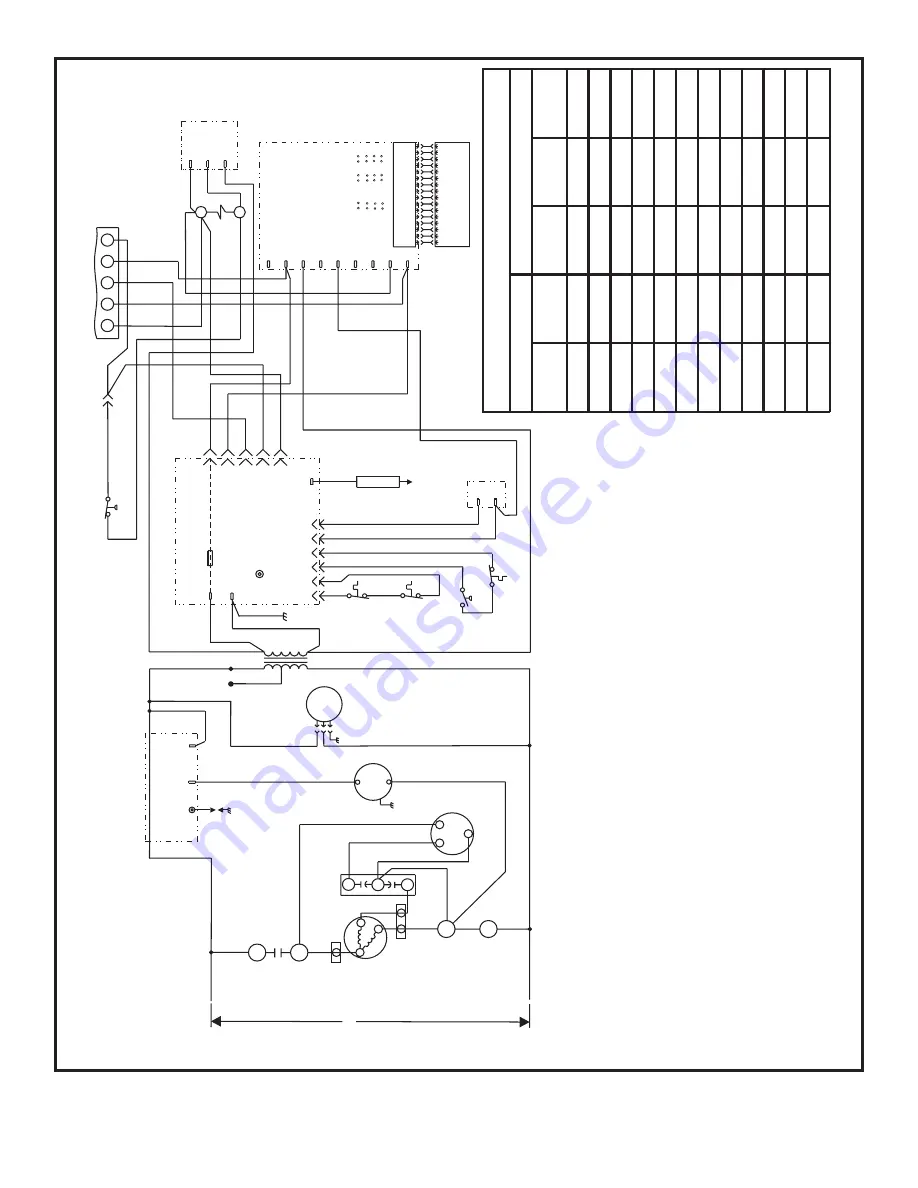
Page 16
506488-01
Issue 1008
Figure 12
208/230V
-1-60
1
2
3
4
5
6
7
8
9
10
11
12
13
14
15
16
1
2
3
4
5
6
7
8
9
10
11
12
13
14
15
16
Y
G
W1
R
C
Y
G
W
R
C
BLU
GRN
YEL
WHT
RED
Y
R
C
DIAGNOSTIC
MODULE
G
Y1
Y2
O
W1
EM
C1
R
HUM
INDOOR BLO
WER
MO
T
O
R
ICM BO
ARD
BLU
RED
24V
A
C
1
625
4
3
FLAME
FLAME
SENSE
GRY
BRN
BLU
ORN
RED
YEL
GRN
BLK
WHT
PUR
BLK
GRN
PUR
ORN
WHT
PUR
MAIN
LIMIT
SWITCH
R
OLLOUT
SWITCH
PRESSURE
SWITCH
A
UX.
