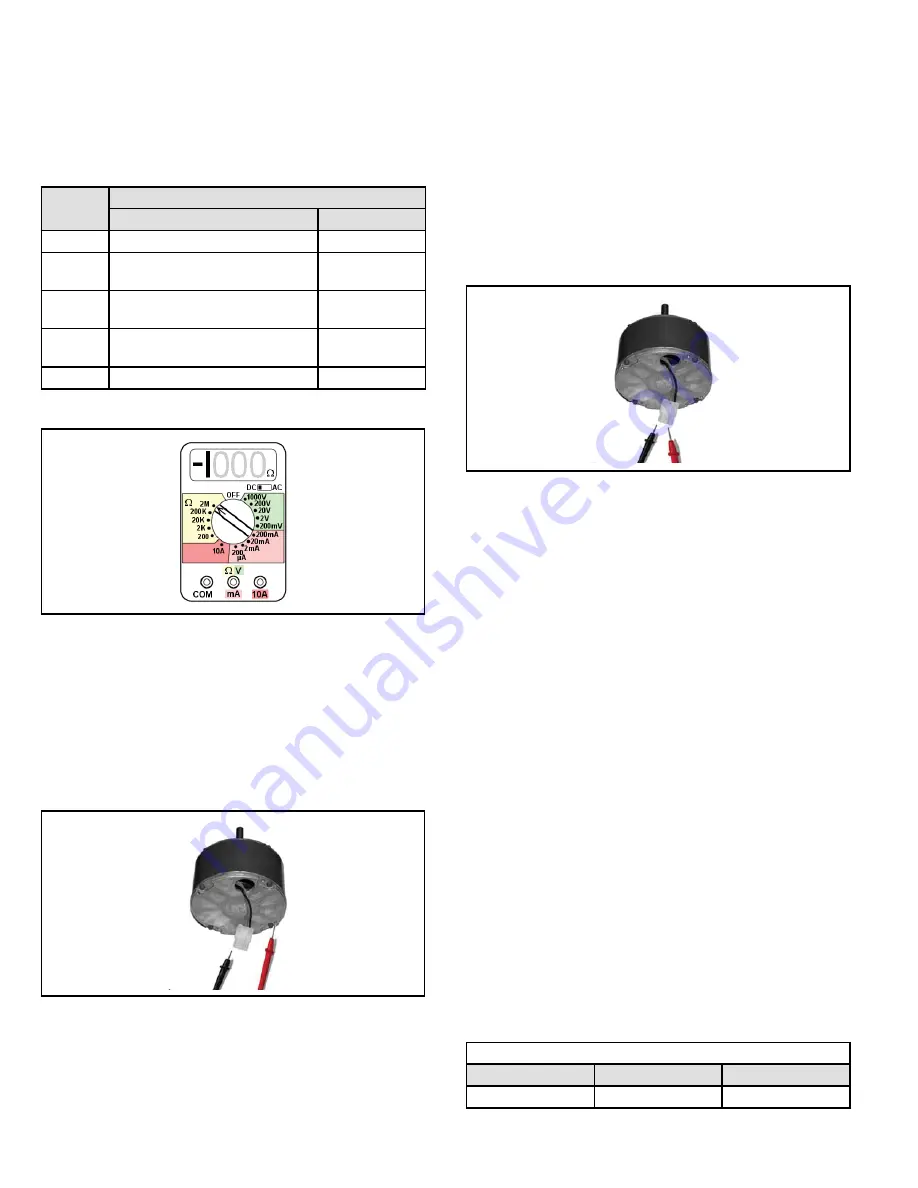
508151-01
Issue 2104
Page 22 of 72
Troubleshooting Motor Windings
Ensure that motor windings are not damaged by performing
the following tests:
NOTE:
If your ohm meter is not an auto-ranging type, set
it to the highest ohm scale (100k ohms or greater) before
performing tests.
Scale
Measurement Range
in Words
in ohms
2 M
two megohm-two million ohms
0 - 2,000,000
200 K
two hundred kilo-ohm-two
hundred thousand ohms
0 - 200,000
20 K
twenty kilo-ohm-twenty thousand
ohms
0 - 20,000
2 K
two kilo-ohm two-thousand ohms 0 - 2,000
200
two hundred ohms
0 - 200
Table 13. Ohm Meter Range
Figure 10.
TEST A
Measure the resistance between each of the three motor
leads (3-pin plug) and the unpainted part of the end shield.
If the winding resistance to ground is <100k ohms, replace
the motor and control module. If the resistance to ground
is >100k, the motor windings are fine. Proceed to Test B.
Figure 11. Test A
TEST B
Use an ohmmeter to measure the motor phase-to-phase
resistance by checking these combinations of the the 3-pin
motor plug. For the purpose of this test, start at either end
of the connector as lead 1.
1.
The lead-to-lead resistance across any two leads
should be less than 20 ohms.
2.
Each lead-to-lead resistance should be the same.
If the measured resistance is greater than 20 ohms, replace
the motor and control module.
Figure 12. Test B
Heating Components
Ignitor
The ignitor is made of durable silicon nitride. Ignitor
longevity is enhanced by controlling voltage to the ignitor.
The integrated control provides 120 volts to the ignitor for
a consistent ignition. Due to this feature of the control,
voltage measured with a digital meter will be slightly lower.
To measure correct voltage use a true RMS meter or ignitor
can be ohmed. Ohm value should be 39 to 70. See Figure
13 for ignitor location and Figure 15 for ignitor check out.
NOTE:
The A96DS2V furnace contains electronic
components that are polarity sensitive. Make sure that the
furnace is wired correctly and is properly grounded.
Flame Sensor
A flame sensor (Figure 13) is located on the left side of
the burner support. The sensor is mounted on the flame
rollout plate and the tip protrudes into the flame envelope
of the left-most burner. The sensor can be removed for
service without removing any part of the burners. During
operation, flame is sensed by current passed through the
flame and sensing electrode. The control allows the gas
valve to remain open as long as flame signal is sensed. To
check flame sense signal use the push-button found on the
integrated control and go to Field Test Mode. The menu
will display the flame signal. See Table 14 for flame signal.
Flame Signal in Microamps
Normal
Low
Drop Out
2.6 or greater
2.5 or less
1.1
Table 14.