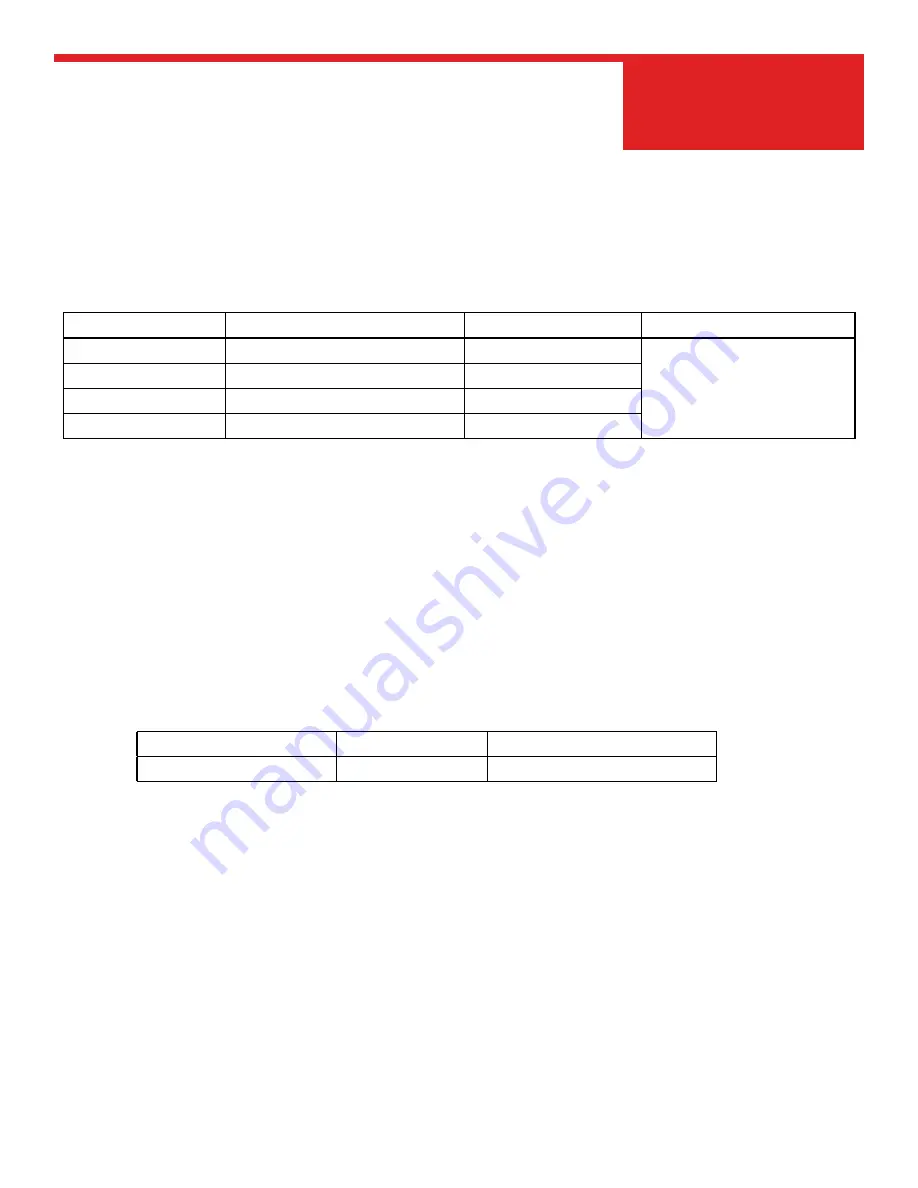
065300 - 09/2016
Page 49
SECTION 3
SERVICE
General Maintenance (cont’d)
•
With the vehicle stationary and the engine off, connect no.4
400 bar
full scale gauges to points
“1”, “2”, “3”
and
“4”
, start the endothermic engine and bring it to the max. power allowed
(3200
rpm for the petrol engine and 3600 rpm for the diesel engine)
.
•
Operate the drive lever corresponding to the track to the service of which the gauge has been
connected, taking care to block the piloted track and progressively bringing the drive lever
completely forwards or backwards.
GAUGE POSITION CORRESPONDING GEAR RELATIVE TRACK
PRESS. TO BE READ
1
forward
right
220 ÷ 240 bar
2
reverse
right
3
reverse
left
4
forward
left
•
The gauge set at points
“1”, “2” ,”3” or “4”
must indicate a pressure of
250 bar
.
ATTENTION!!!
WHEN TESTING THE 4 SERVICES, THE BOOST PRESSURE READ AT POINT
“5”
MUST REMAIN
UNALTERED, RANGING BETWEEN THE LIMITS INDICATED BELOW
(22 – 24 bar)
.
CHECK CHARGE PUMP PRESSURE
•
With the machine stopped and engine off, connect up a pressure gauge with bottom scale val-
ue
40 bar
to point
“5”
after which start the engine and run at max.rpm.