LIMIT
SWITCH
(IF USED)
GAS
VA
LV
E
FUSE
IGNITION CONTR
OL
ORN
BLU
GRN
BLU
YEL
RED
RED
BLU
RED
YEL
CONT
A
C
T
O
R
THERMOST
A
T
YEL
YEL
HIGH PRESSURE
SWITCH
(IF USED)
L1
T1
T2
L2
C
H
F
CONDENSER
F
AN MO
T
O
R
COMPRESSOR
CONT
A
C
T
O
R
COMPRESSOR
CONT
A
C
T
O
R
DU
AL
CAP
A
CIT
OR
COMPRESSOR
TRANSFORMER
C
S
R
L1
CMB
BL
WR
SP
ARK
COMB
.
AIR
BLO
WER
IGNITION CONTR
OL
BLK
BLK
WHT
L2
L1
BLK
BRN
PUR
RED
RED
BLK
208V
240V
24V
INDOOR
BLO
WER
M
OTO
R
5 4 3
NO
TE:
IF ANY OF
THE ORIGINAL
WIRE IS REPLA
CED
,
THE
SAME SIZE AND
TYPE
WIRE MUST BE USED
.
USE
COPPER CONDUCT
OR ONL
Y
, MIN.
75°C
WIRE.
W
ARNING-
ELECTRIC SHOCK HAZARD
.
UNIT MUST BE GR
OUNDED
IN A
CCORD
ANCE
WITH NA
TIONAL AND LOCAL CODES
.
HEA
T ANTICIP
A
TION SETTING:
0.70 AMP
LINE
V
O
LT
A
GE FIELD INST
ALLED
SEE
BLO
WER SPEED
CHAR
T
BLK
S4
S1
K1
A3
GV1
S21
S18
S47
S10
T1
B3
B6
B4
K1-2
C12
B1
K1-1
A3
A54
B3
GR
OUND
BLU
YEL
A132
ADJUST
HEA
T COOL
NORM
(+)
(-)
(TEST)
A
B
C
D
A
B
C
D
DIA
GNOSTICS
The f
ollo
wing ignition control board LED codes will
indicate nor
mal or abnor
mal oper
ations:
SLO
W FLASH Nor
mal oper
ation, no call f
or heat.
F
AST FLASH Nor
mal oper
ation, call f
or heat.
2 FLASH System loc
k
out.
3 FLASH Pressure s
witch senses incorrect pressure
.
4 FLASH Main limit open or rollout s
witch open.
5 FLASH Flame sensed and gas v
alv
e not energiz
ed.
STEAD
Y Inter
nal f
ailure (micro-controller f
ailure;
self chec
k).
LED
YEL
E1
Blo
w
er
S
peed
C
har
t
Unit
F
a
c
tor
y
S
hipped
S
e
tt
ings
C
ooling
Input
Heat
ing
Input
AD
J
U
S
T
H
E
A
T
CO
O
L
24
68
NORM
A
B
30
68
NORM
A
A
36
68
NORM
B
A
36
90
NORM
A
A
42
83
NORM
C
C
42
110
NORM
C
C
48
83
NORM
C
B
48
110
NORM
C
B
48
138
NORM
A
B
60
83
NORM
C
A
60
110
NORM
C
A
60
138
NORM
A
A
A132
A132
BLK
Connection Diagram
Single Phase – V
ariable S
peed Motor
P/N 48107-001