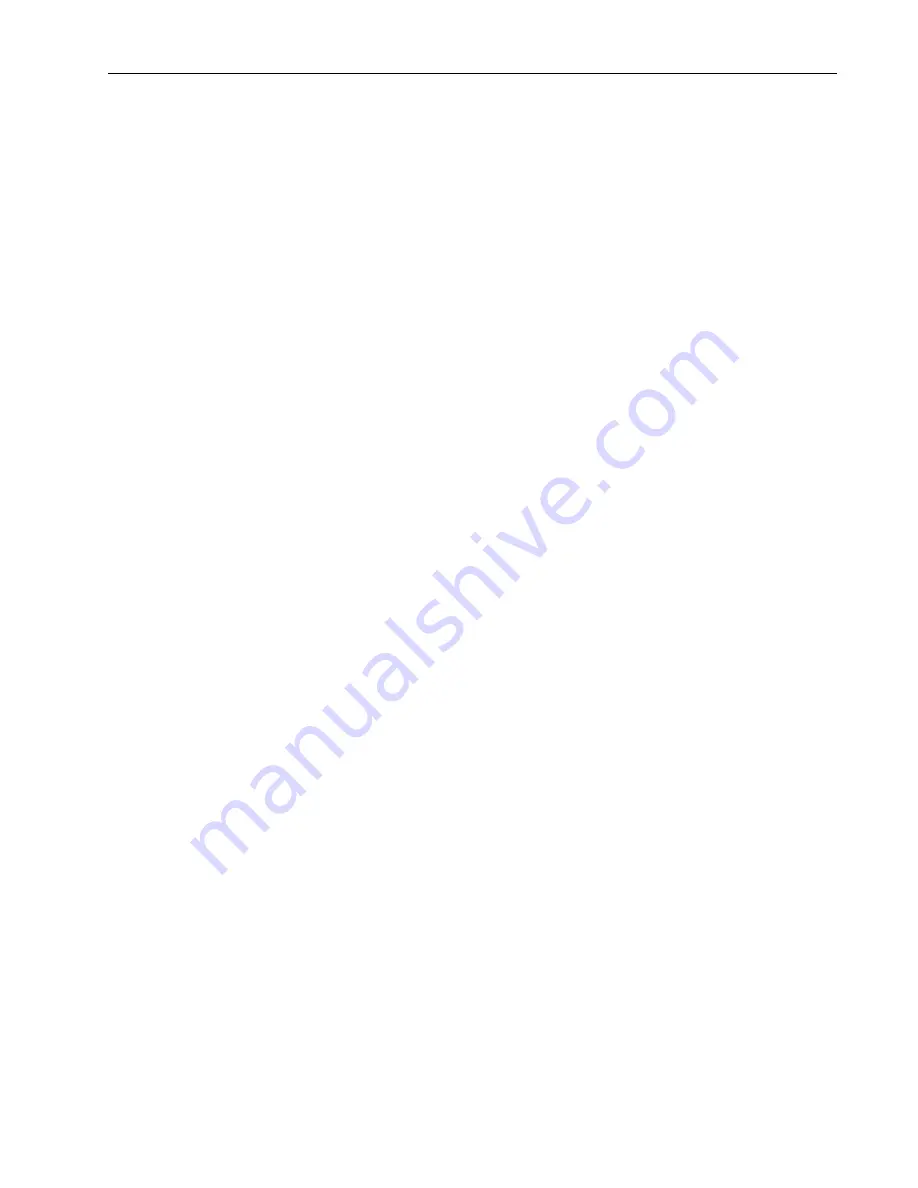
Process PID Loop
85
Using Scale Blocks with PID Reference and Feedback
Scale Blocks are included in the Reference and Feedback selections of the Process
PID controller. This selects the output of the scale block for use as Reference or
Feedback to the Process PID.
PID Setpoint
This parameter can be used as an internal value for the setpoint or reference for the
process. If [PI Reference Sel] points to this parameter, the value entered here will
become the equilibrium point for the process.
PID Error
The PID Error is then sent to the Proportional and Integral functions, which are
summed together.
PID Error Filter
[PI BW Filter] sets up a filter for the PID Error. This is useful in filtering out
unwanted signal response, such as noise in the PID loop feedback signal. The filter
is a Radians/Second low pass filter.
PID Gains
The [PI Prop Gain], [PI Integral Time] and [PI Deriv Time] parameters determine
the response of the PID.
Proportional control (P) adjusts output based on size of the error (larger error =
proportionally larger correction). If the error is doubled, then the output of the
proportional control is doubled. Conversely, if the error is cut in half then the output
of the proportional output will be cut in half. With only proportional control there is
always an error, so the feedback and the reference are never equal. [PI Prop Gain] is
unit less and defaults to 1.00 for unit gain. With [PI Prop Gain] set to 1.00 and PID
Error at 1.00% the PID output will be 1.00% of maximum frequency.
Integral control (I) adjusts the output based on the duration of the error. (The longer
the error is present, the harder it tries to correct). The integral control by itself is a
ramp output correction. This type of control gives a smoothing effect to the output
and will continue to integrate until zero error is achieved. By itself, integral control
is slower than many applications require and therefore is combined with
proportional control (PI). [PI Integral Time] is entered in seconds. If [PI Integral
Time] is set to 2.0 seconds and PI Error is 100.00% the PI output will integrate
from 0 to 100.00% in 2.0 seconds.
Derivative Control (D) adjusts the output based on the rate of change of the error
and, by itself, tends to be unstable. The faster that the error is changing, the larger
change to the output. Derivative control is usually used in torque trim mode and is
usually not needed in speed mode.
For example, winders using torque control rely on PD control not PI control. Also,
[PI BW Filter] is useful in filtering out unwanted signal response in the PID loop.
The filter is a Radians/Second low pass filter.