•
Under these conditions, the shown pressure should be
between 22 and 24 bar
.
GAUGE POSITION
FUNCTION
PRESS. TO BE READ
5
Charge pump
20 ÷ 22 bar
Summary of Contents for AT14S
Page 1: ...OPERATIONS PARTS MANUAL AT14S AT12L TRACK BUGGY MANUAL PART 065300 REVISION C ...
Page 16: ...065300 09 2016 Page 16 SECTION 1 SAFETY State Regulations Proposition 65 Warning ...
Page 17: ...065300 09 2016 Page 17 SECTION 1 SAFETY Federal Regulations Respiratory Hazards ...
Page 35: ...065300 09 2016 Page 35 SECTION 3 SERVICE General Maintenance cont d A 50 h C B ...
Page 54: ...065300 09 2016 Page 54 SECTION 4 PARTS Frame Assembly Illustration ...
Page 56: ...065300 09 2016 Page 56 SECTION 4 PARTS Hydraulic Tank Assembly Illustration ...
Page 58: ...065300 09 2016 Page 58 SECTION 4 PARTS Engine Assembly Illustration ...
Page 60: ...065300 09 2016 Page 60 SECTION 4 PARTS Hydraulic Pump Assembly Illustration ...
Page 62: ...065300 09 2016 Page 62 SECTION 4 PARTS Hydraulic Cooler Assembly Illustration ...
Page 64: ...065300 09 2016 Page 64 SECTION 4 PARTS Fuel Tank Assembly Illustration ...
Page 66: ...065300 09 2016 Page 66 SECTION 4 PARTS Wiring Assembly Illustration ...
Page 68: ...065300 09 2016 Page 68 SECTION 4 PARTS Operator Console Assembly Illustration ...
Page 70: ...065300 09 2016 Page 70 SECTION 4 PARTS Throttle Assembly Illustration ...
Page 72: ...065300 09 2016 Page 72 SECTION 4 PARTS Control Lever Assembly Illustration ...
Page 74: ...065300 09 2016 Page 74 SECTION 4 PARTS Control Lever Assembly Illustration ...
Page 76: ...065300 09 2016 Page 76 SECTION 4 PARTS Block Drainages and Servos Illustration ...
Page 78: ...065300 09 2016 Page 78 SECTION 4 PARTS Hood Assembly Illustration ...
Page 80: ...065300 09 2016 Page 80 SECTION 4 PARTS Bucket Valve Fitting Assembly Illustration ...
Page 82: ...065300 09 2016 Page 82 SECTION 4 PARTS Hydraulic Hose Assembly Illustration ...
Page 84: ...065300 09 2016 Page 84 SECTION 4 PARTS Decal Assembly Illustration ...
Page 86: ...065300 09 2016 Page 86 SECTION 4 PARTS Decal Assembly Illustration cont d ...
Page 88: ...065300 09 2016 Page 88 SECTION 4 PARTS Maintenance Tools Illustration ...
Page 90: ...065300 09 2016 Page 90 SECTION 4 PARTS Hourmeter Illustration ...
Page 92: ...065300 09 2016 Page 92 SECTION 4 PARTS Bucket Hydraulic Cylinder Assembly Illustration ...
Page 94: ...065300 09 2016 Page 94 SECTION 4 PARTS Swivel Hydraulic Cylinder Assembly Illustration ...
Page 96: ...065300 09 2016 Page 96 SECTION 4 PARTS Trilateral Tipping Bucket Assembly Illustration ...
Page 98: ...065300 09 2016 Page 98 SECTION 4 PARTS Trilateral Tipping Bucket Assembly Illustration cont d ...
Page 102: ...065300 09 2016 Page 102 SECTION 4 PARTS Hydraulic Tank Connections Illustration ...
Page 104: ...065300 09 2016 Page 104 SECTION 4 PARTS Control Plates Illustration ...
Page 106: ...065300 09 2016 Page 106 SECTION 4 PARTS Control Levers Illustration ...
Page 108: ...065300 09 2016 Page 108 SECTION 4 PARTS Manufacturer Plates Illustration ...
Page 110: ...065300 09 2016 Page 110 SECTION 4 PARTS AT12L Bucket Assembly Illustration ...
Page 112: ...065300 09 2016 Page 112 SECTION 4 PARTS Bucket Plate Illustration ...
Page 114: ...065300 09 2016 Page 114 SECTION 4 PARTS AT12L Bucket Chassis Illustration ...
Page 116: ...065300 09 2016 Page 116 SECTION 4 PARTS AT12L Hydraulic Tank Connections Illustration ...
Page 119: ...065300 09 2016 Page 119 SECTION 4 PARTS Notes ...
Page 120: ...065300 09 2016 Page 120 Hydraulic Schematic ...
Page 121: ...065300 09 2016 Page 121 Hydraulic Schematic cont d ...
Page 122: ...065300 09 2016 Page 122 Electrical Schematic ...